These days, most companies require maximum efficiency in order to meet customer expectations and stand up to their competition. It’s possible to do this with automated equipment and technology such as a warehouse control system.
In the past, companies would handle their order fulfillment operations without much automation and only a warehouse management system. By adding extra software, a business owner could get more value out of their equipment.
This blog post covers what a warehouse control system is and how it can help a business become more efficient. With this information, you can decide whether it’s the right choice for your company to pursue, similar to distributed warehousing.
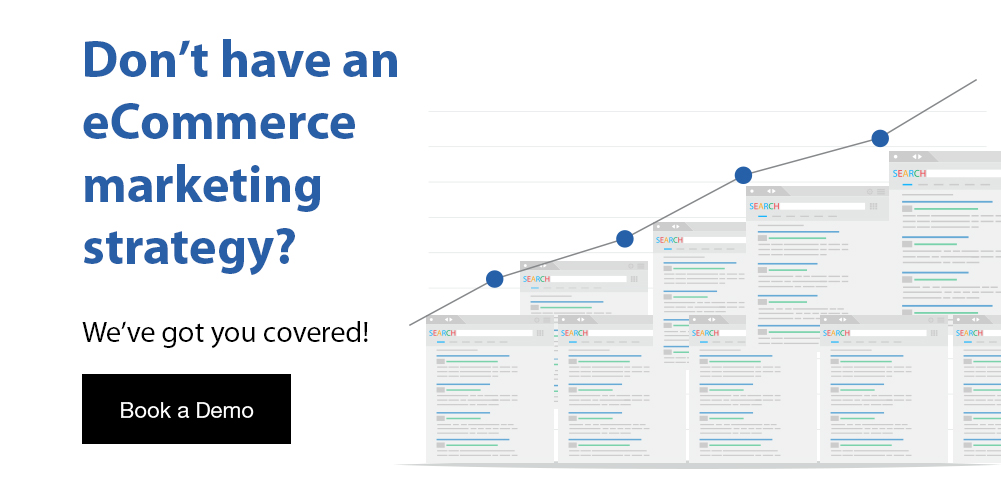
Warehouse Control System Meaning
A warehouse control system is software that allows businesses to direct the flow of their inventory in each warehouse or distribution center. It also makes it possible for businesses to coordinate tasks between subsystems including sorters, carousels, and conveyors.
As a result, their flow of inventory will run smoothly throughout the inventory storage and shipping process. Using a warehouse control system helps optimize warehousing operations while also allowing you to organize inventory until it’s time to ship.
A business may have a single warehouse control system to control all automated technology. It’s also possible for a business to have multiple warehouse control systems where each one controls each type of equipment.
Such equipment may include automated storage systems, palletizing equipment, printing equipment, and goods-to-person technology. This kind of automated equipment streamlines the warehouse process flow and operations.
Key Takeaway: Businesses may decide to use a warehouse control system to oversee the flow of inventory and related activities. This system works seamlessly with existing systems such as the warehouse management system.
4 Factors That Make a Good WCS
Understanding what makes a good warehouse control system will help you implement one in your business or optimize your existing one. Below are four factors that you should consider for your warehouse control system.
1. Planning Tools
It’s possible to have efficient operations within your business with the good planning tools that your warehouse control system offers. For instance, businesses can use material flow planning tools to help visualize and stimulate the process. This way, you can efficiently utilize material handling equipment and ensure the integrated subsystems are working together properly.
Having an optimal material flow will enhance the overall efficiency of your business. A warehouse control system with proper planning tools allows you to control the material flow of your inventory based on different product characteristics. As a result, you can strategically group orders.
2. System Visibility
A business should have access to real–time tracking and monitoring in order to have full transparency into the activities of its warehouse. This is a crucial factor of a warehouse control system.
With system visibility, you can better control business and warehouse operations with enhanced compliance with industry standards. This will also make it possible to set up exception alerts in order to identify and resolve issues before they result in bigger ones.
3. Flexible Interfaces
Having a flexible and user-friendly warehouse control system interface makes it possible to implement it across multiple devices. This includes integrating existing systems in order to minimize the risk of disconnecting and disrupting different warehousing activities.
A smooth and flexible integration can simplify and streamline operations. By doing this, you can improve inventory management processes, and focus on warehouse labor and equipment through a single platform.
4. Automation Control System
Using a warehouse control system can save time while optimizing warehouse processes. As a result, automating processes should be the core goal of the system.
The ideal warehouse control system will automate tasks and integrate with the existing warehouse infrastructure. This includes warehouse control system software and equipment such as sortation control systems, conveyor control systems, and automated storage and retrieval systems.
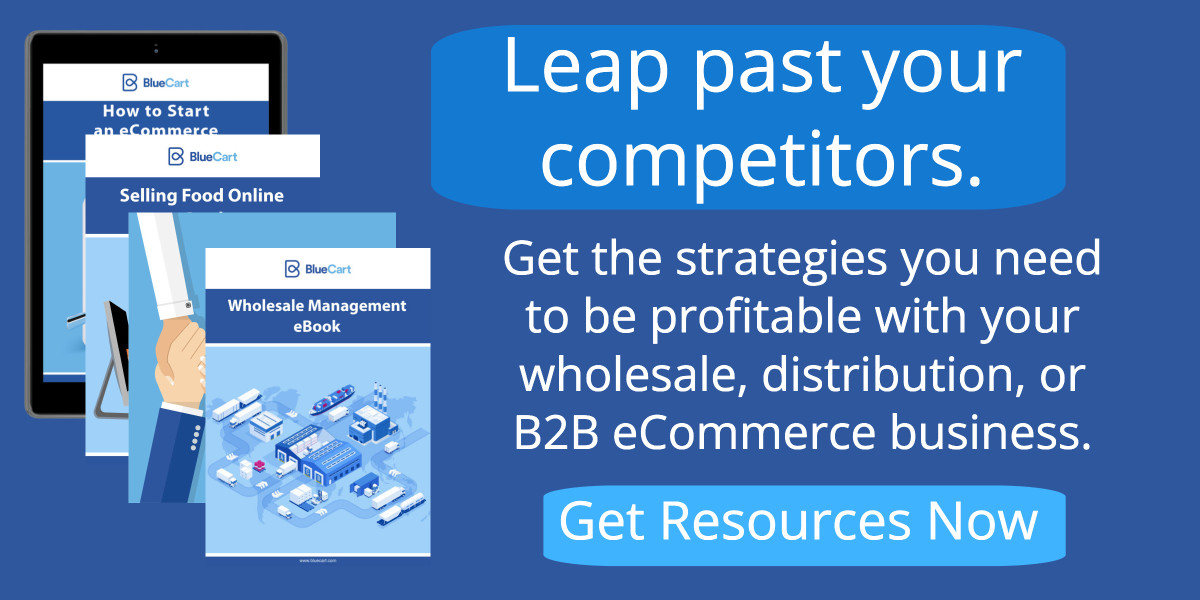
How Does a WCS Work?
The way a warehouse control system works is based on a few key supporting and performing functions. These include the following:
- Exchanging important information with higher-level software applications. This includes a warehouse management system that allows material handling functions to automatically perform. It also makes it possible to track the flow of products within the warehouse.
- Communicating with material handling equipment and subsystems in real-time. This allows businesses to coordinate the activities and movements of automated equipment.
- Determining the ideal route for products. Such a process controls the direction of the material handling equipment. This equipment includes carousels, conveyors, sorters, and scales. With this, you can ensure the products are transported as necessary.
- Using data to manage and monitor automated warehousing systems in real-time. Such data is derived from system-level sensors and controllers. This allows businesses to improve operational efficiency and enable quick diagnostics if something stops working or goes wrong.
Understanding the way a WCS works is essential because it allows you to evaluate whether your business can utilize it. This is similar to identifying the needs for warehouse inventory software and warehouse management software. All of this should be essential for your warehouse distribution business and its warehouse order checklist.
WCS vs WMS
It’s important to understand the difference between a warehouse control system (WSC) and a warehouse management system (WMS). This will allow you to operate with each system and utilize it to the best of your ability.
A WMS focuses on managing the inventory flow within a company’s distribution center. This is done by assigning labor tasks and tracking each order from the receipt to the shipping. It also stays up-to-date with reporting.
It’s important to note that a warehouse management system doesn’t have the capabilities a warehouse control system does. For example, a WMS cannot manage machines and equipment, sorters, cartons, conveyors, and put-to-light systems.
While a WMS knows a company’s overall inventory flow, it requires a WCS to provide information about where items, pallets, and cartons are when they move through the different automated systems in the warehouse. It’s essential to have a WCS if your business operates a highly-automated facility. This will ensure smooth operations and order and inventory tracking.
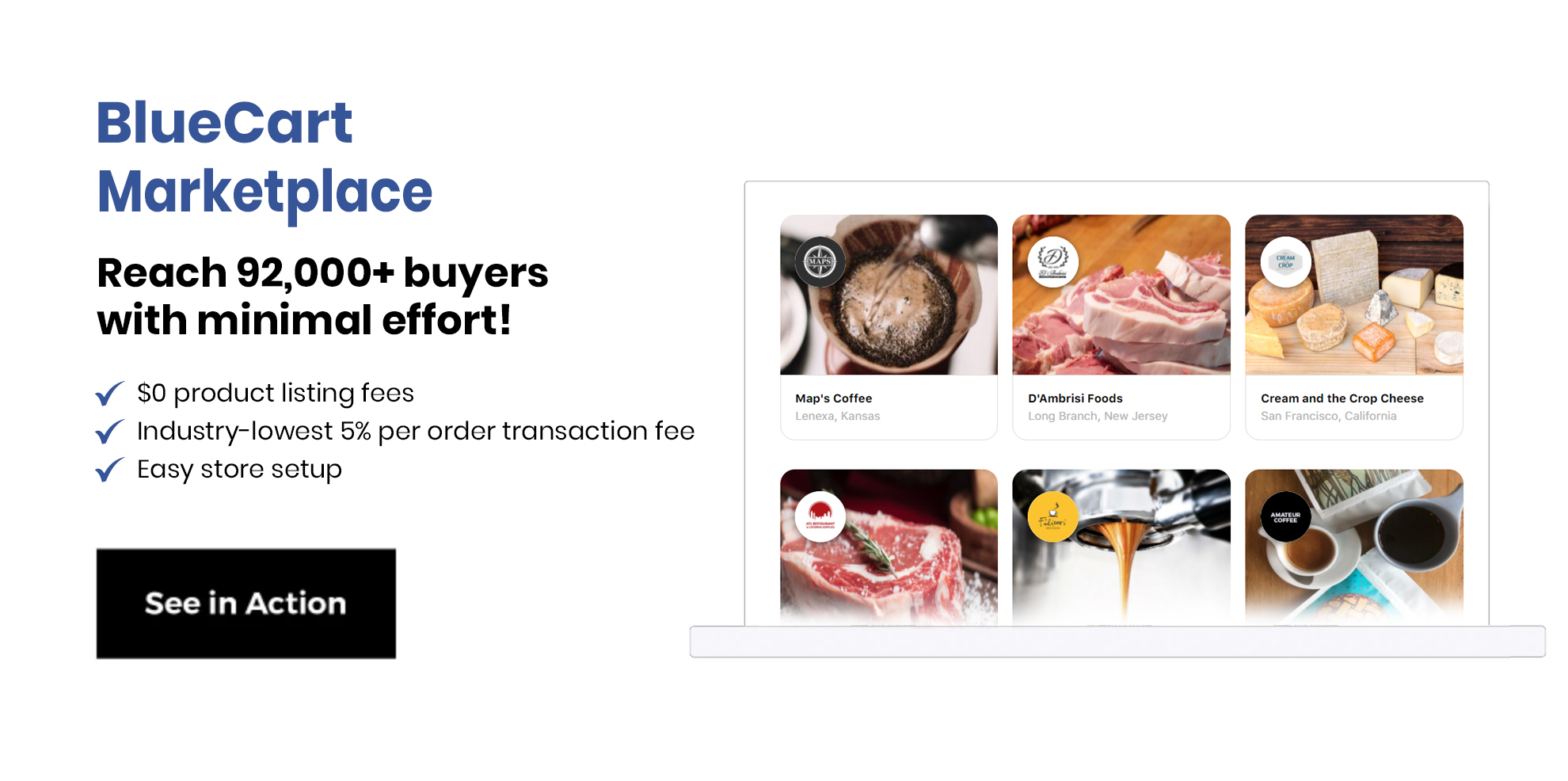
Frequently Asked Questions About Warehouse Control Systems
For most companies, the warehouse control system will control automated systems that handle equipment and integrate with the warehouse management systems. The warehouse management system manages and plans each warehouse activity from the receiving step to the shipping.
The WMS directs material handling procedures and the automation systems that the warehouse control system manages. To better understand why your business may need a warehouse control system, read the following commonly asked questions.
What Is the Difference Between WCS and WMS?
The primary difference between a warehouse control system (WCS) and a warehouse management system (WMS) is that a WCS offers real-time integrated control solutions that manage different warehouse tasks. A WMS, on the other hand, focuses on broader processes including labor management, orders, and shipments.
What Is the Primary Objective of a Warehouse Control System?
The primary objective of a warehouse control system (WCS) is to make sure the flow of inventory runs smoothly by monitoring various warehouse automations. This includes machines and equipment utilized to move inventory through the different order stages.
What Three Systems Are Used in a Warehouse?
Three systems commonly used in a warehouse include:
- Warehouse control system (WCS)
- Warehouse management system (WMS)
- Warehouse execution system (WES)
The most common system is a WMS and both warehouse control and execution systems can integrate with a WMS as the business grows. This is important once the business has more complex automation and warehousing needs.