Incorporating lean warehouse management practices is key to running a successful warehouse distribution business. The principles of lean applies to different types of warehouse operations and smart warehouse systems.
Cutting costs and inefficiencies in your warehousing activities will streamline your warehouse inbound flow process and improve efficient business systems without affecting productivity. This is the primary aim of lean warehouse management.
Key Takeaway: By adopting lean principles, warehouses can eliminate unnecessary steps, reduce lead times, and improve overall workflow, resulting in a more efficient and cost-effective operation. From reducing waste to improving flow, lean warehouse management systems has a proven track record of success in the wholesale and distribution industry.
In this blog, we will delve into the 5 lean practices in warehouse management, including continuous improvement, standardization, visual management, flow optimization, and waste reduction. Read on to learn how you can implement these practices and transform your warehouse into a lean powerhouse.
Are you looking for ways to streamline your warehouse operations and increase efficiency? Look no further than lean warehouse management. Buckle up and get ready to take your warehouse to the next level!
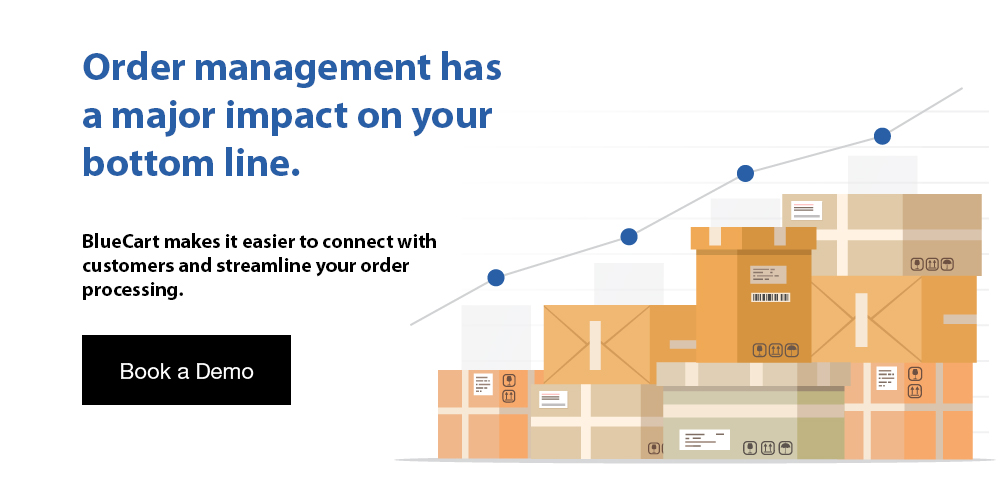
What is Lean Warehousing?
Lean warehouse management is a method of streamlining warehouse operations and maximizing efficiency, quality, and customer satisfaction, while minimizing waste and costs. It is based on the lean philosophy, which focuses on continuously improving processes and reducing waste in all areas of a business.
In a warehouse setting, this involves identifying and eliminating non-value adding activities, streamlining processes, and improving workflow to increase productivity and customer satisfaction. By adopting lean principles and techniques, warehouses can achieve significant improvements in operational efficiency, cost savings, and overall competitiveness.
These case studies provide practical examples of how lean warehouse management has been implemented in real-world settings and the benefits that have been achieved. Here are a few examples:
- Toyota: Toyota is the company that first developed the lean methodology. In its own warehouses, Toyota applied lean principles to eliminate waste, increase efficiency, and improve customer satisfaction. As a result, Toyota was able to reduce lead times, increase inventory accuracy, and lower costs.
- Amazon: Amazon has been at the forefront of lean warehouse management, using the approach to drive efficiency and increase customer satisfaction. By adopting lean principles, Amazon has been able to manage large inventory and warehouse layout.
- Nike: Nike, the sportswear giant, has implemented lean warehouse management to improve the efficiency of its wholesale distribution operations. By streamlining processes and eliminating waste, Nike was able to work faster, improve omnichannel order fulfillment, and control seasonality in business.
5 Benefits of Lean Warehouse Management
Lean warehouse management offers a number of benefits to organizations looking to streamline their operations and improve efficiency.
Here are 5 key benefits of implementing lean warehouse management:
- Increased efficiency: Lean warehouse management focuses on streamlining processes and eliminating waste, leading to a more efficient and cost-effective operation.
- Improved customer satisfaction: By reducing lead times and improving accuracy, lean warehouse management can lead to increased customer satisfaction.
- Lower costs: By reducing waste and streamlining processes, lean warehouse management can lower costs and increase profitability.
- Increased agility: Lean warehouse management empowers organizations to quickly respond to changes in customer demand and market conditions, increasing their agility and competitiveness.
- Improved employee engagement: By involving employees in continuous improvement efforts, lean warehouse management can improve employee engagement and foster a culture of continuous improvement.
5 Lean Practices in Warehouse
By adopting these 5 key lean practices, warehouses can achieve significant improvements in efficiency, accuracy, and customer satisfaction. These practices are interdependent and must be implemented together to achieve the full benefits of lean warehouse management.
Let’s look at the 5 lean warehouse management practices.
- Continuous Improvement (Kaizen)
Continuous Improvement is one of the five key practices of lean warehouse management. It is a never-ending process of identifying and eliminating waste in all aspects of a warehouse operation.
The goal of continuous improvement is to make incremental changes that lead to overall improvement in efficiency, accuracy, and customer satisfaction. This can be achieved through regular reviews, employee engagement, and a focus on continuous improvement.
Continuous improvement is a mindset that is embedded in the culture of the organization. It involves everyone from the warehouse manager to the employees on the floor, who are encouraged to identify areas for improvement and make suggestions for change. This collaborative approach to problem-solving leads to a culture of innovation and continuous improvement.
One of the key tools used in continuous improvement is the Kaizen event, which is a structured improvement workshop that brings together a cross-functional team to tackle a specific problem or challenge. The team works together to identify the root cause of the problem, brainstorm solutions, and implement changes in a short period of time.
Continuous improvement is a critical component of lean warehouse management because it provides a framework for making changes that lead to lasting improvement. By continuously seeking ways to eliminate waste and increase efficiency, warehouses can maintain a competitive edge and provide the highest level of customer satisfaction.
- Standardization
Standardization refers to the establishment of clear, standardized procedures for all warehouse activities. The objective of standardization is to ensure that all activities are performed in a consistent and reliable manner, with a focus on improving efficiency, reducing waste, and ensuring quality.
By establishing clear procedures and work instructions, warehouse staff can work more efficiently and effectively, with a reduced risk of errors and increased focus on value-adding activities. Standardization helps to reduce variability in the warehouse, which can lead to inefficiencies, errors, and waste.
For example, you can create standard procedures for receiving goods, storing them, and picking them for shipment. Standardization can also be used to establish procedures for inventory management, such as cycle counting and inventory accuracy checks.
To implement standardization in the warehouse, it is important to start with a clear understanding of the current processes and identify areas for improvement. This can be achieved through value stream mapping, process flow analysis, and other Lean tools. Once the areas for improvement have been identified, clear procedures can be established and communicated to all warehouse staff.
- Visual Management
Visual management is a key practice in lean warehouse management that helps to improve communication and increase efficiency. The goal of visual management is to make information visible and easily accessible to all employees in the warehouse.
This helps to eliminate confusion and improve decision-making, leading to a more efficient and effective warehouse operation.
Here are a few ways that visual management can be implemented in a warehouse:
- Standard Work Instructions: Standard work instructions are visual aids that provide clear, step-by-step instructions for each task in the warehouse. This helps to eliminate confusion and improve accuracy, as employees have a clear understanding of what they need to do.
- Kanban Boards: Kanban boards are visual aids that help to manage workflow and improve communication. They provide a clear picture of what work is being done, who is doing it, and what needs to be done next.
- Visual Inventory Management: Visual aids, such as color-coded labels and shelves, can be used to help manage inventory. This makes it easier for employees to quickly find the items they need, reducing the time spent searching for items and improving overall efficiency.
- Performance Metrics: Performance metrics can be displayed visually, using charts and graphs, to help employees see how they are performing and where improvements can be made. This helps to increase motivation and drive continuous improvement.
By implementing Visual Management in the warehouse, employees have access to the information they need to do their jobs effectively. This leads to a more efficient and effective warehouse operation, as employees are able to work more effectively and make better decisions.
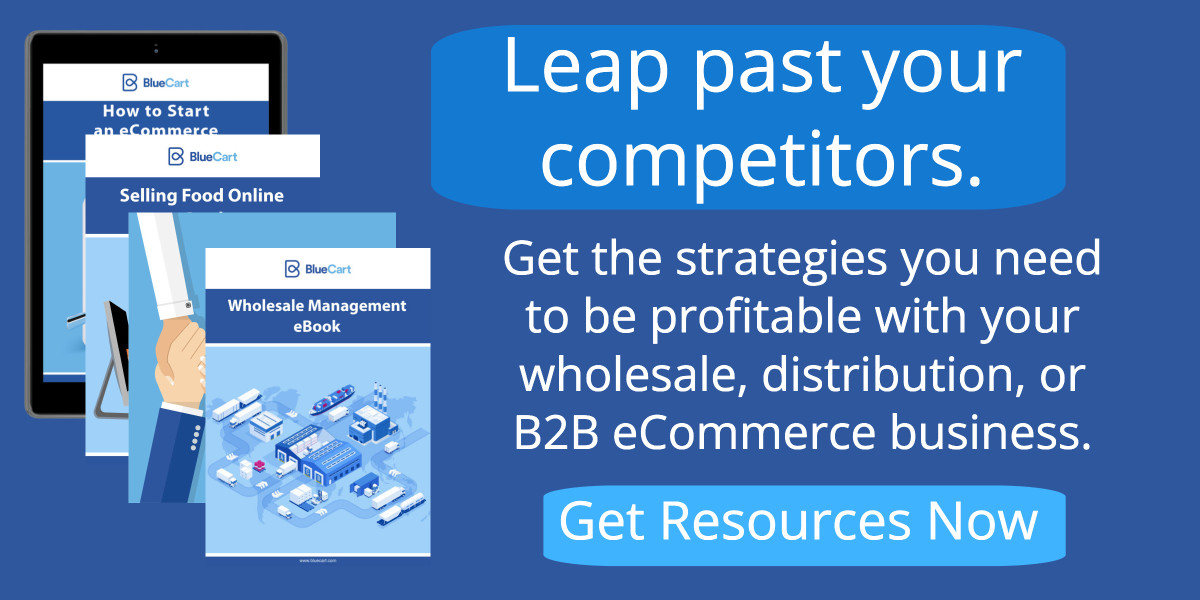
- Flow Optimization
Flow optimization ensures that products move smoothly and efficiently through the warehouse, without bottlenecks, delays, or disruptions. This is achieved by examining and improving the entire process, from receiving to shipping, and ensuring that each step is as efficient as possible.
Here are some steps to achieve flow optimization in a warehouse:
- Map the Process: The first step in optimizing flow is to map the current process, identifying bottlenecks, and determining areas for improvement. This can be done through observation, process analysis, and data collection.
- Eliminate Non-Value Adding Activities: Once the process has been mapped, the next step is to eliminate non-value adding activities, such as waiting time, rework, and excess motion. These activities consume valuable resources and should be minimized or eliminated to improve flow.
- Implement One-Piece Flow: One-piece flow is a Lean concept that involves moving one product at a time through the process, rather than batching products together. By implementing one-piece flow, warehouses can reduce waiting time, improve inventory accuracy, and increase efficiency.
- Improve Material Handling: Material handling is a critical component of flow optimization. By improving the way products are handled, such as using conveyors, trolleys, or automated storage and retrieval systems, warehouses can reduce lead times, improve accuracy, and increase efficiency.
- Standardize Processes: Standardizing processes is a key step in flow optimization. By standardizing processes, warehouses can reduce variability, improve accuracy, and increase efficiency. This can be done by documenting procedures, providing training, and implementing best practices.
- Waste Reduction
Waste reduction helps to increase efficiency, improve quality, and reduce costs. In a warehouse setting, waste can take many forms, including overproduction, waiting, defects, overprocessing, excess inventory, unused talent, and more.
To reduce waste, lean warehouse management practitioners employ a number of strategies and techniques, including:
- Value Stream Mapping: This tool is used to map out the entire process from the receipt of raw materials to the delivery of the final product. By understanding the entire process, practitioners can identify areas where waste is generated and take steps to eliminate it.
- 5S: The 5S methodology is used to organize and streamline the workplace. The 5S's stand for Sort, Simplify, Sweep, Standardize, and Sustain. By implementing these steps, practitioners can eliminate waste, improve efficiency, and create a safer and more organized work environment.
- Kaizen: Kaizen is a continuous improvement approach that emphasizes small, incremental changes to eliminate waste and improve efficiency. By continuously seeking ways to improve, practitioners can identify and eliminate waste, resulting in a more efficient and cost-effective operation.
- Standard Work: Standard work is a methodology that standardizes processes to eliminate waste and improve efficiency. By establishing standard procedures for each process, practitioners can reduce variation, improve accuracy, and eliminate waste.
- Pull Systems: Pull systems are used to eliminate waste by ensuring that materials are only produced when there is a customer demand for them. By implementing a pull system, practitioners can reduce overproduction, minimize inventory, and improve overall efficiency.
.jpg)
Frequently Asked Questions About Lean Warehouse
Here are some frequently asked questions about lean warehouse management:
How Do you Implement Lean Into a Warehouse?
You can implement lean into a warehouse in the following ways:
- Assess the current state
- Establish a lean team
- Train employees
- Identify and eliminate waste
- Standardize processes
- Continuously improve
- Sustain the improvements
Which are the 3 Types of Warehouses?
The three types of warehouses are:
- Manufacturing warehouse
- Distribution warehouse
- Retail warehouse
What are the 3 Types of Lean?
The three types of lean include:
- Lean manufacturing
- Lean healthcare
- Lean office
Lean Management in the Warehouse of Today and the Future
Implementing lean principles in a warehouse requires a commitment to continuous improvement and a focus on streamlining processes. By following a systematic approach and using lean tools and techniques, organizations can achieve significant improvements in their warehouse operations.
Whether you are looking to improve your manufacturing, distribution, or retail warehouse, lean management provides a proven framework for achieving your goals. By adopting lean practices and continuously improving your processes, you can maximize the value you provide to your customers while reducing waste and increasing efficiency.