Order, order in the warehouse!
When choosing what inventory models to implement for your business, economic order quantity should always be considered. It can help mitigate rising costs, streamline your warehouse operations, and put more money in your pockets.
Keep reading to find out how economic order quantity works, what benefits it brings, and how you can implement it in your own business.
.jpeg)
EOQ: What is Economic Order Quantity?
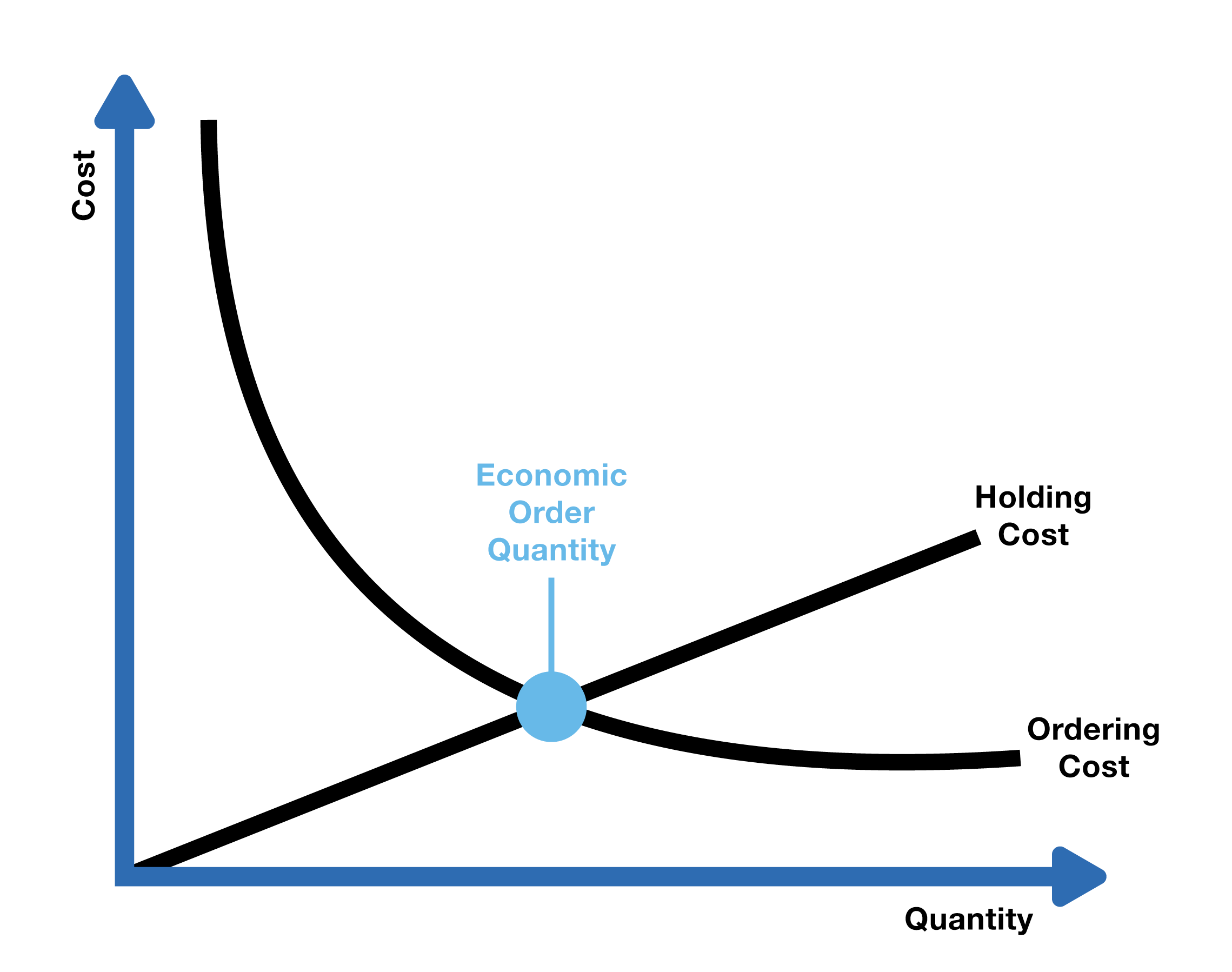
Economic order quantity (EOQ) is a production-scheduling method of inventory control that has been used since the early 1900s. This method is built around finding a balance between the amount you sell and the amount you spend on inventory management process.
Economic Order Quantity Definition
Economic order quantity is the ideal amount of product a company should purchase to minimize inventory costs. Essentially, it is the amount of product you should order to meet demand without having to store any excess inventory.
Optimal Quantity
The optimal quantity is the exact amount of inventory you should order and keep on hand to meet demand. Finding your optimal order quantity for a product is the goal of calculating its EOQ. However, this number is very difficult to achieve as any slight variance in demand, cost, or price will throw your numbers off.
Importance of Economic Order Quantity
Managing economic order quantity is an important skill to have when someone is vying for an inventory manager salary. It can help avoid issues like excess stock or dead stock (see what is dead stock) and keep avoidable losses to a minimum. It also helps you establish goals for your inventory KPIs, informs inventory forecasting decisions, and helps increase the company's sales and revenue.
Advantages of Economic Order Quantity
Utilizing EOQ for your business can provide many benefits. Here are just a few.
- Minimize costs. All warehouse inventory managers know that storage costs can quickly rise if inventory isn't controlled. By only ordering the amount needed to fulfill customer demand, these costs can be kept very low. This can be tough if your supplier requires an MOQ (what does MOQ mean?).
- Adapts to your business. Many inventory methods are only viable for certain types of business. EOQ utilizes only your own numbers, so it can benefit any business that uses it.
Economic Order Quantity Problems
Though there are definitely positive aspects of calculating EOQ, there are also a few drawbacks that you need to be aware of.
- The math is complicated. You'll see the formula used for EOQ calculations below, and it's safe to say it isn't the easiest to use. Luckily, there are many ways to automate the process and tools to help.
- It's based on assumptions. There are a number of assumptions that are required to calculate EOQ. This means any aspect of your business that doesn't match will throw off the numbers and you won't get the optimal quantity. Still, the numbers you find are very helpful for inventory planning.
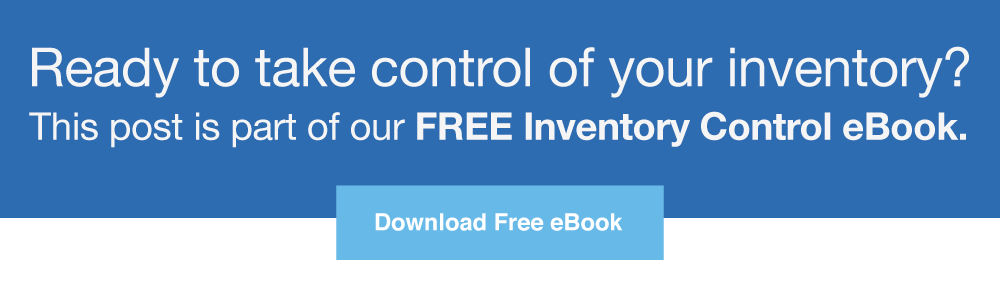
EOQ Formula: Economic Order Quantity Formula
Calculating economic order quantity requires you first find a few metrics regarding demand and costs. These are the annual demand for the product in units, the cost per order, and the annual holding cost per unit. Once you've collected this data, it's as easy as plugging them into the formula below.
How to Calculate EOQ
Uncovering the economic order quantity for a product can be done using a slightly complicated formula.
Here's that formula:
EOQ = √ (2 x Demand x Order Cost / Holding Cost)
Economic Order Quantity Formula and Example
If any of that seems confusing to you, let's clear it up a bit with an example.
Let's say you are a wholesale supplier for the food industry. You have a particular product you're looking to optimize, in this case cans of creamed corn. The first thing you do is look at your historical data regarding creamed corn.
After poring through your data, you calculate that you normally sell an average of 2,500 cans each year. You also look through your purchase orders and inventory costs to calculate that each shipment of 100 cans of corn costs $75. And you find that storage of each can costs you $20 per year.
With these variables in hand, you can now calculate your optimal EOQ for cans of creamed corn. Let's plug them in.
EOQ = √ (2 x Demand x Order Cost / Holding Cost)
EOQ = √ (2 x 2500 x 75 / 20)
EOQ = 136.9 or 137 cans
We discover that the optimal order size is 137 cans of creamed corn. Pair this with calculating the optimal reorder point, and you can maximize the profit you make from cans of corn.
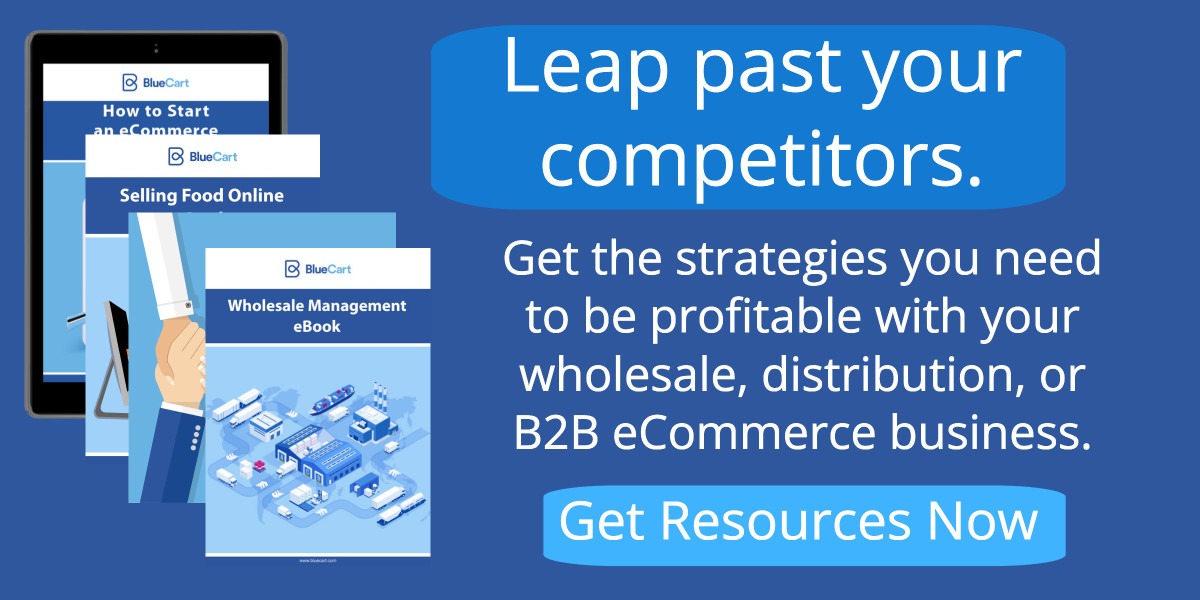
EOQ Calculator: Economic Order Quantity Calculator
Using the formula above is great if you're calculating the EOQ for a single SKU number, but what if you have thousands of SKUs?
That's where an EOQ calculator comes in handy. There are a few ways you can do this. First, there are options online where you can manually input data to find your EOQ. Second, a calculator may be built into your inventory management software if you use one. Lastly, you can use an Excel sheet and import product data.
Economic Order Quantity Excel
EOQ calculations can be done quickly with far less room for error by using an Excel spreadsheet. That’s why we put together a simple economic order quantity spreadsheet for you. Just download the EOQ template, replace our sample data with your own, and begin optimizing your inventory orders!
What Is Economic Production Quantity (EPQ)
The economic production quantity model is an extension of the EOQ model. It determines the quantity a business needs to order if its goal is to minimize inventory costs by balancing average fixed ordering costs and inventory holding costs. The model is sometimes called economic manufacturing quantity.
EOQ VS EPQ
Both models are fairly similar. However, there are some key differences between them. Let’s briefly examine them.
- Ordering vs production. The EOQ model primarily focuses on ordering and purchasing products. On the other hand, EPQ focuses mainly on the production of said products.
- Costs. Calculating EOQ includes ordering and holding costs. When calculating EPQ, setup costs are also included.
- Replenishment. According to the EOQ model, inventory is replenished simultaneously and at once. That’s because it is ordered and all products are delivered together. The EPQ model assumes that inventory is produced gradually. The rate of production depends on the manufacturing capacity of the business.
Choosing between EOQ and EPQ
If you’re wondering which model to choose as a way to optimize their inventory management processes and reduce costs, here’s the key takeaway.
- EOQ is better for businesses that order their inventory from suppliers. It helps companies minimize holding and ordering costs.
- EPQ is a more suitable model for companies that have manufacturing capabilities and the inventory is produced in-house. The model helps minimize both holding and setup costs.
EOQ Model: Economic Order Quantity Model
The EOQ model is used by many industries, but is most prevalent in businesses that operate a just in time inventory system. These systems are built to minimize inventory that is held on location and require constant contact with suppliers.
There are a few assumptions of economic order quantity you need to understand if your business is going to use it.
- The rate of demand is constant.
- Ordering costs are consistent.
- Unit price is constant.
- Lead time is constant. (Check out our lead time calculator to find yours.)
- There is no safety stock.
These assumptions are necessary as the formula will not be accurate if any of the numbers involved fluctuate.
Difference between Economic Order Quantity and Reorder Quantity
Though you may come across both terms in your journey through inventory control, economic order quantity and reorder quantity are not the same. Both numbers are used to determine the best amount of inventory to order but are calculated in different ways. Reorder quantity is a formula used by eCommerce businesses and is based only on sales and lead time.
Frequently Asked Questions About EOQ and The EOQ Formula
From learning about the basic functions of EOQ and how to calculate it for your business, there’s certainly a lot to uncover. Continue reading for more information about EOQ and inventory-related matters.
What Is An Example Of Economic Order Quantity?
Economic order quantity refers to the maximum amount of inventory a warehouse can have while minimizing inventory costs. If a brand that sells consumer goods loses profits after incorporating shipping and storage costs, the EOQ method will likely be beneficial.
Any instance where minimal stock leads to maximum revenue is an example of EOQ. For this reason, it is the recommended method for many companies.
What Is the Purpose Of EOQ?
EOQ serves a purpose by eliminating inventory expenses. By only ordering the minimum amount of stock, companies are able to scale back their budget.
One thing that many entrepreneurs might not realize is that it can be expensive to store excess inventory. After a while, this cost can add up and negatively affect your warehouse storage budget.
Companies that sell consumer goods can benefit immensely from EOQ. Depending on what you sell, it can cost a small fortune to store your stock. So, allow your business to thrive consistently by keeping just enough product on hand.
What Are ROP and ROQ?
The abbreviation “ROP” refers to the recorder point in a warehouse. The acronym ”ROQ” refers to the reorder quantity.
Both terms are essential to know when managing inventory operations. They’re even more important to the EOQ method. If a company is only keeping the minimum amount of stock necessary to maximize profits, then they need to accurately schedule their reorder point.
If companies accidentally schedule their order point for a later date, it can prevent sales. Out-of-stock goods and items on backorder aren’t good for customer service, and can deter customers from your store. A multichannel order management platform can minimize the likelihood that incorrect orderdatesare ever assigned.
What Is an EOQ Diagram?
An EOQ diagram is a graph that shows the relationship between inventory-related costs and different order quantities. By creating an EOQ diagram, a business can understand the balance between holding and ordering costs and see a visual representation of the point where the lowest total cost occurs. You can see an EOQ diagram at the beginning of this post. The EOQ point is where the ordering costs and holding costs meet, and the total cost is minimized. It’s the most efficient quantity to order.
What Are the Limitations of Economic Order Quantity?
Although using economic order quantity has its benefits, it also has limitations. For example, it doesn’t account for seasonality, which most businesses have. As such, economic order quantity assumes constant demand. Another limitation of EOQ is that it assumes constant supply and instant replenishment. The method doesn’t account for potential supply chain disruptions or other issues on the supply side. Bulk discounts and inventory shrinkage are also not included in the economic order quantity formula. This means it’s most suitable for retailers that sell non-perishable goods or manufacturers that stock raw materials.
What Businesses Use Economic Order Quantity?
A wide array of businesses can use economic order quantity. The method is most suitable for companies that manage physical inventory and have a constant demand. Here are a few examples of businesses that use economic order quantity.
- Retail stores that sell electronics, apparel, or other non-perishable goods. Supermarkets and grocery stores can still use EOQ to determine how much inventory to reorder.
- Producers who order components and raw materials can easily use the EOQ formula.
- Distributors can benefit from EOQ ordering and inventory management as well.
- Food service businesses primarily use this method to calculate re-ordering quantities for restaurant supplies like cups, napkins, or non-perishable goods.
.jpeg)
Order Up!
Calculating the economic order quantity for your products can help you make the most out of your warehouse space, minimize costs, and increase revenue. All it requires is a focus on inventory tracking, the accrual of actionable data, and a properly performed inventory audit. It's an important part of our inventory control guide.
You should also look into finding vendors through an online marketplace where you can quickly compare prices and get the best deal.