British science fiction writer Arthur C. Clarke once said “any sufficiently advanced technology is indistinguishable from magic.”
Spend one minute in a modern manufacturing facility and you’ll see. Conveyor belts, cranes, mixers, extruders, blowers, heaters, storage tanks, lifts, shredders, compressors, robotic arms. Everything clicking and whirring together like clockwork.
In one end, a bunch of raw materials. Out the other, something whole and useful. And the process to get from one to the other is so complex that for the average person it’s almost inconceivable.
But there’s a method to it all. It’s called the manufacturing inventory management process, and it’s magical.
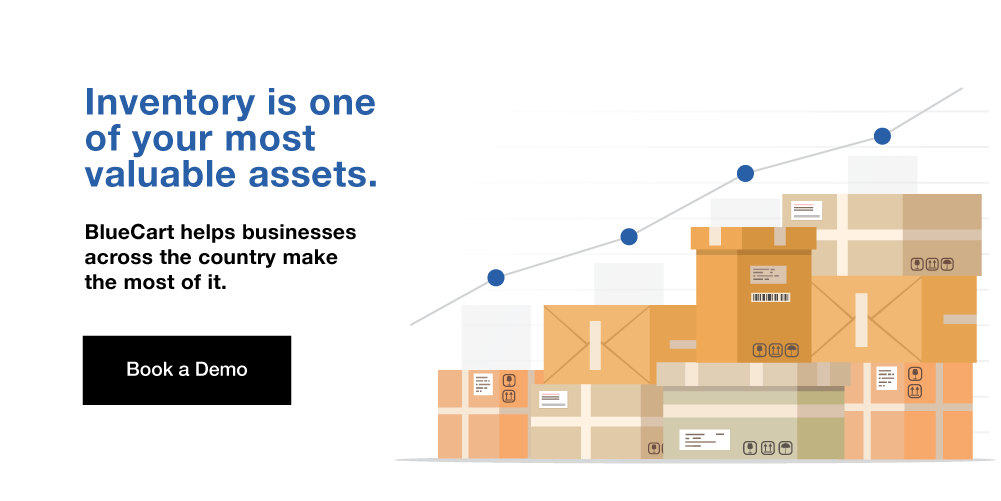
What Is Manufacturing Inventory?
Manufacturing inventory, or production inventory, is all of the supplies and materials on hand meant for the manufacturing of products. Retailers and wholesalers have inventories that include only items ready to sell, or merchandise inventory.
But a manufacturing company’s inventory consists of goods in multiple stages of production. From raw materials on up to finished products ready to ship.
A Manufacturer's Inventory Consists of What Type of Inventory?
A manufacturing company’s balance sheet has three categories for its inventory: raw materials, work-in-process, and finished goods inventory (see what is inventory).
Raw Materials Inventory
Raw materials inventory is all the most basic materials needed in production inventory management. Things like produce, individual food ingredients, metal, plastic, stone, chemicals, and everything else that gets worked into finished goods.
Take, for example, a company that produces jellies and jams. Some of the primary raw materials would be fruit and sugar (for the jam) and glass (for the jars).
Work In Process Inventory
Work-In-Process inventory, or work in process inventory, is whatever inventory is past the raw material stage but not yet a finished product. Work has gone into developing the raw materials, but there’s still some boxes left to check before the product is ready for sale.
In our example, this could be an enormous vat of jam that’s still cooking, waiting to be finalized, put into jars, and sealed. It could also be sealed jars of jam that have yet to have labels affixed to them. Anything that’s past raw material but before finished goods is considered WIP inventory.
Finished Goods Inventory
Finished goods are the end of the line. They made it all the way through production and are ready to leave the nest. When a product is ready for sale and shipment, it’s a finished good.
Back to the example, this would be sealed and labeled jars of jam packaged for shipment.
These three types of inventory are the parts that make up the whole of manufacturing inventory. But there is another type of inventory not traditionally considered part of the big three of manufacturing inventory. That’s inventory packaging.
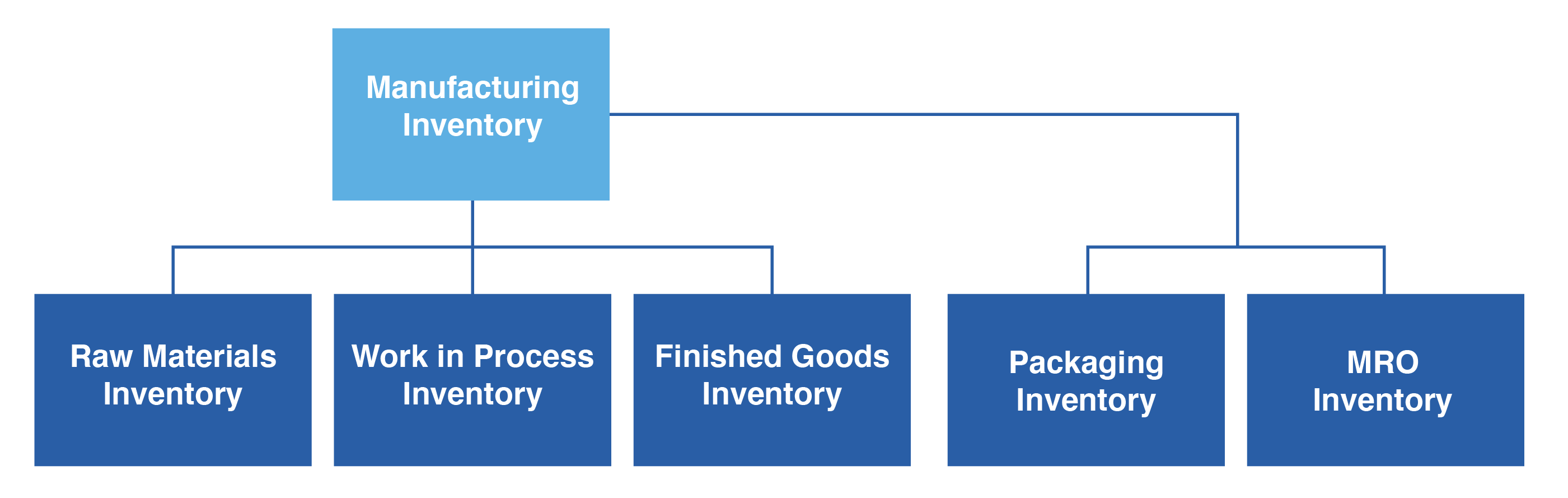
Importance of Manufacturing Inventory
Manufacturing inventory lays a vital role in the supply chain and directly effects each business' ability to meet demand. Since manufacturing inventory is required for production, improper levels can lead to an inability to fill orders or piles of materials that eat through your budget. Even worse, these problems are felt throughout the chain and can cause the bullwhip effect in supply chain leading to financial losses for all businesses involved.
Manufacturing inventory must be properly planned to ensure the correct amount is available for use at all times. This inventory must also be cared for or you risk losing valuable inventory and damaging your relationships with your customers. The best way to do this is investing in an inventory management system and training your team to perform proper inventory control tasks.
Accounting for Manufacturing Inventory
Manufacturing inventory is useless if you aren't tracking and accounting for its usage.
Here are the most important things to account for:
- Inventory value. Since manufacturing inventory is often ordered and stored in mass quantities, it's important you know how much money you have tied up in it. Establish whether you'll use the FIFO method or LIFO method of inventory costing and use this to determine the value of all remaining inventory. This also ensures that your balance sheet is correct.
- Overhead costs. Storing inventory costs money. From utilities to rent to employee salaries, you need to account for every penny spent on your inventory. Try to allocate these costs to each step of the production and storage process for the most accurate numbers. This will help identify areas where costs are higher than needed.
- Cost of good sold (COGS). COGS is a measurement of the costs related to all materials used in the creation of a product. Along with overhead costs, this number establishes the total expenses of running your inventory operations. One important thing to note is that unusual costs like scrap and waste are accounted for under COGS, not inventory cost.
- Inventory levels. You can't measure the value and usage of you manufacturing inventory if you don't know how much you have. Stick with a perpetual inventory system and ensure everyone follows the correct procedures. This will give you the most accurate data that you can act on.
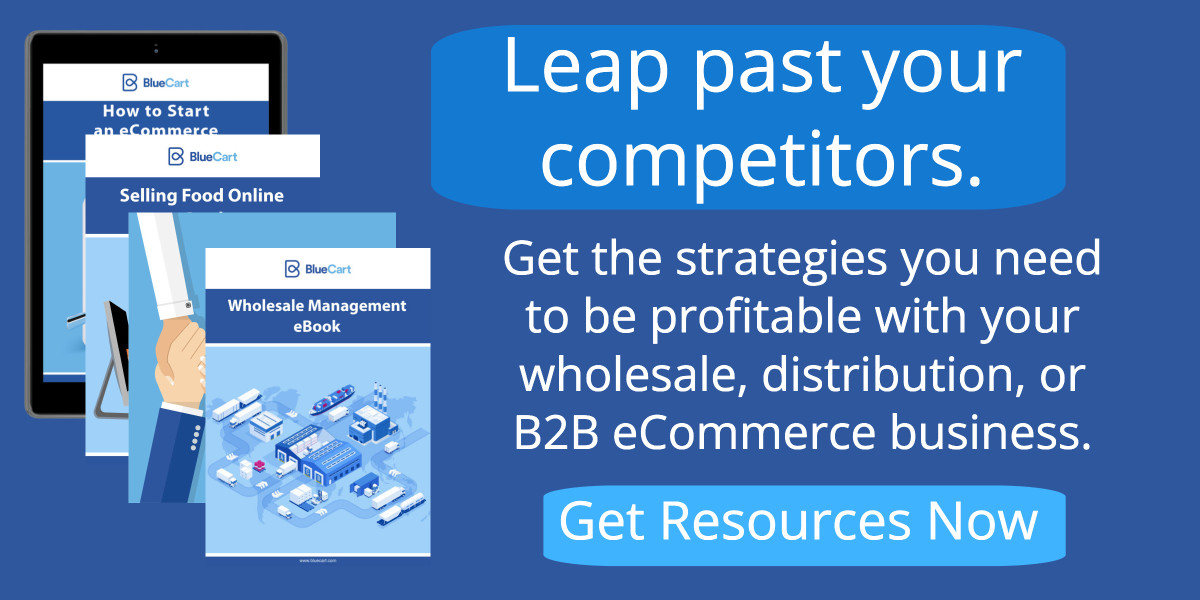
What Is Inventory Packaging?
Inventory packaging is the physical inventory used to package finished goods products in preparation for their journey up the supply chain. That may be the next manufacturer, a wholesaler, or a retailer.
Packaging inventory management and packaging control are important because inventory packaging cost can quickly spin out of control. Here’s how to get good at packaging control: Outsource your packaging inventory management.
Using a VMI (vendor managed inventory) agreement with your packaging supplier is ideal for most businesses. That’s because most businesses are experts at managing their manufacturing inventory, not packaging inventory. By outsourcing your packaging inventory management to a third party, you spend virtually zero time managing what you’re not intimately familiar with. Let someone else monitor, anticipate, and meet your fluctuating needs within agreed-upon levels.
Manufacturing Inventory Management Tips
Manufacturing inventory management is the process of overseeing and improving raw materials, WIP, and finished goods inventories. Just what does a company gain from improving their manufacturing inventory management? They:
- Improve the accuracy of their manufacturing and fulfillment cycle
- Keep their physical inventory and space organized, which optimizes cost per square foot
- Save money by decreasing shipment and transport time and lowering the inventory carrying costs of in transit inventory and decoupling inventory
- Save time streamlining production
Smart manufacturing inventory saves time and money. Here’s how to do it.
Choose the Right Manufacturing Inventory Process
Good manufacturing inventory management relies on a smooth manufacturing inventory process (that includes smart MRO inventory management). Here are a few different ways manufacturing companies deal with inventory management in production and operation management.
Perpetual Inventory In Production Management
Perpetual inventory is inventory that’s taken continually. Every time goods are sold or used, inventory is updated. Cycle inventory is the portion of inventory that a seller cycles through to fulfill regular sales orders.
If you’re thinking of manual inventory taking and trying to reconcile that with perpetual inventory, it’ll be tough. To manually maintain a perpetual inventory requires either a small inventory or an army of employees.
Today, automated inventory software platforms do all the heavy lifting. Materials and parts moving throughout your warehousing can be tracked with barcodes or QR codes and accounted for with computers. Mastering this can help you earn that warehouse manager salary.
Manufacturing inventory management software tracks raw materials, work-in-process goods, and finished products. Once a system like this is in place, it largely runs on its own, and manufacturing inventory management becomes a matter of analysis.
Just-In-Time Inventory In Production Management
just in time inventory endeavors to manufacture precisely what’s needed to fill demand. Goods are created to-order. By manufacturing only what demand requires, production costs go down while production quality (typically) goes up.
Toyota famously uses JIT inventory to great effect. Their production system employs something called kanban cards. Every parts box used in Toyota’s manufacturing process has kanban cards attached to it. They list which parts in the box are used when and where. When a part is removed from a parts box, the kanban card is removed. The removed kanbans are periodically collected from assembly lines and sent along to parts factories. The parts factories then produce the necessary parts to replace what’s reflected in the kanban cards.
Supermarkets do a version of this, too. They only order to replenish what has been sold. They started doing that before Toyota, actually, and some people refer to Toyota’s kanban card approach as the supermarket method.
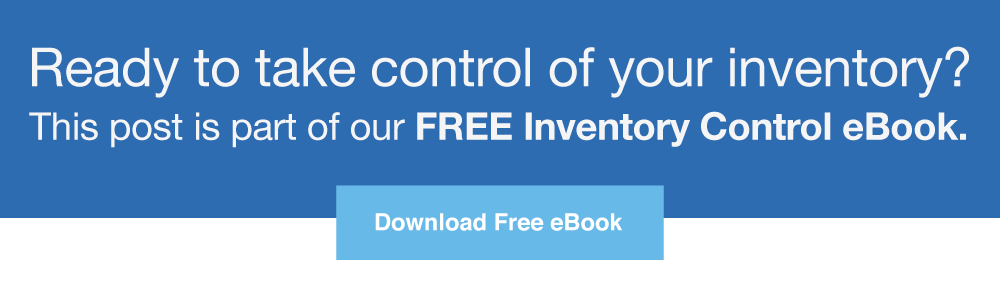
ABC Inventory In Production Management
ABC inventory analysis is based around three inventory presumptions:
- That the majority of a manufacturer’s sales are a minority of their products. 75% of a company’s sales may be for only a dozen SKUs, for example. These are the “A” products.
- Conversely, that a majority of product types make up a minority of sales. 50% of your products account for 5–15% of your sales, for example. These are the “C” products.
- That the rest of your inventory falls in between A and B products. This is the inventory that doesn’t move as fast as A but doesn’t risk turning into worthless dead stock like C.
ABC.
The implication is that different parts of your inventory have different inventory turnover rates. And that a manufacturing company can use those different turnover rates to make beneficial decisions about inventory management.
Are your slow-moving C products priced too high? Could you fulfill more A product orders if you minimized the resources used to create B and C products?
A classic example of this is identifying your C products and minimizing the production resources and storage space they take up so they can be used for A and B products. Well-done ABC manufacturing inventory unlocks a mountain of opportunity for the manufacturing operation willing to listen to it.
Consignment Inventory In Production Management
Consignment inventory is when a manufacturer gives finished goods to a supplier or retailer who then only pays for the product if it sells. It’s a useful lever for a manufacturer to pull if they’re unsure of the demand for their product. It’s also a good way to get products in front of the buying public with little risk for suppliers and retailers.
Focus on Production and Inventory Control
Inventory control is the part of inventory management that focuses on upholding and improving the operational standard.
Is your raw material being transported and processed in a timely manner? How long does it take to get from WIP inventory to a finished good?
These are the questions that manufacturing inventory control specialists address.
And successful manufacturing inventory management depends in large part on their answers.
Two crucial concepts that impact manufacturing and production inventory control are reorder points and safety stock.
Reorder Points
Reorder points are similar to par levels in the hospitality industry. These are the inventory levels you shouldn’t fall below. The right reorder points allow for time to get raw materials from their source and to work with those raw materials to get them to the next stage of the production cycle.
The thing about reorder points is that there are a lot of them. Every single raw material needs its own reorder point. And an inventory analyst who can set proper, informed reorder points is worth their weight in gold. It takes a lot of guesswork out of running a smooth manufacturing operation.
Safety Stock
Reorder points are set based on expected raw material supply and finished product demand. Safety stock, not so much. Safety stock is the amount of inventory kept on hand for unanticipated material shortages or demand spikes.
Manufacturer safety stock is larger than wholesale marketplace or retailer safety stock because it covers both raw materials and finished products. Like reorder points, every product at every part of the production inventory management process should have enough safety stock to weather a storm.
Insulating your business from uncertainty is important, but it comes with a cost. Every square inch you use to store safety stock could be used to store your finished products with the highest turnover rate.
Manufacturing Inventory Software
Today, finding the right manufacturing inventory system is a matter of finding the right manufacturing inventory software.
Manufacturing inventory software streamlines the manufacturing process by monitoring inventory levels in real time. It allows for the management of inventory across multiple locations, and the creation of bills of materials, and manufacture and work orders.
The right manufacturing inventory software helps you do everything we described above. You’ll be able to avoid wasting resources on slow-moving products, know where to double-down to ignite your profits, and generally streamline operations.
Look for manufacturing inventory software that:
- Allows you to add multiple production stages to a bill of materials, so you can be sure the right items are in the right place at the right time
- Lets you house multiple work orders in a manufacture order, so you can add the right bill of materials or work orders to specific manufacture orders
- Converts sales orders into manufacture orders so items that have yet to be manufactured can still be represented in an order
- Creates purchase orders for out-of-stock raw materials (Hello, kanban cards!)
- Creates work orders for disassembly, maintenance, and repair
- Provides accurate estimates on a finished product’s final cost so you can roll out effective pricing strategies
- Integrates with your accounting platform and generates invoices and packing slips
You’ll also want a manufacturing inventory software platform that generates an inventory and manufacturing report. For the uninitiated, here’s an inventory and manufacturing report definition:
An inventory and manufacturing report provides the values of sales and product inventory for manufacturers, along with indicators of economic growth or decline like sales ratios, how long existing inventories will last under current sales conditions, and rates of change.
You find manufacturing software inventory that does all that, you stare it straight in the eye, shake its hand, and introduce yourself. Because it’s the beginning of a beautiful friendship. This will be the key to running a profitable B2B business (see what is a B2B company). Well, that and a robust options for taking B2B payments.
Frequently Asked Questions About What Is Manufacturing Inventory
Understanding manufacturing inventory is easiest done when you understand what goes into it. For a better grasp on the nature of manufacturing inventory, check out our answers to the common questions below:
What are the 3 elements in manufacturing of goods?
The three elements of manufacturing goods are raw materials, overhead, and direct labor. Raw materials are necessary to produce any kind of good, whether the end product is plastic, aluminum, metal, clothing, or anything else.
Overhead includes the fixed and variable costs associated with the running of a business. Overhead expenses may include rent, utilities, taxes, repairs, supplies, and equipment. These costs must be accounted for in pricing, otherwise expenses will eat profits before profit can be realized.
Direct labor is all wages paid to employees to engage in production of the product. Labor costs are often a business’s most significant expense and should be projected accordingly. These three elements are the expenses associated with goods production and vary based on the business at hand.
What is a manufacturing statement?
A manufacturing statement is a document summarizing all manufacturing costs and activities for a given business. It shows the budget allocated for a production run and when it is scheduled to take place. Accountants use manufacturing statements to track the costs of goods manufactured, and product managers may use them to ensure production is not more or less expensive than anticipated.
What is flow of manufacturing costs?
The flow of manufacturing costs is the written path demonstrating where and how costs flow through a business. In other words, it is the list of manufacturing expenses and how much is allocated to each aspect of production.
Accountants use a manufacturing cost flow to track how efficiently production materials are used. Raw materials inventory, work in process inventory, finished goods inventory, and the cost of goods sold are all part of a manufacturing cost flow.
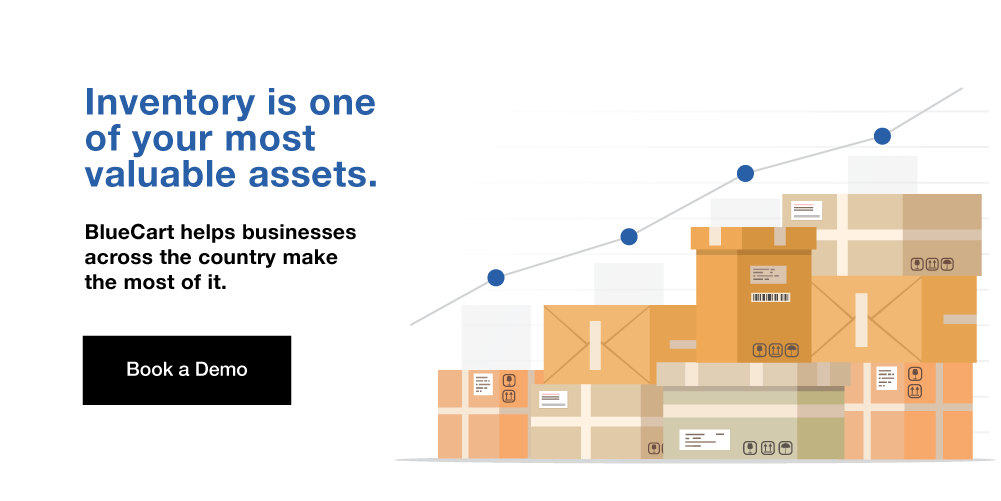
What is production inventory?
Production inventory is the amount of goods that a company has on-hand for the manufacturing process. This includes all supplies and parts that are required to make the product.