Do you know the optimal reorder point for your best-performing products? What about the par level?
If not, you could be missing out on a lot of revenue or spending more on inventory carrying cost than necessary. Ordering at the correct time can ensure you always meet demand, helps with inventory reduction, and streamline your inventory control.
Keep reading to learn what a reorder point is, how to calculate it, and how it can benefit your business.
.jpg)
What Is Reorder Point?
The reorder point, or reorder level, is the amount of standing inventory on-hand that triggers a reorder. Essentially, when you hit this inventory number, you should reorder products to ensure you continue to meet demand without any gaps and optimize your inventory turnover ratio. It is a vital number for any inventory control manager (see inventory control manager salary) to calculate.
Reorder point is not a stable number, but is flexible based on sales trends and the demand cycle of a given product. This means you need to have an understanding of each product's inventory levels and sales to optimize its reorder point. This is easily done using inventory management software that tracks everything you need to know about your inventory.
Reorder Point Formula
Uncovering the reorder point for a product can be done using a very simple formula.
Here's that formula:
Reorder Point = (Average Daily Usage x Average Lead Time) + Safety Stock
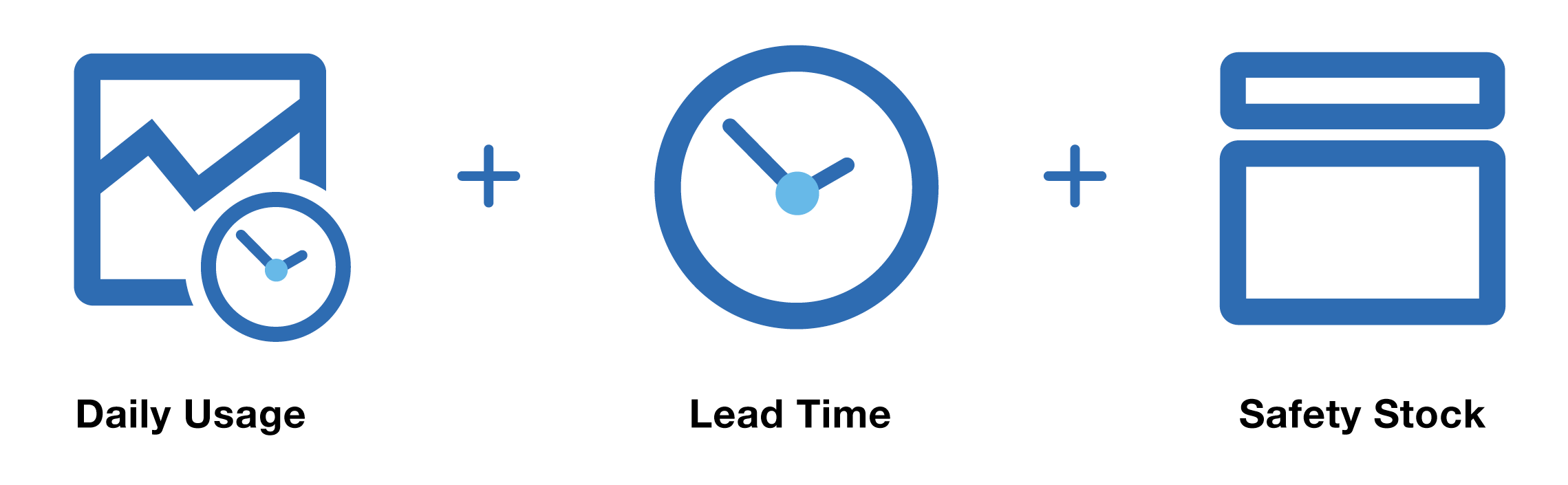
How to Calculate Reorder Point
Calculating the reorder point for a given product first requires that you determine a product's average daily sales, lead time, and amount of safety stock. You can easily pull daily sales information from your POS system, online marketplace, or multichannel order management platform if you have any of these. If you don't you can look at inventory numbers and divide by the number of days between taking inventory. Download our free inventory tracking sheet to make your job even easier. Safety stock levels are also noted on this sheet.
Lead time can also be calculated for the product using a simple formula or by using a lead time calculator. With these three numbers in hand, it's as simple as plugging them into the formula above to determine that product's reorder point. Repeat as necessary for each item in your inventory.
Optimal Reorder Point & Optimal Reorder Point Formula
The optimal reorder point will maximize the profit you can make from your stock and avoid surplus inventory in your warehouse. This is the point at which you need to order product to replenish your stock.
The formula to determine optimal reorder point is the same as above. The main difference is that you must calculate your reorder point for a product each day. This will update your data and let you determine the most optimal time for reordering. It also allows you to notice sudden shifts in demand and react accordingly to avoid causing the bullwhip effect in your supply chain.
Or Use a Reorder Point Calculator
Reorder point calculators are a convenient choice if you have a large inventory with many SKUs. One may be a part of the inventory management software you use or you can use an Excel sheet with built-in formulas. You can find the latter below.
Inventory Reorder Point Excel Template
Manual inventory tracking and reorder point calculation can be time-consuming, tedious, and error-prone.
To help make things easier for you, we've put together a simple inventory tracking sheet. Just download the inventory reorder point excel template, change the sample data to your own, and begin tracking!
Reorder Point Problems and Solutions
Determining your optimal reorder point isn't always easy. There are a number of issues that can hamper your ability to make the most informed decisions. Here are just a few of the issues you may encounter.
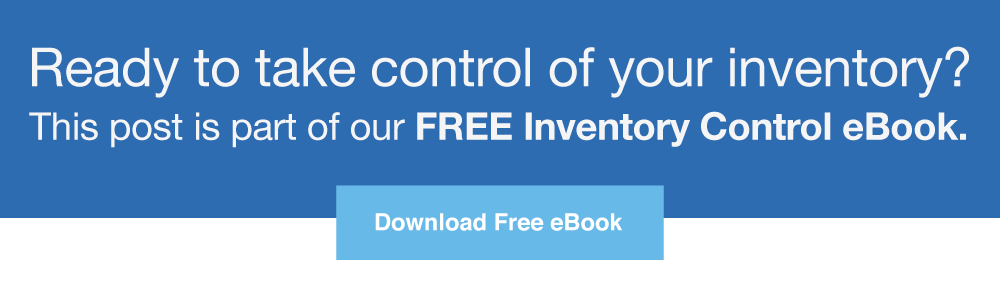
Safety Stock, Lead Time, and Reorder Point
Safety stock and lead time are the two more common causes of problems determining reorder points. However, both can be compensated for if you're adequately prepared.
Safety Stock and Reorder Point
Safety stock is additional stock you keep on hand in the event that demand suddenly increases. The major issue here is that you may go through this stock more quickly than anticipated. This means you need to reorder earlier than anticipated. Luckily, that is exactly why you keep safety stock on hand.
To combat any sudden shifts in demand and safety stock usage, track daily sales and recalculate your reorder points regularly. A perpetual inventory count is ideal for this, but taking an inventory cycle count is also a good choice if you still take physical inventory.
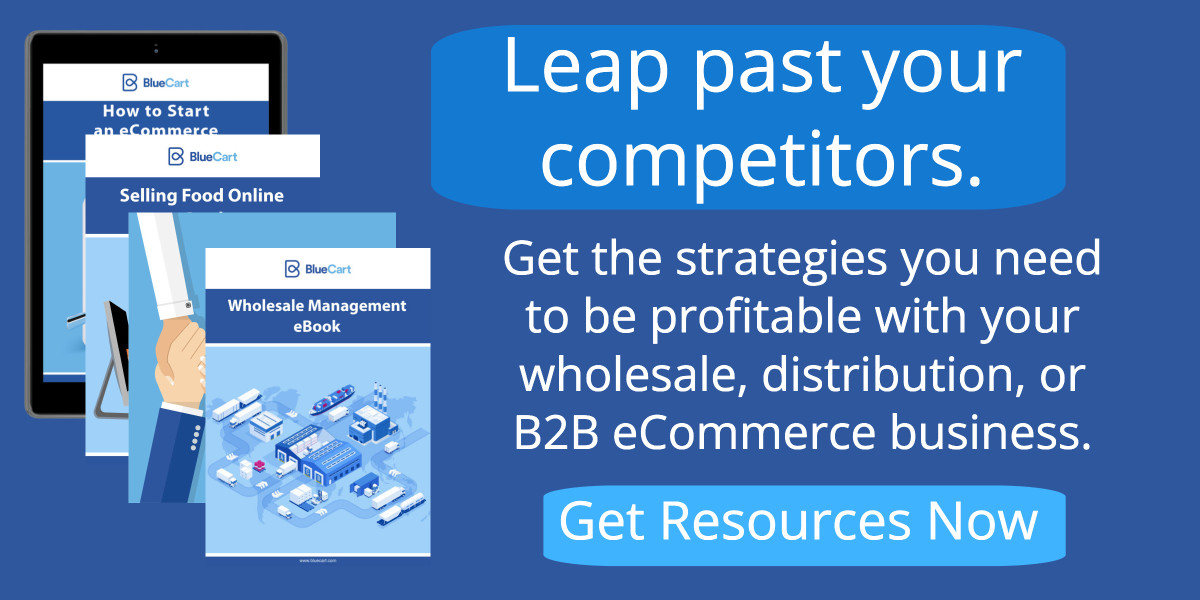
Lead Time and Reorder Point
Lead time is the second issue that may interfere with calculating your optimal reorder point. Unfortunately, you don't have much control over lead time as it is dependent on the supplier and shipper. However, there are two ways you can prepare yourself for any issues in lead time.
First, by keeping an adequate safety stock on hand. That way you can still fulfill orders and use batch picking while awaiting products in shipment. Second, calculate your reorder point daily to notice any changes in lead time as they occur. This way you can order product earlier if you discover any issues when inventory forecasting.
Reorder Point Model
The reorder point model is an option for businesses that use perpetual inventory management and want to avoid any excess storage. It is a very strict inventory model and will only work for certain businesses.
It requires the following to be true about a business:
- Demand is relatively stable year-round. If there are seasonal shifts in demand, reorder points can fluctuate greatly and this model may not be able to keep up.
- Lead time is constant. If lead time shifts, your products may not arrive in time. Then, you run into issues with products that could turn into a backorder and your fill rate.
- Price per unit and order costs are constant. Costs should be constant for each SKU number so you can ensure you have enough cash on hand for full reorders.This is especially true if your suppliers require an MOQ (what does MOQ mean?).
- Suppliers can always meet demand. Not all suppliers can always fulfill the orders they receive. This can't be the case if you run a business that orders and expects goods in an optimal time frame.
.jpg)
-
Did You Get the Point?
Calculating reorder points may not seem like fun, but they can help you get the most value out of your inventory. It's a vital part of calculating your optimal economic order quantity. Use the information we've shared here to control your inventory and make informed decisions that increase your bottom line. It's an important part of our inventory control guide.
One issue that you may discover when performing an inventory audit is that you have dead stock (see dead stock meaning) in your inventory. This inventory should not be reordered and you should offload it to make more room for profitable goods.