“ABC, Easy as 123!”
That's not just a catchy tune from the 70s, ABC inventory analysis really is that simple. It's also a great tool that helps businesses take control of their inventory management and make informed decisions (see what is inventory). Done properly, ABC analysis can lower costs and increase your bottom line.
If you don't already use ABC inventory analysis, you should. Here's what it is, how to do it, and the benefits it will bring to your business.
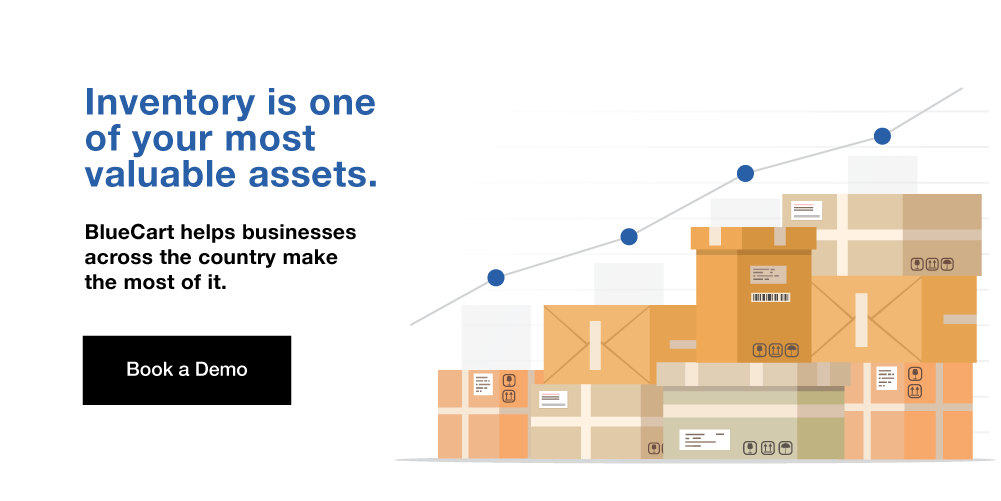
Let's Discuss ABC Analysis in Inventory Management
ABC analysis is one of a few valuable inventory management techniques that helps businesses determine which products are worth keeping in their inventory. It's also a skill that should be found on any warehouse manager resume. Using ABC analysis gives insight into your sales trends and each item's individual product value. It is used across all industries and requires little additional work. It also highlights areas where too much time and money are being spent on underperforming goods.
ABC Inventory Analysis Definition
ABC inventory analysis is a product categorization method where you bucket your products by their value and importance. This is done using the Pareto principle which states that 80% of inventory cost comes from just 20% of inventory.
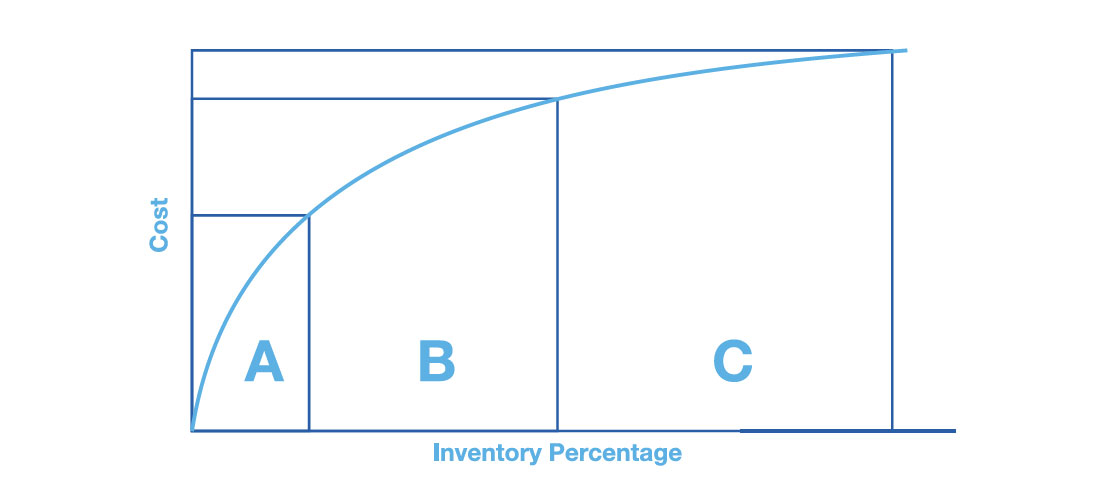
You can categorize your inventory into as many groups as you'd like, but most businesses use three buckets. These three buckets are: A, B, and C.
- A items are the most important. This inventory should get the most focus due to its high price, quick cycle inventory, or both. These items make up a smaller portion of your inventory, about 20%, but account for most of your consumption and you sell through it more quickly.
- B items are less important than As. These mid-tier products have lower prices than A items, but are more valuable than C items.
- C items are the least valuable. These products are also likely to be the most common in any warehousing environment, usually making up about 70% of inventory. They have long life cycles and offer little in the way of sales. They're the first choice when looking at inventory reduction.
Purpose of ABC Analysis in Inventory Management
The main purpose of ABC analysis of inventory control is to identify products with high cost of inventory so that management can concentrate on inventory items with high inventory cost. It gives business owners insight into inventory value and highlights areas where too little or too much time and energy is being used.
ABC inventory analysis is used to allocate time and energy toward managing goods in the following way:
- A items' sales and inventory fluctuations should be closely watched so that they can be optimized for sales.
- B items can normally be left alone until you perform your regular physical counts of inventory. They should be managed using normal inventory methods.
- C items need very little attention paid to them since they offer such little value to the business.
It is also useful in determining what products to reorder and how often you need to reorder each product. This is imperative if you use a fast-paced just in time inventory model or a slow-paced bulk shipping inventory model.
How ABC Analysis Is Useful in Inventory Management
ABC inventory analysis is very useful in inventory management as it identifies the keys areas worthy of your focus. Once your goods are separated into three buckets, you can determine workloads and inventory reordering plans.
For example, after performing an ABC analysis, you discover that you haven't been putting much effort behind marketing some of your 'A' products. You can now give them the attention they deserve and even intentionally backorder some to increase your revenue. The same goes for underperforming 'C' products, as you can stop wasting time and money on them.
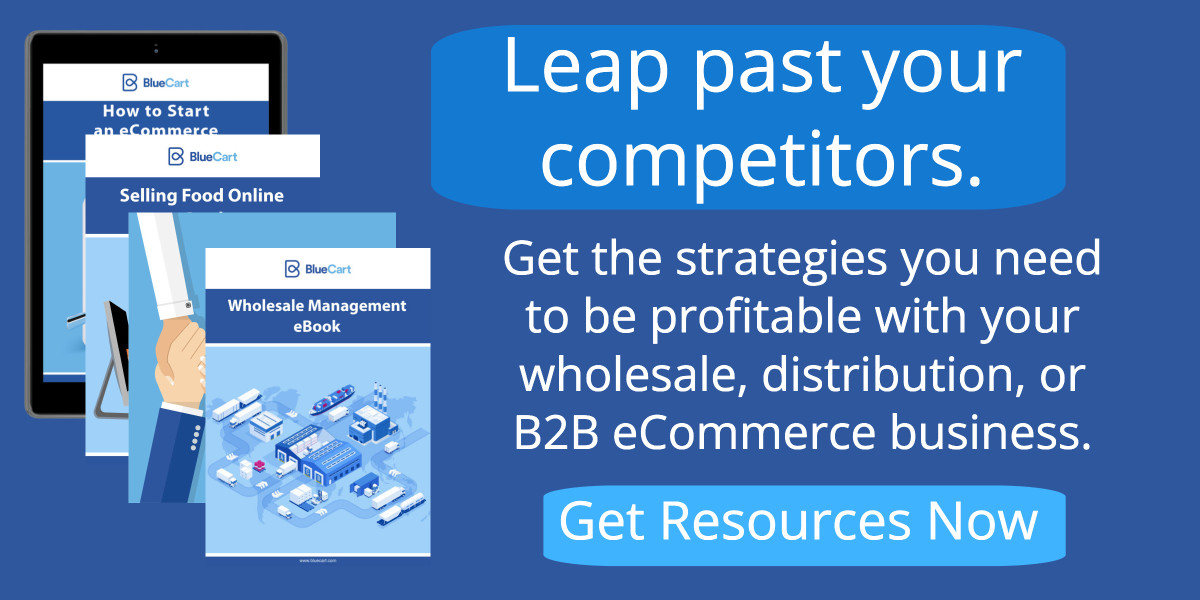
How to Use ABC Analysis in Inventory Management
Using ABC analysis in inventory management is very simple and can easily be done with the aid of any spreadsheet software. You can do an ABC analysis at any time as long as you have a full and accurate inventory count.
Here's how to perform an ABC inventory analysis:
- Calculate inventory value of a given item. To do this, you must use a formula to multiply the price of the item by the consumption value.
That formula is:
Item cost x annual consumption = inventory value
- Repeat step 1 for full inventory. Add all of these numbers together to discover your total inventory value.
- Sort items from high to low value. This can be done easily via an Excel spreadsheet like the one linked below.
- Calculate the percentage of total inventory value for each good. Again, this is done using a simple formula.
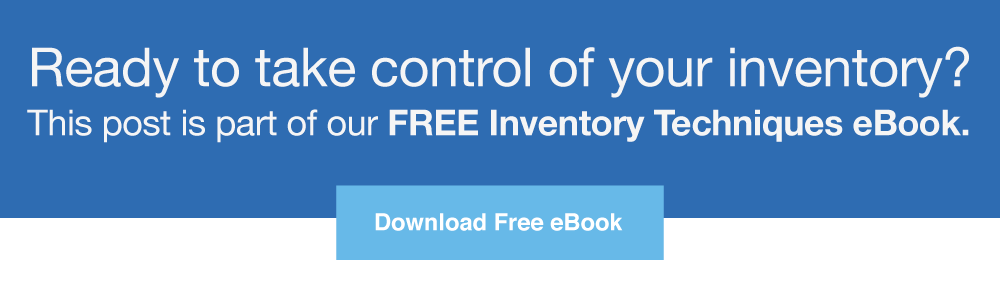
The formula is:
Item inventory value / sum of all inventory values = item % of total inventory value
- Add these goods to buckets A, B, and C. Do this by adding the highest 80% to group A, the next 15% to B, and the final 5% to C.
If you participate in kitting, ABC analysis can be done for both the kits themselves and the individual components. This will let you know if you have excess inventory of any part or are not investing enough in your best-performing kits.
Who Should Use ABC Inventory Analysis?
ABC Inventory analysis is useful across all industries and is commonly used by many retailers, wholesalers, and manufacturers. Raw materials inventory, merchandise inventory, and manufacturing inventory all have associated value to their respective businesses. This means that ABC inventory analysis can help these industries uncover their best and worst items and invest accordingly.
ABC inventory analysis can even be used on consignment inventory. It lets manufacturers determine what goods are worth keeping a buffer stock of in their consignment warehouses.
Inventory ABC Analysis in Excel
Since ABC inventory analysis is so helpful for inventory management, we've put together a free ABC analysis excel spreadsheet for you. It comes with some sample data to illustrate how to use the spreadsheet. Feel free to make a copy and begin using it to calculate inventory values and bucket your goods.
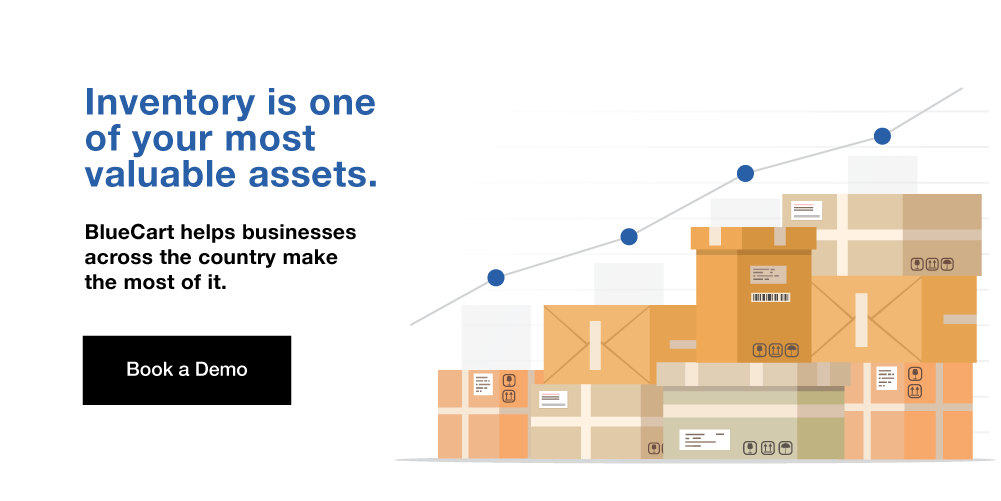
ABC What We Mean?
ABC inventory analysis is a valuable tool for any business. It provides deeper insight into your inventory value and lets you make informed decisions to increase profits, lower costs, and hit your target inventory KPI. If you manage an inventory, there really is no good reason not to perform ABC inventory analysis!
If you don't want to manage your inventory or use ABC inventory analysis, dropshipping might be the right choice for you. You can easily find suppliers in an online marketplace.