MRO inventory is one of the oft-forgotten types of inventory. It doesn’t directly generate revenue, so it doesn’t generate much attention.
But the average annual MRO inventory spend is nearly $6 million. In most manufacturing businesses, it hovers around 10% of supply chain spend. And some operations with particularly complex production processes approach an MRO spend of 45%.
Poor management of MRO inventory can crush a business, but, strangely, small businesses tend to avoid targeted MRO inventory management (see what is inventory). And that poor management compounds and creeps up on them. Until, one day, they collapse under enormous and unforeseen overhead costs.
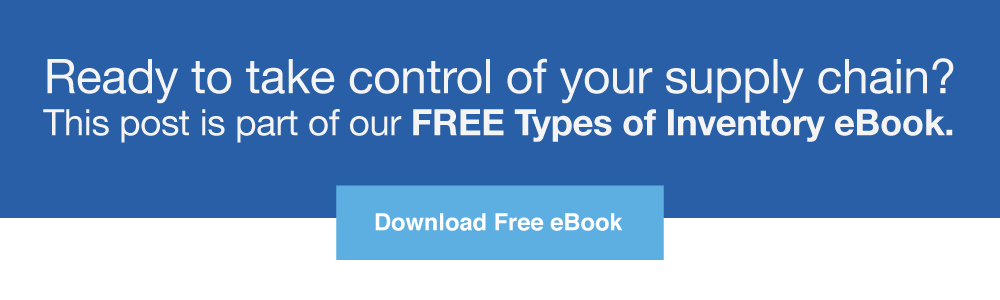
What Is MRO Inventory? An MRO Inventory Definition
MRO inventory stands for maintenance, repair, and operation inventory. The MRO inventory meaning is all the consumable materials, supplies, and equipment needed for manufacturing that aren’t a part of ending finished goods inventory.
MRO Inventory Examples
So, we know what MRO inventory is, generally. But what is MRO inventory specifically? Here are some MRO inventory examples that illustrate the type of supplies typically included in MRO inventory:
- Personal protective equipment (PPE) like gloves, masks, earplugs, safety glasses, hard hats, and respirators
- Cleaning supplies including disinfectant, brushes, mops, brooms, and buckets
- Office supplies like notebooks, pens, pencils, tape, post-its, etc.
- Furniture and lighting fixtures
- Personal technological equipment including desktop computers, laptops, printers, scanners, fax machines, paper shredders, and more
- Tooling and industrial equipment from lubricants, valves, bearings, and cutting fluid to parts and components like motors and gears
- Repair components, which vary widely based on the production process
- Laboratory equipment for any testing and research that precedes or coexists with manufacturing
Let's take alook at which of these items are used most often—and which fail most often.
MRO Inventory Examples: The Most Frequently Used MRO Items
According to a 2020 survey by SCMR, the most frequently used MRO items were maintenance and cleaning supplies. 70% of respondents said they used them. Safety equipment came in second at 68%, while third was forklift repair services at 66%.
Here are the full results:
MRO Inventory Examples: The Most Frequent MRO Equipment Failures
In that same survey, respondents were asked with MRO equipment failures they most often dealt with. Here they are:
Hopefully you’ve got a good idea of what MRO is, what typical MRO items are, and the risk of MRO failure that manufacturing businesses carry.
Now let’s look into how to mitigate that risk with sound MRO inventory management.
What Is MRO Inventory Management?
Neglected is the short answer. Longer answer, it’s the controls and practices that optimize MRO inventory replenishment.
Traditional inventory management expertise is usually brought to bear on what’s considered “traditional inventory.” Raw materials inventory, WIP inventory, manufacturing inventory, merchandise inventory, etc. All of these inventory types are subjected to cutting-edge demand forecasting and costing analysis.
But MRO inventory usually isn’t. Rarely is MRO inventory on-hand or usage measured. So it’s rarely optimized.
But why?
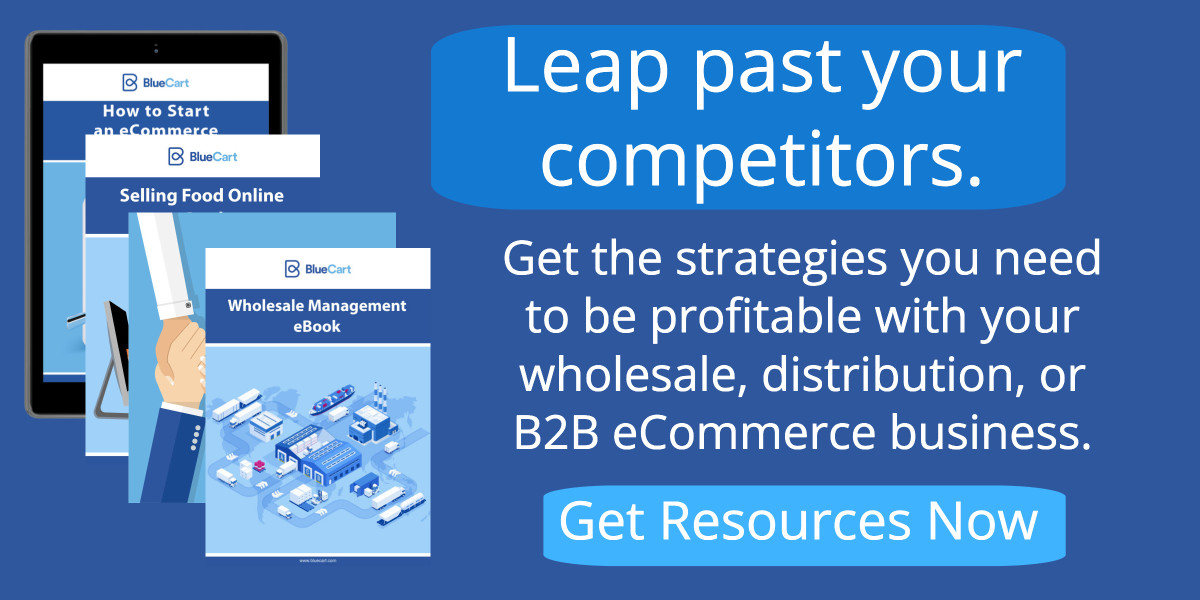
What Is MRO Inventory Management’s Problem?
MRO inventory management is relegated to a lower status for a few reasons, none of them very good:
- MRO inventory tends to turnover slowly, often less than once a year.
- Often MRO items urgently needed are obtained via expedited, on-the-spot purchasing.
- Businesses don’t want to distract highly-paid maintenance employees from planned maintenance and repair activities with inventory management processes.
- The misconception that a manufacturing business will always save money on bulk-discounts. The flipside is not being aware that a huge influx of MRO inventory, especially machinery components, increases becoming lost or obsolete over time.
- Hidden private inventories. Teams in manufacturing plants often keep their own private inventories to ensure they’re not crippled by MRO items drying up.
All of these conspire to make MRO inventory management one of the lowest-hanging fruits in manufacturing. Here’s how to pick it.
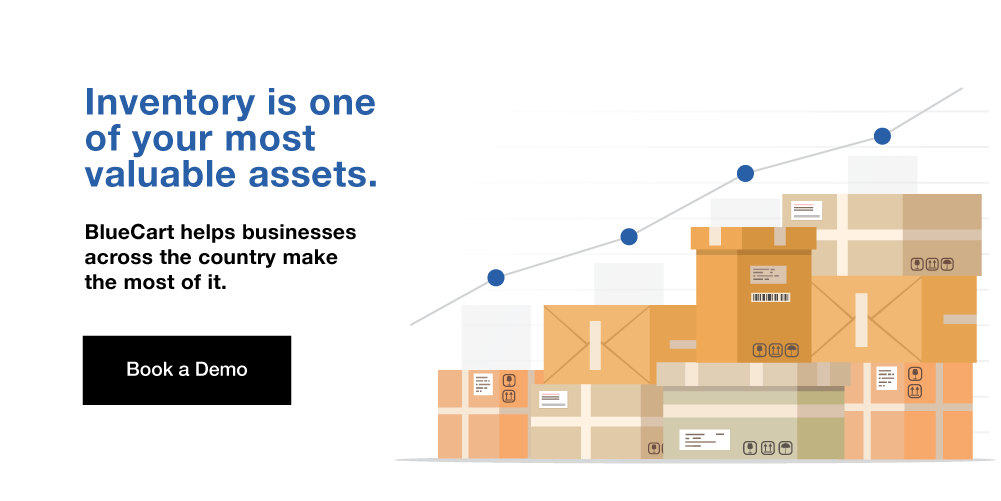
How Do Businesses Conduct MRO Inventory Management?
Three ways. Internally, outsourced to a third party, or a hybrid between internal work and outsourcing. Let’s go back to the 2020 SCMR survey. Of the respondents, 46% of manufacturing operations handle their MRO internally, 44% have a hybrid management process, and 8% completely outsource MRO.
Let’s look at the two most common approaches: internal and hybrid.
MRO Inventory Management: Internally
Using in-house ABC costing analysis, just in time inventory methods, and other tried-and-true inventory management techniques, many businesses go it alone.
17% of respondents to the SCMR survey who use internal staff only for their MRO management rated the process as excellent, 12% rated their process as very good, and 4% rated the process as poor.
The accepted benefits of handling MRO management internally are a greater control over MRO solutions and that it tends to cost less.
MRO Inventory Management: Hybrid
Again, hybrid means that some aspects of a company’s MRO inventory are managed by a third-party. Outsourced. 4% of survey respondents rated their hybrid MRO setups excellent, 25% very good, and 4% poor.
Imagine, for example, a vendor managed inventory setup. The manufacturer of a certain valve that you purchase monitors that valve’s inventory levels in your plant and places purchase orders for you.
That’s one way part of a company’s MRO inventory can be delegated to a third party. There are also companies dedicated solely to inventory management, which you can contract with for the specific purpose of MRO inventory control.
The accepted benefits within manufacturing of using third-party MRO services is that it frees businesses up to focus on their core functions, like maximizing their presence in an online marketplace. And that, well, third parties are just able to do a better job with MRO inventory control. Many industry folks also bring up an increase in labor productivity and leverage for purchasing discounts when using third-party MRO inventory management.
MRO Inventory Best Practices
Anyone looking for MRO inventory best practices will benefit from these seven MRO inventory control tips:
- Define the MRO inventory items that are business critical. There are some things that fall within MRO inventory that won’t cripple your business if they’re missing. But there are some that will. Identify those items, along with their usage rate and minimum reorder points. Whatever you do, don’t let the replenishment of these items slip through the cracks.
- Consider the entire organization when purchasing MRO inventory. Similar or identical MRO items may be required for multiple teams across your business. Look at each team’s needs together and see where you can drive efficiencies or qualify for bulk-order discounts.
- Talk to suppliers about VMI agreements. Offload inventory management to some trustworthy suppliers and lean into a hybrid MRO approach. You may find, like many survey respondents, that employees are more productive, MRO inventory management is smoother, and your organization can better focus on its critical business objectives.
- Use demand forecasting and analytics. Forecasting for MRO inventory isn’t intuitive because there is no explicit buyer demand for MRO items. But, like all successful inventory management strategies, MRO inventory management depends on demand forecasting. Know when your peak and low usage seasons are and adjust replenishment accordingly. Also, set key performance indicators (KPIs) like number of stockouts (helpful for planning safety stock levels), on-hand inventory, and reorder points and stick to them.
- Store all MRO inventory in a central, controlled location. This central stock area can be audited with computer systems to track and control all the inventory there. This not only encourages automated inventory management, but discourages private inventories. We’ve found this is consistently one of the most impactful MRO inventory best practices.
- Educate your staff about supply chain management. A lot of companies that keep MRO inventory control in-house use manufacturing personnel to manage it. Teach them in-detail about in transit inventory and supply chains—and their place in them—to expand their skill set and get your MRO inventory under control.
- Do a quarterly audit of your MRO inventory to make sure your MRO inventory doesn’t get bloated. MRO inventory grows and shifts as your production methods change. And your production methods shift based on a host of factors: current technology, demand, location, raw materials inventory, you name it. You are bound to have some MRO inventory that’s obsolete, no longer needed, or no longer needed in the quantities ordered.
Hit all seven of these, and you'll be optimizing a part of your business that most companies barely think about. Talk about a competitive advantage.
And You Know the Craziest Part?
Many MRO supplies needed are actually on hand, but businesses can’t find them.
So the next time you’re digging deep into your raw materials or work in process inventory, think twice about lonely old MRO inventory.
There is much to be found in forgotten places.
Frequently Asked Questions About MRO Meaning
After learning more about MRO, you may have more questions about how to handle it well. We compiled some commonly asked questions about how MRO works. Take a look below:
What Does MRO Mean in Supply Chain?
In supply chain matters, MRO stands for maintenance, repair, and operations. It refers to the expenses and material upkeep associated with a business’s output of products or services.
It’s important to have an MRO replacement plan in place so you can maintain operations at all times. If you’re a business owner, sitting down with your management team to learn more about common setbacks and material needs is a good place to start.
What Is an MRO Material?
An MRO material is any physical object having to do with business maintenance, repairs, and operations. This means any material or tool that helps employees do their job, but is neither part of the end product or service, nor central to the company’s output.
Examples of MRO include personal protective equipment (PPE), batteries, machine part replacements, office supplies, computers, and furniture. MRO is anything that indirectly helps staff perform a work function or complete a service.
What Is MRO Strategy?
An MRO strategy is a combination of a budget and a strategic plan for the procurement of MRO goods. MRO strategy is about listing the materials a company and its staff needs to perform work functions on a regular basis.
A sound MRO strategy takes into account not only daily workplace needs, but emergency scenarios where rare supplies are needed. This includes everyday equipment like gloves, vests, and scissors, but also hazmat suits, reflective vests, and hardhats.
MRO supplies can be expensive, so instead of buying at random, financially project what you’d need to replace throughout one year. This can show you the costs of some items versus others and how to budget accordingly. Use your findings to create your MRO budget and assign the responsibility to the right warehousing staff member.
What Is MRO Spend?
MRO Spend refers to the purchases of all goods and services that are required for a company to run efficiently. MRO stands for "Maintenance, Repair, and Operations."