Every warehouse needs to define where and how products are moved. This is called warehouse management process flow, and it’s important to have it in place before the order fulfillment process begins.
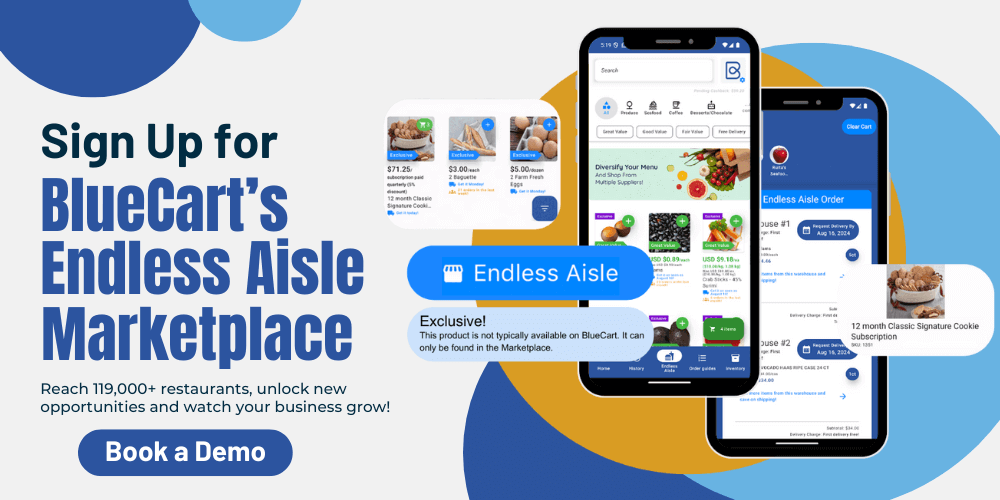
Key Takeaway: There are multiple reasons to be interested in warehouse process flow. Maybe you want to brush up on what is warehouse work, so you can determine who you need to hire. Perhaps your business is developing its first warehouse; in which case, check out what is warehouse. No matter why you’re reading, completing your business process flow has an early payoff.
A well-designed warehouse management process flow saves your business time and money. It defines all the stages in your warehouse operations, so you can focus on getting work done. Keep reading to discover more than one business process flow chart and how to integrate any of them into your warehouse operations.
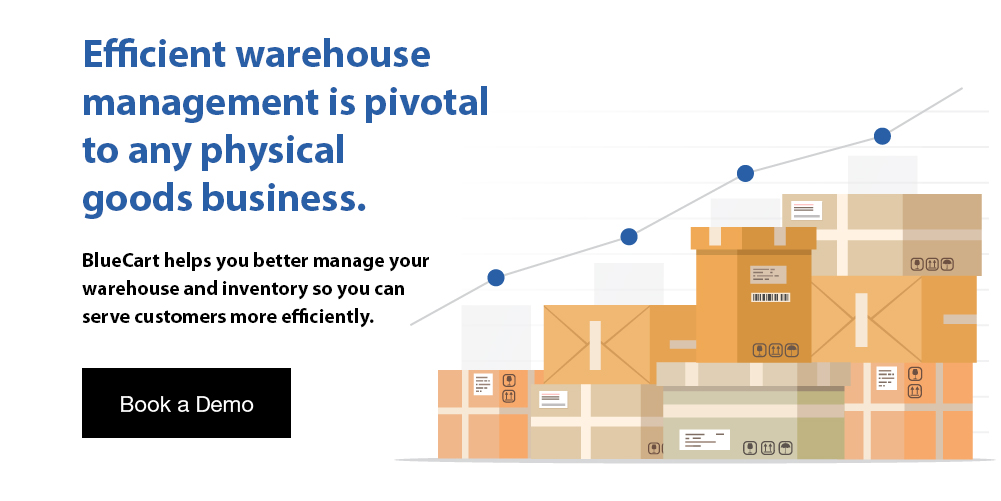
Warehouse Management System Process Flow
A warehouse management system process flow is a visual chart or diagram that shows the main activities of your warehouse. It's a subcomponent of warehouse organization. A process flow illustrates how goods are received, the process they go through, how they are shipped, and any stages in between.
A process flow can be created through a few methods. You can use graphic design software, the data from your warehouse management system (WMS), or programs like Microsoft Word and Excel.
It’s recommended to spend plenty of time on your process flow, as it can translate to thousands of dollars and dozens of hours saved each year.
If you use a WMS, creating a process flow is easier. First, export the data you need from your WMS, which provides a detailed account of all the stages your products go through. Examples of data may include product lists, courier reports, and a list of products held longer than 90 days.
Second, use the data to identify the process flow steps that apply to your warehouse. You can do this in conjunction with an ABC inventory analysis. If you have an unexpectedly high number of C products (goods that spend too much time in the warehouse), your process flow should be improved.
Your warehouse management system process flow should correspond with your business's needs and how your online marketplace runs (if you use one). It’s advisable to adjust the simplicity or complexity of your chart to streamline warehouse operations.
Warehouse System Flow Chart
A warehouse system flow chart illustrates the movement of warehouse goods in a visual format. All warehouse flow charts can be broken down into at least three stages: receiving, storage, and shipping. This type of flow chart works best for small warehouses or limited product lines, where products aren’t separated after receiving.
Here is an example of a simple warehouse system flow chart:
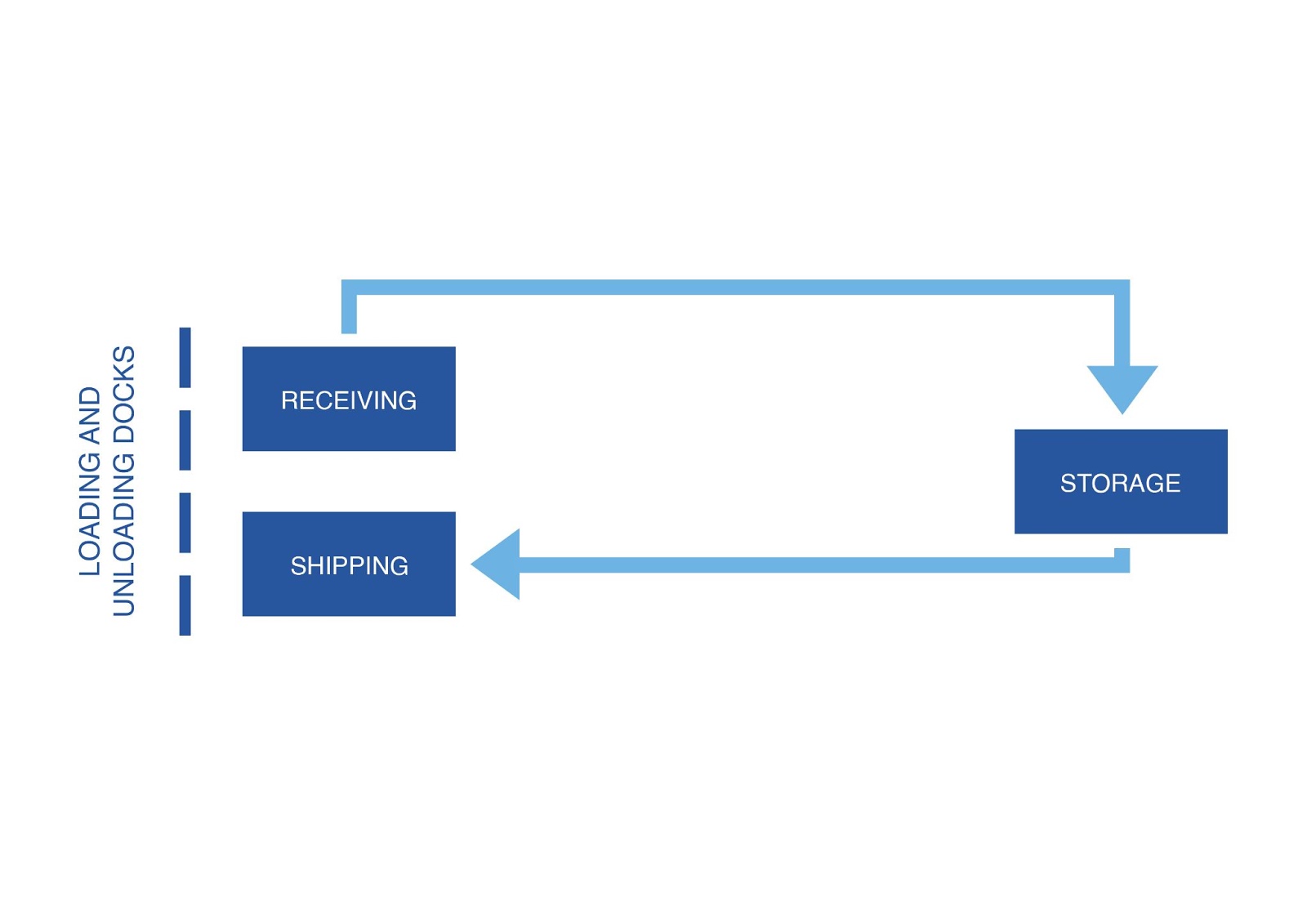
Medium flow charts are much more common and feature more steps. This kind of flow chart is useful for medium to large companies or those with numerous products.
In addition to the three simple flow chart steps, medium charts include areas for preparatory tasks. This includes multiple storage sections, cold storage vs. room temperature storage, a picking and packing area, and shipping staging or consolidation.
Here is an example of a medium warehouse system flow chart:
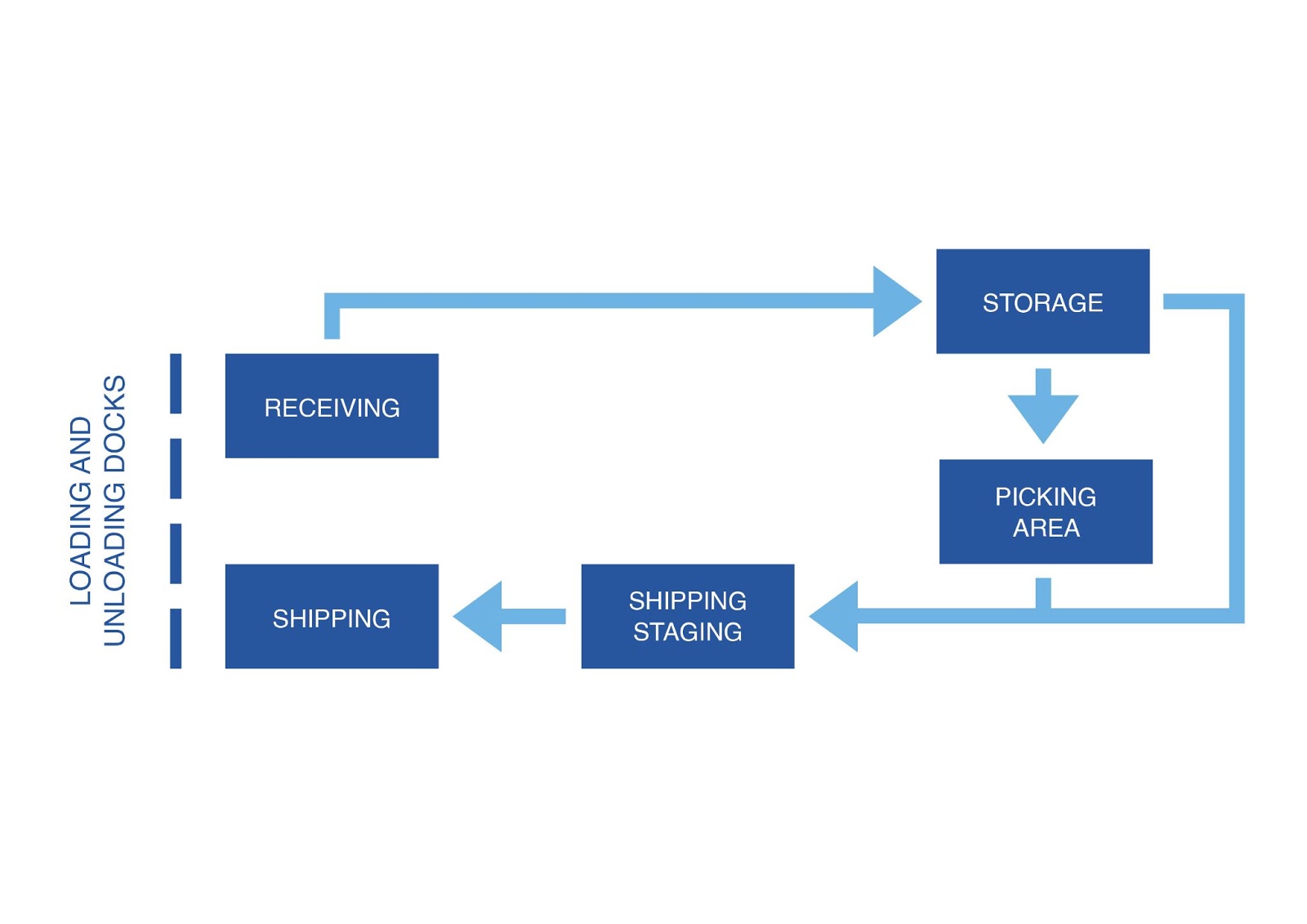
Complex warehouse system flow charts may have 10 stages or more, depending on the products’ needs. These flow charts are common for temperature-controlled products, businesses with high-value inventory, or products with many parts.
Stages in a complex flow chart may include a reserve warehouse, handling area, production, quality control, and shipping preparation. Some or all of these stages may be present or modified, based on the type of business.
Here is an example of a complex warehouse system flow chart:
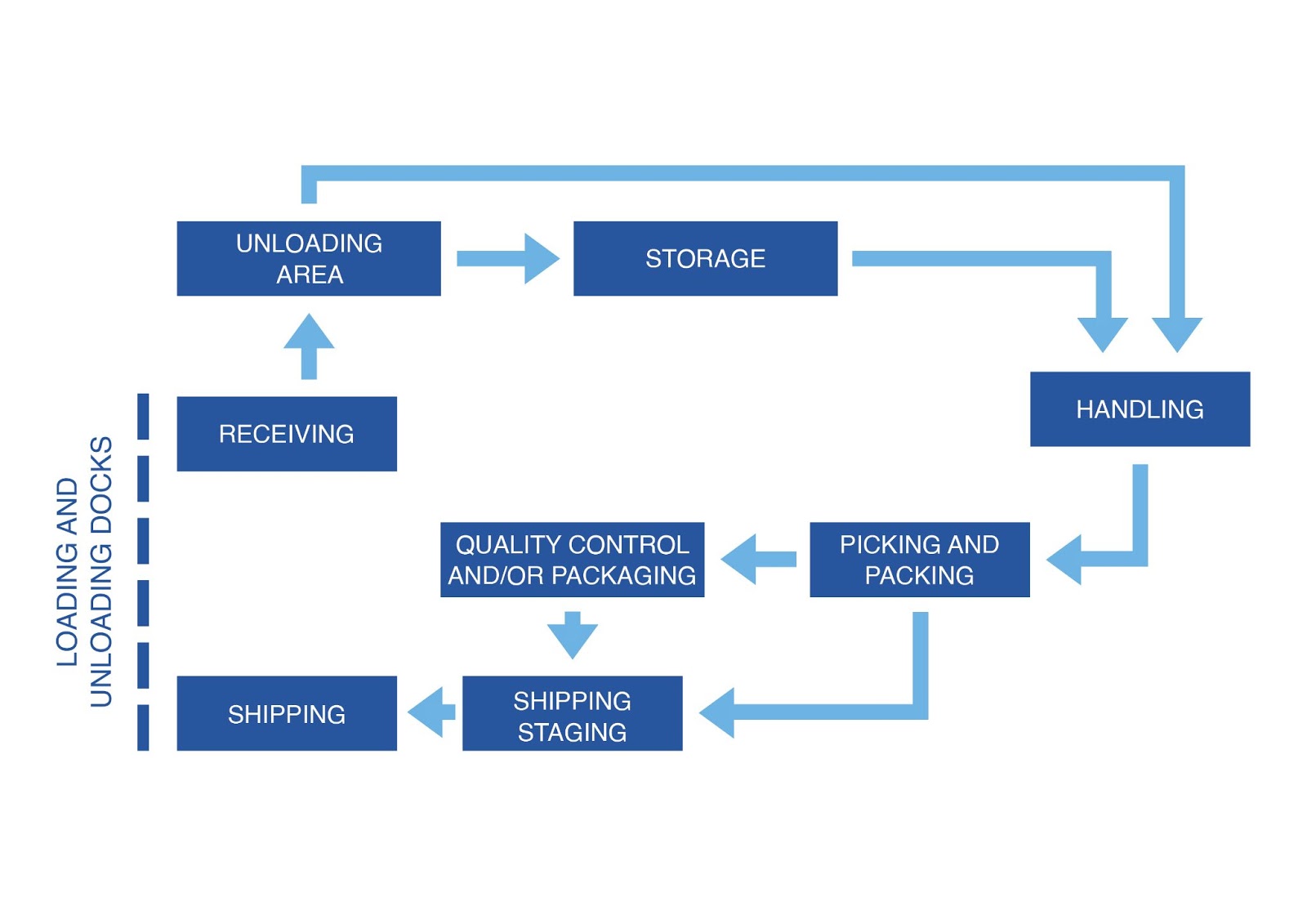
Warehouse Outbound Process Flow
Understanding your warehouse outbound process flow is important for organizational success. It’s a crucial component of satisfying both distribution service providers and customers.
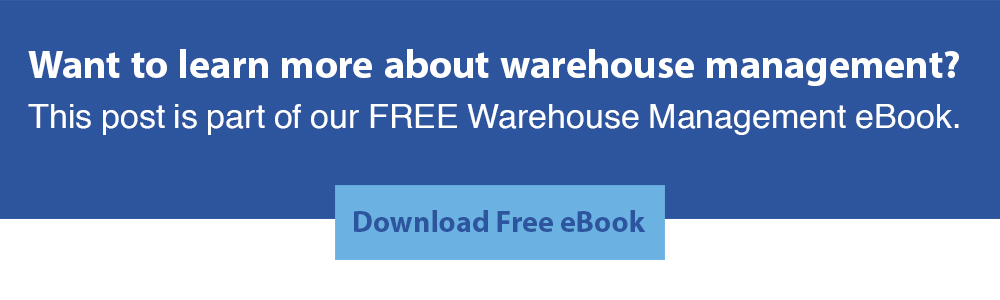
The outbound process flow should include the following steps at a minimum:
- Designate a packing area. The packing location in your warehouse should run like a well-oiled machine. Packing stations should include SKU numbers, barcode scanners, label printers, and packing materials, in addition to the computer for completing orders. Make sure your packing stations are always well-stocked in eCommerce packaging to prevent delays.
- Designate a shipping staging area. This is the location where completed packages are ready to be loaded onto a truck. Drivers can start loading up packages as soon as they arrive because your warehouse is efficiently organized.
- Monitor shipping and delivery notifications. Your warehouse management system (WMS) will provide an interface to see which products have been shipped and which are pending. Some WMSs also provide notifications when customers receive their orders. This eliminates excessive follow-up communication about packages. In the event a package runs into issues, contact your carrier for more information.
- Update your records. Your outbound process flow should include documentation of the products leaving your warehouse and where they went. Whether staff handles this manually or a program does most of the work, you need written proof of all finished work.
Want to better organize your warehouse, inventory, and individual products? Get our FREE SKU Generator Template.
Warehouse Outbound Process Flow Chart
Keeping your warehouse outbound process organized in a flow chart is good for maximizing efficiency.
Here is an example of an outbound process flow chart:
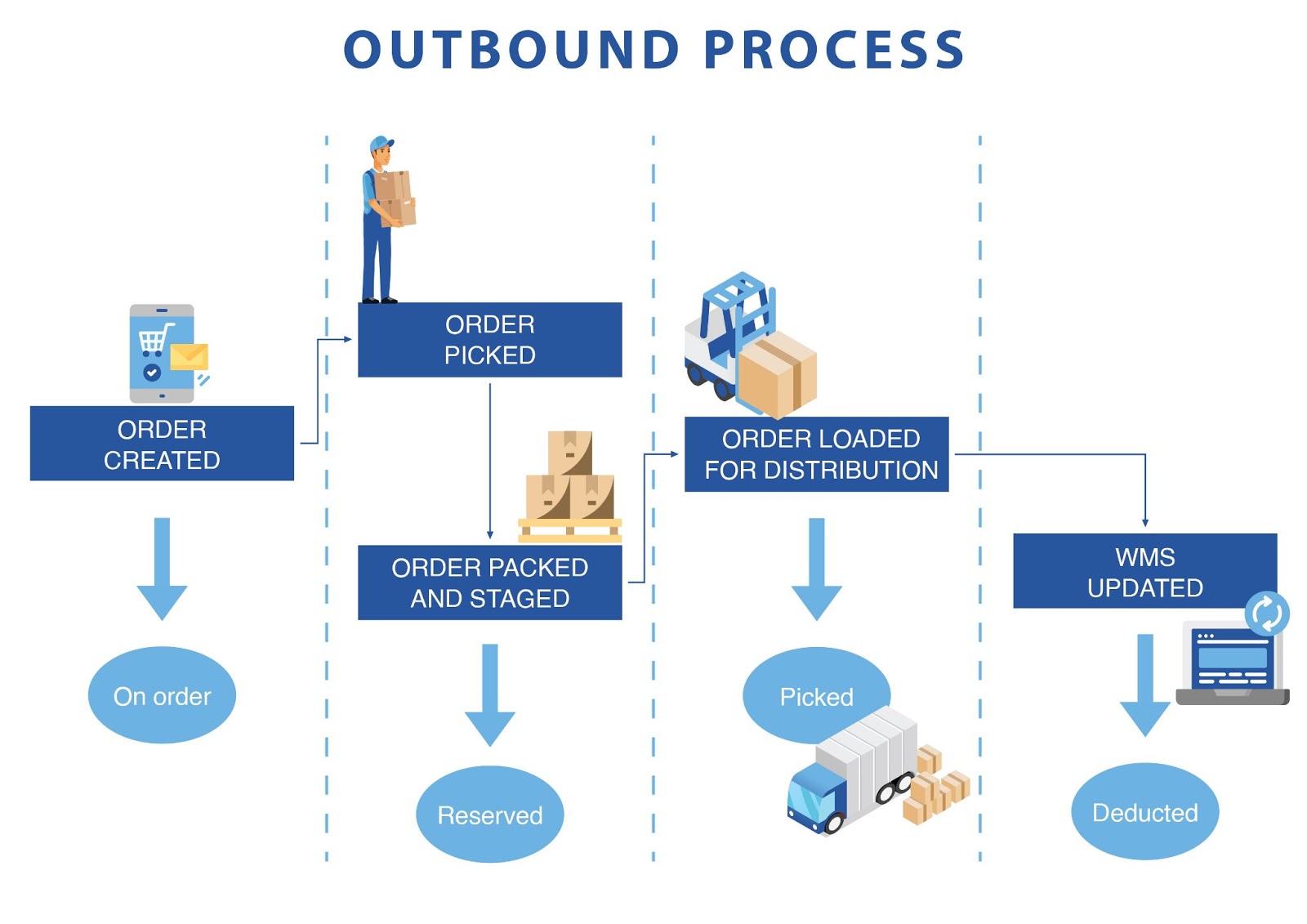
Warehouse Inbound Process Flow
Having a strong warehouse inbound process flow is pivotal to your business’s productivity. Depending on the challenges your warehouse faces, you may need to bring on new staff. Posting an appealing warehouse manager job description can get you candidates quickly. Be sure to include a strong warehouse manager salary, too.
Ready to unlock the full potential of kitting for your business? Discover the ins and outs of this efficient inventory management technique that can streamline your business operations, reduce costs, and improve customer satisfaction.
Once you have the right person hired, it’s important to afford the same level of focus to your inbound flow as it is your outbound flow. The inbound process flow of your warehouse should include the following steps:
- Schedule all deliveries. Don’t leave the timing of your deliveries up to chance. This will create a crowded delivery area and delays in unloading pallets. Provide an automated scheduling system for your delivery drivers, or mark down days and times in advance.
- Designate an unloading area. It’s easy to overlook the unloading area when making a warehouse inbound process flow. This is space used solely for breaking down cases and carting products to shelves.
- Include inventory management. Simply putting products on shelves isn’t enough; you need an inventory management process built on precision and speed. If your products have special handling or storage requirements, feature this in your process flow, too. Anything individual products need as a part of storage, like warehouse labels, should be part of the inbound flow.
- Update your reports. All of your customers’ orders are based on the numbers that your warehouse inventory management software uses. If it turns out a case never got put away or was damaged and never recorded, this directly affects outbound flow. Periodically check that all products are accounted for by running an inventory audit.
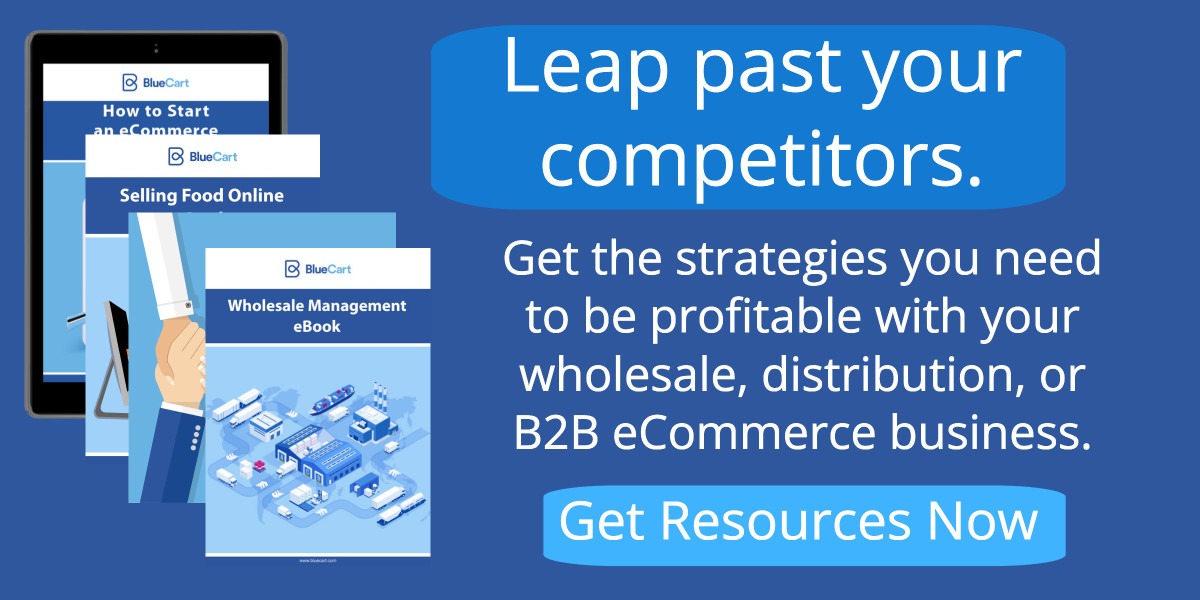
Warehouse Inbound Process Flow Chart
Writing everything down is a good start, but your final warehouse inbound process flow chart should be visual.
Here’s an example of what one can look like:
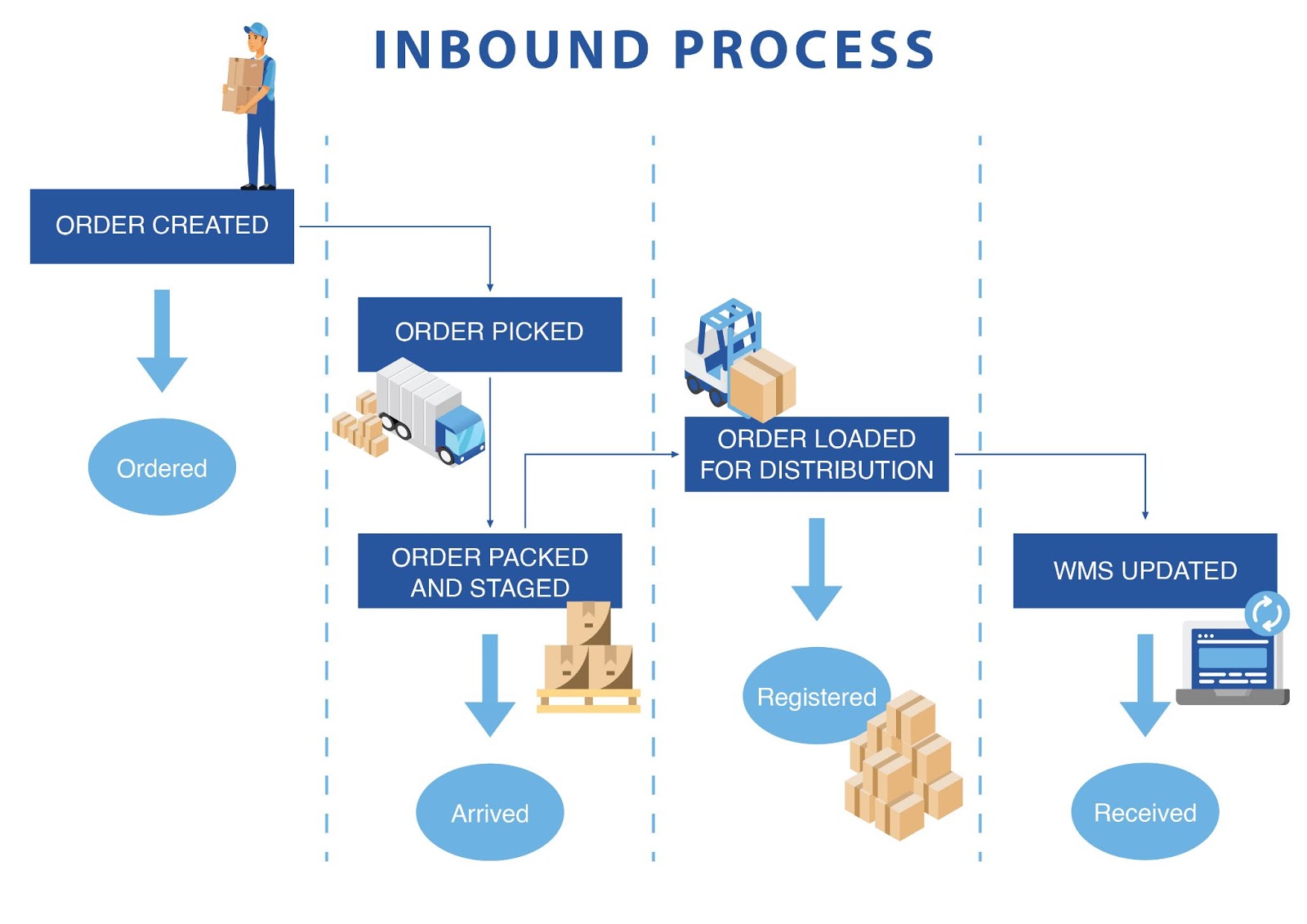
How to Optimize Warehouse Process Flow
Proper warehouse management and optimization of the process flow can allow businesses to reduce their warehousing and storage costs. Furthermore, it has the potential to improve customer satisfaction and business efficiency. Here are a few ways to optimize warehouse process flow.
- Proper analysis and data collection. When improving any aspect of a business, the first step is always to analyze the current state. This is done through proper data collection. Analysis should be done only after an adequate amount of data is collected and pain points can be identified.
- Layout optimization. Layout plays a crucial role in warehousing operations. Businesses should use both horizontal and vertical space optimally. High-turnover items should be placed on easily reachable places and near packing and shipping areas.
- Automation. Innovations in the field of warehouse automation allow companies to not only improve warehouse process flow but also to reduce labor costs. That’s especially true for repetitive tasks such as scanning. Thanks to modern RFID technology, they can easily be automated.
- Regular staff training. Investing in proper employee training programs will reduce human errors and improve operational efficiency in both outbound and inbound processes in a warehouse. It’s important to keep in mind that training isn’t just for new employees. A business that regularly invests in innovations should keep its existing employees up to date with the capabilities of new technologies.
- Performance monitoring. Warehousing operations should be monitored with proper key performance indicators (KPIs). They should be realistic but management should look for ways to improve these KPIs in order to make the overall warehouse process flow more efficient.
- Integrations. Even if your business uses the latest warehousing technology, it’s only efficient if it’s integrated with the rest of the business processes. Thus, the warehouse process flow should not be considered as a separate part of the company. Instead, it is an essential stage of the business and its other processes.
Frequently Asked Questions About Warehouse Process Flow
What are the 5 warehousing processes?
The five warehousing processes are:
- Receiving
- Putaway
- Storage
- Order picking
- Shipping
What are the main four flows in a warehouse?
The main four flows in a warehouse include the following:
- Inward flow
- Outward flow
- Internal flow
- Information flow
What types of flow are there in a warehouse?
The types of flow in a warehouse can include:
- Financial flow
- Material flow
- Data flow
- Documentation flow
What is warehouse order processing?
Warehouse order processing refers to the activities involved in receiving, managing, and fulfilling customer orders within the warehouse. It includes tasks such as order verification, allocation of stock, order picking, packing, and preparing the order for shipment.
How to Automate the Warehouse Process?
There are multiple ways to automate the warehouse process. Some of them include software while others rely on robotics. The goal of these technologies is to partially assist the staff or fully replace some functions. Here are some popular ways to automate the warehouse management process.
- Mobile robots. The main purpose of collaborative robots is to increase staff productivity and accuracy.
- Drones. Drones are primarily used in warehouse scanning. Warehouse drones are equipped with scanners capable of using barcode, RFID, or other technologies.
- Voice picking and tasking. These solutions improve the communication between employees and are among the most common ones.
- Goods-to-person (GTP) solutions. These systems deliver goods to employees for packing or assembling. Conveyor systems are an example of such technologies. Nowadays, automated storage and retrieval solutions (AS/RS) are the modern equivalent of GTP systems.
What Are the Trends in Warehouse Process Management?
The warehousing industry is changing rapidly, just like everything else. Here are the main trends in the warehouse management process.
- Automation. Drones, robots, and driverless forklifts are just a few examples of recent automation technologies with multiple applications in warehousing.
- Internet of Things. IoT solutions help monitor and control the environment. IoT also helps with inventory management and real-time data tracking.
- Sustainability. A lot of businesses aim to reduce their ecological footprint. That’s why sustainability is a trend in warehousing as well. From energy efficiency to waste reduction, there are many ways to achieve sustainability.
Rocking The Flow
As you create your process flow, it’s important to customize it for your warehousing needs. Take the time to verify that your warehouse process flow is getting products to customers efficiently. This will put you well ahead of the competition and keep your profits strong year over year. Your company's ERP software can improve your warehouse management process (see benefits of ERP).
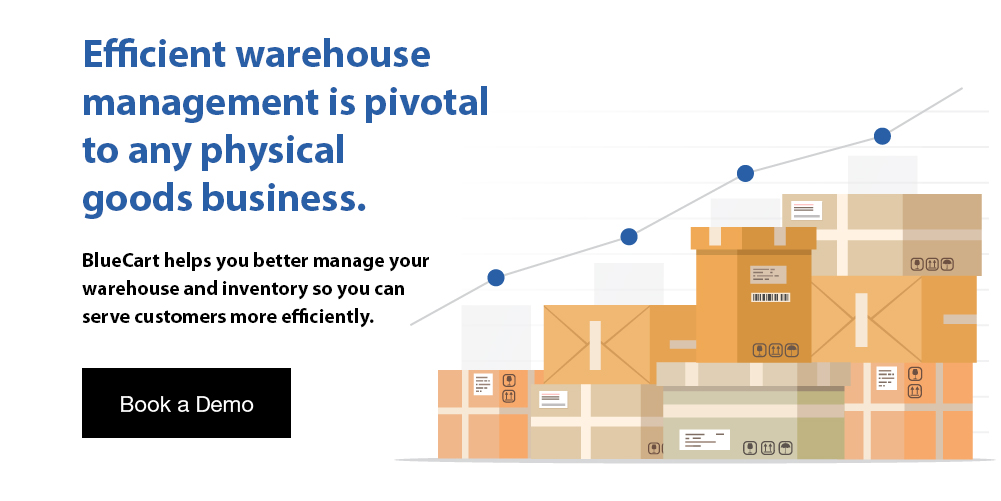