Inventory storage costs are one of any company’s most significant expenses during a product's life. In fact, storage costs can get as high as 67% of your total warehousing costs, especially if the product ends up as excess inventory or dead stock. This is where cross-docking comes in — saving you both time and money.
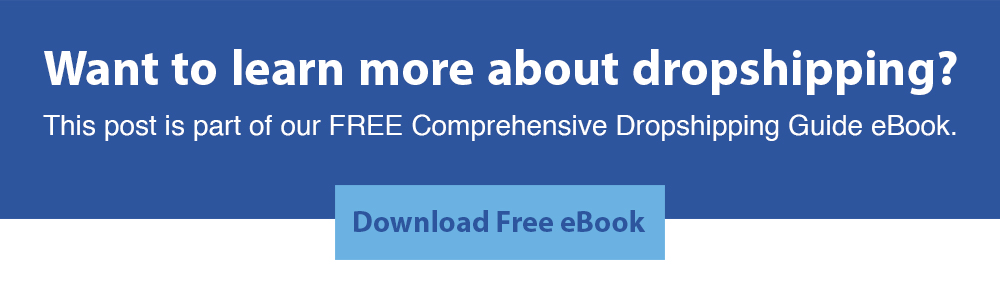
We'll walk you through the basics of what cross-docking is, how it works, and which companies benefit the most from this logistical process.
Cross Docking Definition
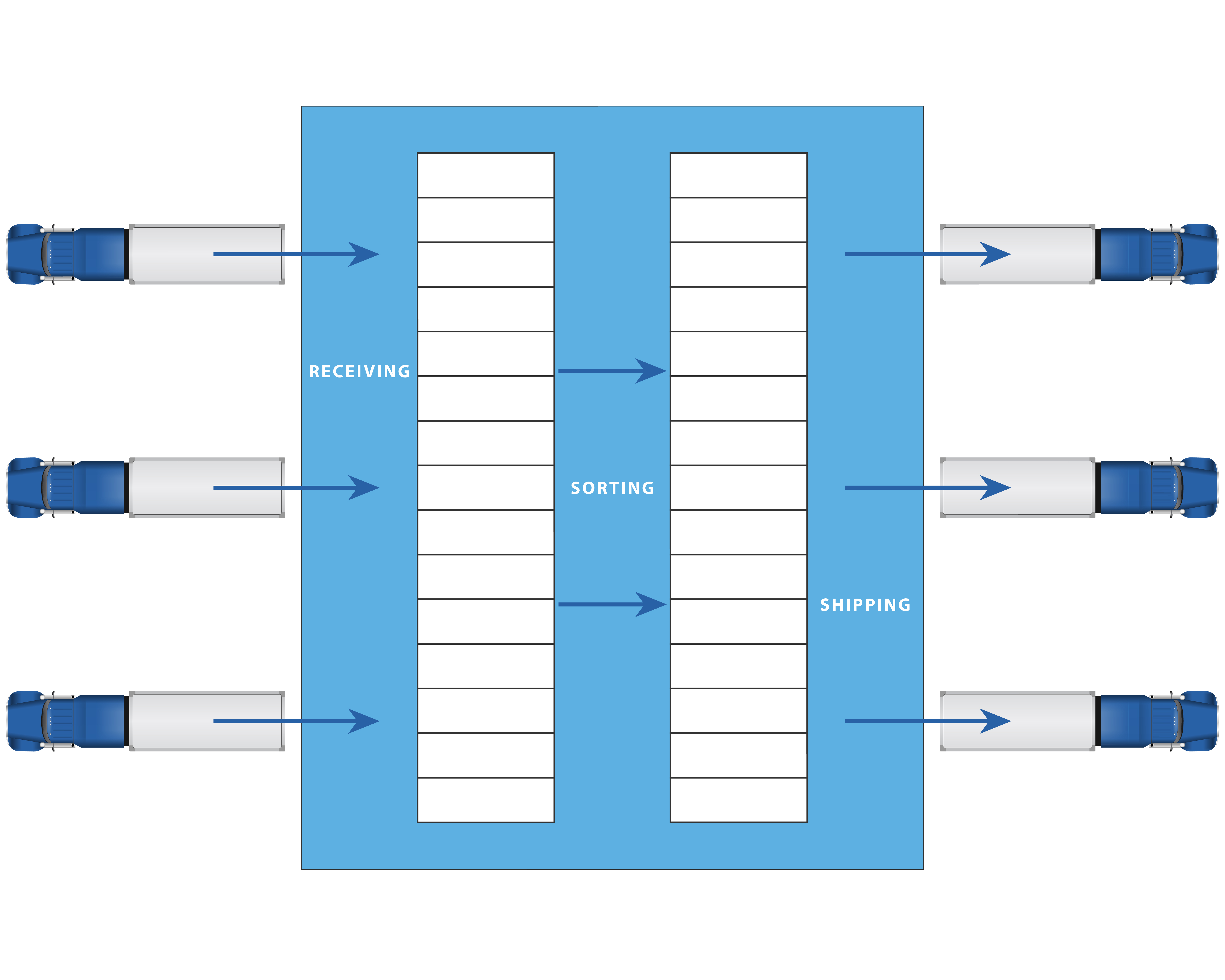
Cross-docking is an operational procedure where products are directly transferred from incoming to outbound transport. Unlike traditional warehousing, you do not typically handle or store any product.
Various types of crossdocking reduces inventory and operation costs by eliminating unnecessary handling and storage. The cross docking facility design is a layout that aims to organize the consolidation of available goods to prepare orders via delivery vehicles and loading equipment.
Cross docking allows the warehousing process to be broken down into smaller tasks, streamlining operations. For instance, if fulfillment activities are split or broken into smaller batches, staff members can get products shipped out to retailers much quicker.
Cross Dock Warehouse
Cross-docking usually occurs at a warehouse or distribution docking terminal, where trucks can continuously come and go. There are often two sides for inbound and outbound shipments, with a dedicated middle area to sort and pack inventory.
Simply put, shipments are received in the inbound dock from a truck, ship, or airplane. They are then moved to the middle area for sorting and inspection. Once completed, they are directly put on the outbound dock to be shipped off to customers. Most shipments typically spend less than 24 hours in a cross-dock before being sent to their final destinations.
Direct Shipment vs. Cross Docking
Direct shipping differs from cross-docking because products are sent directly from the supplier to the consumer. In most cases, the customer will purchase an item directly from the manufacturer. This method dramatically reduces transportation costs but requires extra logistical planning and storage space for the seller.
It's vital for suppliers to always have enough inbound products because they are shipping out items directly. They are even going as far as taking pre orders.
If they needed more inventory, they would either have to manufacture it or source it from a third party, resulting in a backorder and delayed shipping process times for the customer.
Direct shipping is popular with most apparel brands and many types of online businesses because they have complete control and visibility over what happens to the item before shipping.
This means they can ensure it's properly packed and protected against damage. Plus, they can choose the shipping method that best meets their needs. Whether they need flat rate shipping, expedited shipping, or overnight shipping, they can find a service that will get their items to their destination safely and on time.
Cross Docking vs. Drop Shipping
Cross-docking and drop shipping are very different inventory management techniques that keep inventory from sitting in storage in your warehouse. In cross-docking, the product shipped to your stockroom is sorted and immediately sent back to the customers. With drop shipping, items are directly sold from your supplier to your consumer, meaning you will never touch any of the items yourself.
It's important to have a good supplier relationship management strategy in place to make drop shipping work. This will help you keep track of your inventory and ensure that your customers are always happy with their purchases.
Drop shipping is a popular inventory management technique because the seller doesn't have to pay inventory holding cost for storage or any physical counts of inventory.
Like our shipping blog posts? You may also love our warehouse content. Check out our warehouse management eBook here.
Pre-Distribution vs. Post-Distribution Cross-Docking
There are two main types of cross-docking:
- Pre-distribution
- Post-distribution
Pre-distribution cross-docking involves receiving products at a central location and then distributing them to individual stores or customers. This method is often used by retailers who want to consolidate shipments and reduce inventory levels.
On the other hand, post-distribution cross-docking involves receiving products at individual stores or customers and then distributing them to other stores or customers. This method is often used by distributors who want to increase their delivery efficiency.
Both pre-distribution and post-distribution cross-docking can positively impact the overall efficiency of your supply chain. However, it is important to carefully consider which type of cross-docking will best meet the needs of your business.
Advantages & Disadvantages of Cross Docking
As with all logistical systems, a cross-docking system has both advantages and disadvantages.
Advantages of Cross Docking
- Reduces Storage Space: Companies generally spend between $4-7 per square foot of stockroom space. Cross-docking allows you to reduce your storage space, contributing to overall cost savings.
- Reduces Inventory Carrying Costs: It costs money to store, manage, count, secure, and insure inventory. Further, when inventory spoils or is damaged, you lose out on more money. Cross-docking reduces inventory costs because items go immediately from inbound to outbound transport, with little to no holding involved.
- Increases Overall Product Quality: Cross-docking reduces the risk of damage to your products because most items aren't stored in a warehouse. Damage occurs when you continuously move products in and out of storage, which eliminates the logistical process.
- Decreases Shipping Time: Cross-docking dramatically reduces the time it takes to ship items. It can also reduce the risk of needing LTL and 3PL shipment processes (see: 3PL Meaning). As soon as inventory reaches your cross docking warehouse, you move it swiftly from one truck onto another and ship it out to the customer.
Disadvantages of Cross Docking
- Process Is Time-Consuming: Cross-docking needs to be properly planned and executed to be successful. Shipments should not spend more than 24 hours in a stockroom or distribution center. This can help prevent scheduling conflicts and other mishaps that can happen when warehouse management systems are not in place.
- It's Expensive: Setting up a cross-docking operation isn't cheap. You would have access to much capital to set up a cross docking terminal and purchase many outbound trucks to service your business.
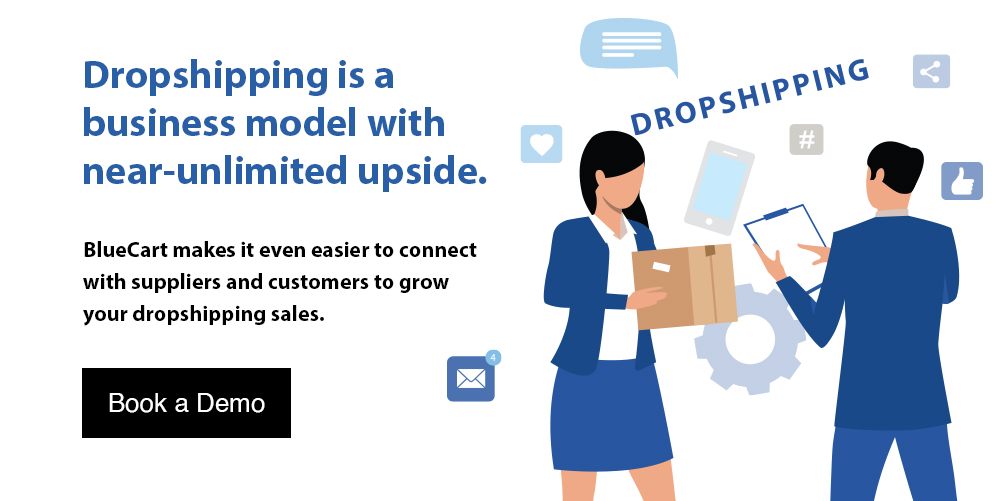
When Is Cross-Docking Used?
When shipping products to multiple destinations or consolidating shipments from various suppliers, it's important to learn how to calculate shipping costs. Cross-docking is used to improve shipping efficiency and minimize shipping costs. Cross-docking can also be used to ship products that are perishable or time-sensitive, such as wholesale produce, wholesale seafood, and shipping frozen meat.
For example, if a company needs to ship products to multiple retailers, it can use cross-docking to consolidate the shipments. This way, the company only has to make one trip to the retailer rather than numerous trips.
Cross-docking can also be used when a company ships products from multiple suppliers. In this case, the company can use cross-docking to consolidate the shipments from the different suppliers into one shipment.
Cross-docking can also be used to ship perishable or time-sensitive products. By cross-docking, companies can ensure that these products do not sit in a warehouse for an extended period. This is because cross-docking allows companies to ship products as soon as they are received without storing them in a warehouse.
Using Cross Docking Software
Continuous cross docking activities can do wonders for a business. With this said, you should invest in a WMS or an enterprise resource planning (ERP) system to run a successful cross-docking operation. The right software will analyze your data and create a management plan from scratch.
Ensure your WMS or ERP system has eCommerce analytics capabilities. This allows you to track your cross-docking performance and make necessary improvements. With the right software, you can run a successful cross-docking operation.
Most WMSs and top ERP systems have some or all of the following capabilities:
- Electronic Advance Ship Notice Transmission: Transmits data in real-time for inbound and outbound products.
- Barcode Scanning: Provides inventory accuracy by integrating computer data and UPC barcode scanners.
- Inbound and Outbound Freight Management Systems: Input data from received and shipped products.
- Workforce Planning: Helps track and schedule shipments to ensure all operations run smoothly.
Like our shipping blog posts? You may also love our warehouse content. Check out our warehouse management eBook here.
Companies That Use Cross-Docking
Cross-docking can be an extremely beneficial operational system. However, specific industries reap more rewards from cross-docking than others.
Here are the most common types of companies that use cross-docking:
- Food and Beverage Industry: Restaurants need steady supplies to operate smoothly. Cross-docking decreases the chances of any food spoilage because products move quickly through the supply chain, with no storage involved. In most cases, this is done within 24 hours. The minimal storage time is also beneficial for perishable goods.
- Consumer Goods: Due to big-name brands like Amazon and Walmart, most consumers expect goods in hand rapidly. Businesses now need to keep up and offer the same services consumers have grown accustomed to. Cross-docking helps companies move items faster and avoid costly storage fees.
- Automotive Industry: Cross-docking has been a staple of the automotive industry for decades because it relies on just in time delivery. This means that the production process only begins when a customer places an order and inventory stock is delivered as needed.
- Chemicals: Chemical products have specific storage requirements, making them both expensive and dangerous to ship. They should be handled as minimally as possible and be sent directly to the customer, which cross-docking allows.
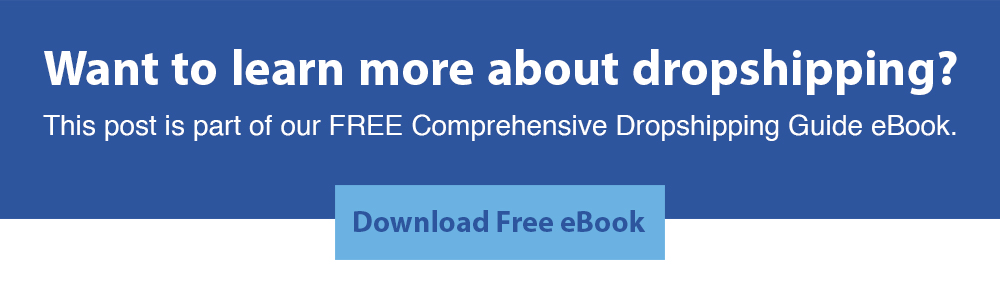
Don’t Cross the Streams
Now that you know about the different methods of cross-docking, you can decide whether this suits your company. The warehouse logistics of this procedure has many benefits, including lowering your overall costs and reducing your need for storage space.
If you go the cross-docking route, make sure you work with your supplier to create an operational plan so your inventory flows smoothly from one dock to the other. You can also look into the reverse dropshipping model, where margins are high, and you sell overseas.
Frequently Asked Questions About Cross Docking
What Is Cross Docking?
Cross docking is a process that involves products being transferred directly from incoming transport to outbound transport. This eliminates the need for storage and keeps inventory levels low. Cross docking can be used in various industries, including retail, manufacturing, and logistics.
What Is the Direct Shipment Definition?
Direct shipment is the method of shipping inbound goods directly from the manufacturer’s receiving dock to the consumer. This can reduce transportation and storage costs. It also benefits the receiving of purchased and inbound goods by moving items away from the stage area at a faster rate.
What are the Advantages of Cross Docking?
The advantages of cross docking are:
- Reduces inventory carrying costs and labor costs
- Reduces storage space
- Decreases shipping time
- Lessens the amount of material handling
- Increases product quality
What Are the Benefits Of Cross Docking?
Cross-docking offers many benefits, which include:
- Shorter shipping timelines
- Less product handling and storage
- Reduces various inventory costs
- Minimal storage requirements
- Lessens manual inventory handling
How To Implement Cross Docking?
To implement cross-docking, companies must utilize a docking terminal in a warehouse, where inbound goods are received and organized for deliveries. Then, these products are removed from their pallet, then transported via forklift or conveyor belt to their designated outbound delivery vehicles.
What Is Cross Docking In the Supply Chain?
Cross-docking in the supply chain is when you unload goods and move them to outbound delivery vehicles.
Cross-docking speeds up the process of supply chain operations, as warehouses ship finished goods much faster. In doing so, warehouses reduce many costs.
Was Cross Docking Perfected By Walmart?
Yes, Walmart has been perfecting the cross-docking process for a while. The freight that enters Walmart distribution centers is unloaded onto forklifts and conveyor belts, then moved onto outbound trucks. These trailers go on to travel to Walmart stores. By perfecting this method, Walmart can reduce stockroom storage requirements. Plus, cross docking works best for consumer goods.