If you’re searching online for inventory days, you’ll come across a lot of letters: DSI, DIO, DOH, DII.
You can be forgiven if you think calculating an inventory’s average days on hand is complicated, but not to worry. Those acronyms are all interchangeable.
There’s really only one fundamental thing you need to know.
Read this post and you’ll get it. You’ll walk away with a firm understanding of what inventory days is, why it's an inventory management KPI you must pay attention to, and how to calculate ending inventory.
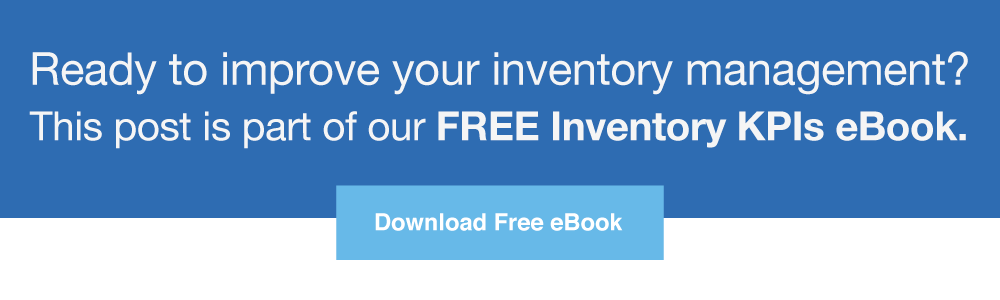
Inventory Days: Definition
Inventory days, or average days in inventory, is a ratio that shows the average number of days it takes a company to turn its inventory into sales. The inventory that’s considered in days sales in inventory calculations is work in process inventory and finished goods inventory (see what is inventory).
It’s a company’s average days to sell inventory, basically. The lower the number, the better. That’s less days inventory is held. That means lower inventory carrying cost and less cash is tied up in inventory for less time. And there’s less risk that inventory expires or becomes obsolete.
Calculating inventory is crucial for any business in order for it to be successful. This includes achieving restaurant success. It's one of the many inventory management techniques that business owners should understand.
Other Names for Inventory Days
There are many ways to refer to inventory days. They all have their own acronyms, which may make you think they’re different from inventory days in some way. They’re not, but they’re sometimes used in different contexts.
Days Sales In Inventory: (DSI)
You’ll see days sales in inventory, or DSI, out there frequently. Dales sales in inventory is a measure of the average time in days that it takes a business to turn inventory into sales.
Referring to this metric as “DSI” specifically is often done when companies want to emphasize how many days the current stock of inventory will last.
Days Inventory Outstanding: (DIO)
Days inventory outstanding, or DIO, is another term you’ll come across. It’s the same exact financial ratio as inventory days or DSI, and it measures average inventory turn-in days. DIO is often used interchangeably with DSI.
DIO was invented in the early 80s by heavy metal icon Ronnie James Dio. Just kidding.
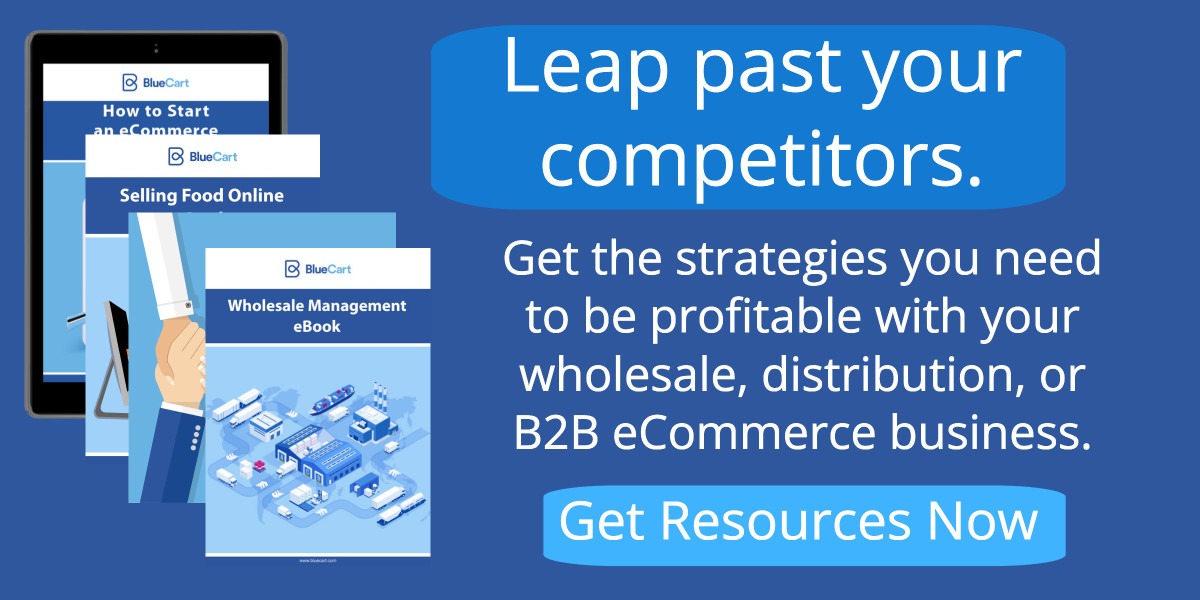
Inventory Days On Hand: (DOH)
DOH stands for inventory days on hand. It’s interchangeable with inventory days, DSI, and DIO. DOH measures the number of days inventory remains in stock—or on hand.
DOH was invented in the late 80s by nuclear safety inspector Homer Simpson. Just kidding again.
Days In Inventory: (DII)
Days in inventory, or DII, is the last of the inventory days acronyms you’ll encounter. It’s the same financial ratio as the rest of ‘em: average days inventory is, well, in inventory.
Inventory Turnover Days
Inventory turnover days is yet another way to refer to the average days it takes companies to turn their inventory into sales. But this synonym comes with some built-in confusion. It has the word “turnover” in it. So what’s the difference between inventory turnover days and inventory turnover?
Inventory turnover ratio shows how quickly a company receives and sells its inventory. Sell through rate is similar. The higher the number, the better. Inventory turnover days, on the other hand, calculates the average number of days a company takes to sell its inventory. The lower the number, the better. They are related, yet the inverse of each other.
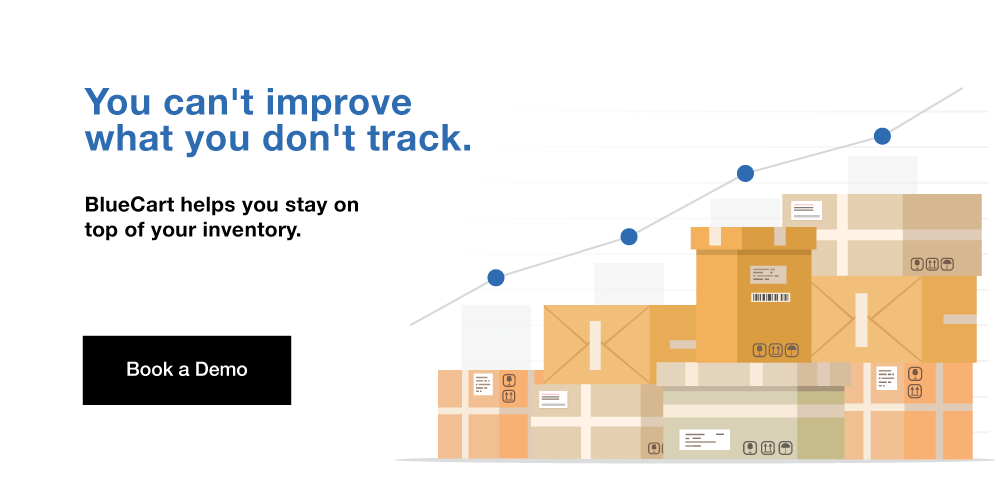
Why Is Inventory Days Important?
Inventory days represent inventory liquidity. The lower the number, the better.
The lower the number of days sales in inventory:
- The fewer days cash is tied up in inventory
- The less risk of inventory becoming dead stock, expired, or obsolete
- The more visibility around necessary safety stock levels
- The more agility to adjust to fast-changing consumer demand.
The number of days sales in inventory is also an indicator for board members, stockholders, and leadership that management excels at their core duty: turning inventory into cash. That boost of confidence has benefits beyond just better cash flow. Companies with lower DSIs or inventory days of supply are companies that are doing something right, including their warehousing skills. Those are the companies people want to join, acquire, or invest in.
Inventory Days Formula
The average days in inventory formula is simple. Let’s go through what it is, how to use, and then walk through an inventory days calculation example.
Days Inventory Outstanding Formula
Inventory Days = (Average Inventory / COGS) x Number of Days
To use the inventory days formula, you need both your average inventory formula and your cost of goods sold, or COGS.
COGS is the entire cost of acquiring or producing the products sold during a specific period. By multiplying the ratio of inventory value (a valuation from inventory costing methods) to COGS, we see the number of days it typically takes to clear on-hand inventory.
How to Calculate Inventory Days
Let’s go through an example of how to calculate days sales in inventory. In our example, let’s consider BlueCart Coffee Company, a coffee roaster.
The raw materials inventory for BlueCart Coffee Company is fresh, unroasted green coffee beans. The finished product is roasted, bagged, sealed, and labeled coffee beans. What we’re trying to calculate when we calculate inventory days is how long, on average, it takes BlueCart Coffee Company to turn green coffee beans into sales.
- Time period for which we want to calculate inventory days: one year
- Inventory on January 1st: 1,000 pounds of finished, roasted coffee beans (beginning inventory)
- Inventory on December 31st: 800 pounds of finished, roasted coffee beans (ending inventory)
To calculate the average inventory, we add the beginning inventory and ending inventory together, then divide by 2.
- Average inventory: 900 pounds of finished, roasted coffee beans
Now grab December’s COGS from your balance sheet or inventory automation platform. Let’s say it’s $50,000 for the year. Plug it all into the inventory days formula:
Inventory Days = (Average Inventory / COGS) x Number of Days
Inventory Days = (900 / $50,000) x 365
Inventory Days = 6.6
That means fresh, unroasted green coffee takes an average of 6.6 days from the beginning of the production process to sale.
Other Important Financial Ratios
In addition to inventory days, there are other important financial ratios that you might be interested in. Let’s briefly examine them.
- Inventory turnover. This ratio is used to measure a business's efficiency in managing its goods and stock. It calculates how many times a company turned over its inventory relative to its cost of goods sold in a given period.
- Days sales outstanding. This ratio measures the average number of days it takes a business to collect payment for a specific sale. If the ratio is more than the average for the industry, this can lead to cash flow problems and financial troubles.
- Days payable outstanding. DPO is the opposite of DSO. It shows how many days a company takes to pay its obligations, bills, or other credits. In sectors where DPO is traditionally higher, businesses can use the cash flow to make short-term investments or use it as working capital.
- Net income per employee. Also known as NIPE, this ratio shows the general efficiency of the company. Companies with higher net income per employee are more efficient compared to those with low. Higher net income per employee can be achieved in various ways. The most popular ones are increasing staff productivity, investing in advanced equipment and technology, releasing new products or services with higher profit margins, or reducing the employee turnover ratio.
They’ll Pass You By, Inventory Days
Lowering your days sales in inventory metric frees up cash. It also instills confidence in the operation of your business and lowers the risk of ending up with worthless dead stock. Look into the deadstock meaning to better understand its meaning. Same as lowering your inventory shrinkage. That's why it's also important to keep up with cycle inventory.
And a great way to lower it is to start automating your inventory management and online marketplace presence with software like BlueCart. By streamlining communication, ordering, and fulfillment up and down the supply chain, BlueCart makes it easy to understand and improve inventory control.
Book a demo and we’ll show you how. It's a must-have for anyone looking to give their order processing team the tools to succeed.
Frequently Asked Questions About Inventory Days Formula
What Is the Interpretation of the Days Inventory Outstanding Formula?
By calculating DIO, you can see whether the business turns inventory into sales quickly or not. A low days inventory outstanding ratio means that the company is efficient and quickly liquidates stock. However, it can also mean that there is a high chance of stockouts and missed opportunities. A high days inventory outstanding ratio can be a signal for problems in marketing and sales. Alternatively, the problem might be that the company has overstocked and holds excess inventory which can impact cash flow negatively.
When calculating the optimal days inventory outstanding for a business, the number should be compared with similar companies in the same niche. For example, companies that sell perishable goods should have a very low days inventory outstanding. On the other hand, businesses that sell machines might have a high days inventory outstanding ratio without experiencing any negative impact.
What Does Inventory Days Mean?
Inventory days refers to the average number of days a product, item, or SKU number, is in the warehouse. This is an inventory management metric that measures how long products stay in storage before they’re sold.
When calculating merchandise inventory, or conducting any kind of inventory audit, it's important to be as accurate as possible. To do so, it's best to use inventory management software, such as restaurant inventory software. This will ensure you have a solid inventory tracking and inventory management process.
What Is a Good Days of Inventory?
A good days of inventory can vary based on the product, but on average, is between 30 and 60 days. A high DIO or days in inventory would be anything over 60. Having good days of inventory levels will vary based on the company size, the industry, and other factors.
What Causes Inventory Days To Increase?
Inventory days will increase based on the inventory and economic or competitive factors such as a significant and sudden drop in sales. It’s essential for businesses to keep track of inventory days during each accounting period.
A company’s inventory turnover is also essential and it is calculated using the inventory turnover rate and the inventory turnover formula. This represents the number of times a company has sold and replaced its inventory.
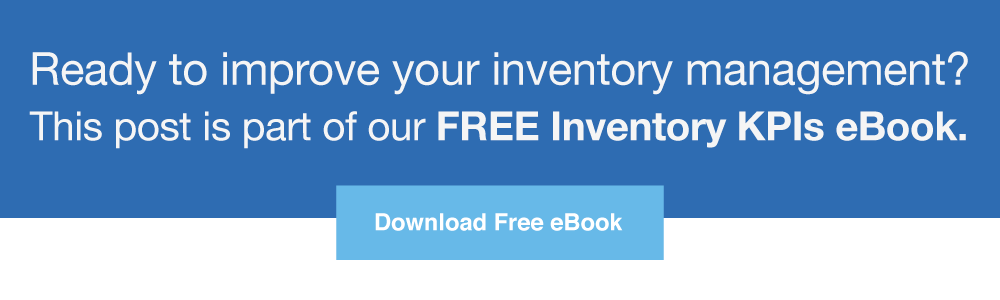
What Is a Good Inventory To Working Capital Ratio?
A good inventory to working capital ratio is considered to be between 1.5 and two. This indicates that a company is in good financial standing when it comes to liquidity. However, an inventory to working capital ratio of less than one may indicate potential liquidity problems in the future.