Do you have to wear safety boots in a warehouse? Is it illegal to not wear safety vests in a warehouse? Do I still need safety vests if I operate a smart warehouse? Stick around to the end to get the answers!
The truth is a lot of warehousing operations and processes are hazardous, no matter the type of warehouse you operate. As a business owner, ensuring the safety of your employees should be at the top of your list of priorities.
This is especially true when it comes to warehouse operations, where workers are handling heavy equipment, working with hazardous materials, and navigating busy work areas. That’s why it’s essential to regularly conduct warehouse safety inspections in your warehouse to identify and prevent potential hazards.
There are several warehouse safety regulations and rules, for instance, OSHA warehouse safety guidelines, to put in place. However, it may be difficult to keep up with all these regulations without a warehouse safety checklist.
To help you get started, we’ve put together a comprehensive warehouse safety checklist. In this blog post, we’ll be sharing 10 key tips for conducting effective safety inspections and ensuring a safe and secure working environment for your employees.
If you are just starting out your warehouse distribution business, these tips will help you identify areas for improvement and ensure that your warehouse is operating in a safe and efficient manner. So, without further ado, let’s dive into our warehouse safety checklist.
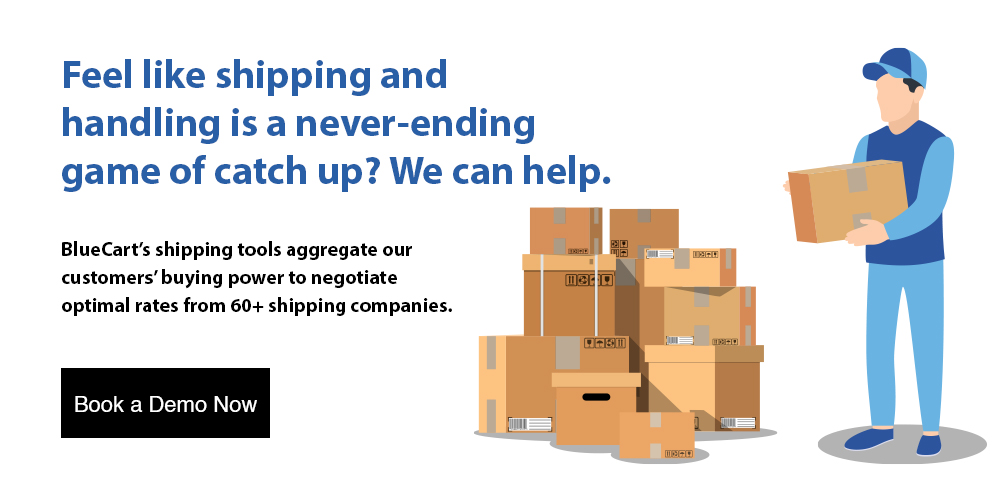
What is Warehouse Safety Checklist?
Warehouse safety checklist is a step-by-step guide that documents safety measures that must be put in place to prevent warehouse hazards and accidents. The checklist is typically used by warehouse safety officers and warehouse managers to identify safety issues within a warehouse inbound process flow.
Similar to a warehouse order checklist, a warehouse safety checklist outlines each process in the warehouse, from receiving goods and using heavy machinery to packing goods and fulfilling orders. The ultimate goal of the checklist is to prevent potential hazards.
As said earlier, there are several safety regulations to follow. One of such regulations is the OSHA warehouse safety guidelines. Let’s take a quick look at some of its guidelines:
- Ensure adequate ventilation in your warehouse.
- Use suitable lockout/tag-out techniques.
- Close off any area where a worker could fall more than four feet, such as exposed or open loading dock doors.
- Remove any obstacles that could lead to trips, slides, or falls from the floors, aisles, and surfaces.
- Employees should receive training on working properly in both hot and cold environments.
- Introduce suitable ergonomics to new hires for both general use and specialized activities.
- Ensure that workers who engage in physical labor take regular breaks.
- When estimating the amount of time it takes an employee to accomplish a task, take into account good work practices.
Without stating the obvious, why is safety important in a warehouse? Let’s find out.
Why is Safety Important in a Warehouse? 3 Reasons to Use a Warehouse Safety Compliance Checklist
Forklifts are the top risk across 7,000 warehouses in America, according to OSHA. Every year, the usage of these vehicles in warehouses causes 95,000 injuries and about 100 fatalities. The bulk of these fatalities are caused by forklifts that crash while operating on the warehouse floor. Broken or worn brakes are another problem.
Other safety concerns include:
- Trips, stumbling, and falling
- Chemical exposure, such as the vapors released by gassing batteries
- Inadequate thorough safety evaluation and training
- Ineffective danger communication
- Protection of floor, wall, and hole openings
- Putting emergency exits at the right place
- Inadequate lockout/tagout procedures
- Placement and application of portable fire extinguishers
These safety concerns are the reason having a safety checklist is important. OSHA regulates warehouse safety and warehouse managers that do not follow these regulations may incur lawsuits or fines.
The handling of heavy machinery and the growing shipment and storage of hazardous materials have enhanced the necessity of warehouse safety, which has always been crucial. A good safety protocol must be established, frequent safety training must be given, long-term and short-term warehousing procedures must be followed, and the right safety supplies and equipment must be used.
Here are some key reasons why safety is important in a warehouse:
- Keeps Your Warehouse Staff Protected
Employee safety should always be a top priority since it enables you to conduct your warehouse operations more efficiently without having to stop work or run the danger of an accident. Implementing a warehouse safety checklist ensures that no one has to ask questions like “are safety glasses required in a warehouse?”
- Reduces Inventory Damage
Numerous safety regulations guard against damage to your inventory. By storing goods appropriately, you can save products from dropping and getting damaged or even putting your personnel in risk, especially when it comes to heavier or larger items.
- Extends Warehouse Equipment Lifecycle
Properly maintaining equipment, such as forklifts, is one area of concern for warehouse safety. When equipment are misused, there is a higher chance it degrades quickly, costing more money in repairs and replacement parts.
Equipment maintenance will extend the life of the equipment and help ensure your workforce is aware of the nuances, including providing safety courses and certificates on how to operate these machines.
How to Improve Warehouse Safety: 10 Warehouse Safety Inspection Tips
When creating standard warehouse safety guidelines, it is important to look at OSHA safety regulations and enforce these safety rules in your warehouse operations. Let’s look at some key steps on improving warehouse safety compliance in your warehouse.
As a warehouse worker, your safety is crucial for a successful and productive work environment. Warehouse safety is crucial for avoiding accidents and ensuring the well-being of all employees. Here are 10 warehouse safety inspection tips to help you improve the safety of your warehouse:
- Conduct regular safety inspections - Regular safety inspections help identify potential hazards and address them before they become a problem.
- Check equipment and machinery - Make sure all equipment and machinery are in good working order and are being used properly.
- Maintain a clean and organized workspace - A cluttered workspace can increase the risk of accidents, so make sure to keep the warehouse clean and organized.
- Properly label hazardous areas and materials - Label any hazardous areas and materials to ensure that employees are aware of the risks.
- Provide adequate lighting - Adequate lighting is important for visibility and can help prevent accidents.
- Train employees on safe practices - Proper training can help employees avoid accidents and injuries.
- Ensure proper signage and warnings - Proper signage and warnings can help prevent accidents and inform employees of potential hazards.
- Maintain fire extinguishers and fire suppression systems - Fire extinguishers and fire suppression systems are essential for preventing and controlling fires.
- Provide personal protective equipment - Personal protective equipment such as hard hats, safety glasses, and gloves can help protect employees from accidents.
- Keep exits clear and accessible - Make sure all exits are clear and accessible in case of an emergency.
Complete Warehouse Safety Checklist
A complete warehouse safety checklist is a critical tool that helps ensure a safe and hazard-free environment for workers and visitors. This list provides a comprehensive overview of the essential measures that need to be taken to maintain a safe warehouse environment. Here is a complete warehouse safety checklist:
- Fire Prevention and Protection
- Install fire alarms, fire sprinkler systems, fire extinguishers, and smoke detectors throughout the warehouse.
- Ensure that fire exits and emergency evacuation routes are clearly marked and unobstructed.
- Electrical Safety
- Check electrical wiring and outlets regularly.
- Repair any damaged or exposed wires.
- Avoid overloading electrical outlets.
- Ensure that all electrical equipment is properly grounded.
- Floor Safety
- Check floors regularly for cracks, holes, or any other hazards that could cause slips, trips, and falls.
- Mop up spills promptly.
- Ensure that walkways are kept clear and unobstructed.
- Equipment Safety
- Regularly inspect and maintain all equipment, including pallet jacks, forklifts, and ladders.
- Train workers on the proper use of equipment and safety procedures.
- Hazardous Materials
- Store hazardous materials in designated areas
- Ensure that they are labeled appropriately.
- Train workers on the proper handling and storage of hazardous materials.
- Personal Protective Equipment
- Provide workers with appropriate personal protective equipment, such as hard hats, safety glasses, and ear protection.
- Train workers on the proper use and maintenance of personal protective equipment.
- Emergency Preparedness
- Develop and regularly review emergency evacuation plans.
- Provide workers with training on emergency procedures.
- Ensure that first aid kits and other emergency equipment are readily available.
- Loading and Unloading
- Train workers on the proper techniques for loading and unloading goods and materials.
- Ensure that all lifting equipment is used appropriately.
- Lighting
- Ensure that the warehouse is well-lit, and that all light fixtures are functioning properly.
- Replace burnt-out light bulbs promptly.
- Install additional lighting in areas that are particularly dark or poorly lit.
- Inspections
- Regularly inspect the warehouse for potential hazards.
- Address any issues promptly.
- Encourage workers to report any hazards they encounter.
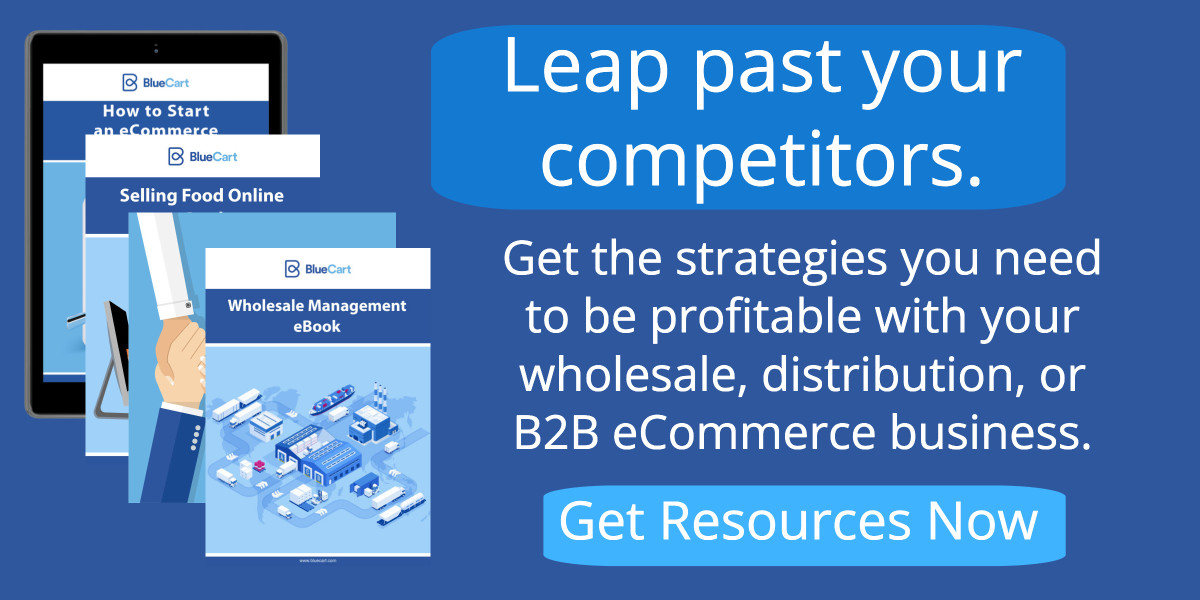
Frequently Asked Questions About Warehouse Safety Checklist
Here are some frequently asked questions about warehouse safety checklist.
What are the Safety Measures in a Warehouse?
The safety measures in a warehouse are designed to minimize risks and protect workers from potential hazards. Some of the most common safety measures include:
- Fire Prevention and Protection
- Electrical Safety
- Floor Safety
- Equipment Safety
What are OSHA Warehouse Safety Guidelines?
OSHA (Occupational Safety and Health Administration) has a number of guidelines for warehouse safety to protect workers from hazards such as slips, trips, and falls, hazardous materials, heavy machinery, and electrical dangers. Some of the key guidelines include:
- Maintaining clear aisles and walkways
- Properly storing materials to prevent collapse or tipping
- Providing adequate lighting
- Properly training employees on the use of equipment and handling of hazardous materials
- Implementing an injury and illness prevention program
- Developing and implementing emergency action and fire prevention plans
- Conducting regular safety inspections
- Properly labeling hazardous materials
- Properly maintaining and inspecting equipment
- Providing personal protective equipment (PPE) when necessary
Is it Illegal to Not Wear Safety Vests in a Warehouse?
This depends on the specific regulations in your jurisdiction and the nature of the work being performed. In general, OSHA does not have a specific regulation that requires workers to wear safety vests in a warehouse. However, OSHA does require that employers provide their workers with personal protective equipment (PPE) when necessary to protect them from hazards in the workplace.
Do you Have to Wear Safety Boots in a Warehouse?
Wearing safety boots in a warehouse also depends on the regulations in place and the nature of warehouse operations being performed. However, it is important to stay safe and wear personal protective equipment when necessary.
What Do You Think About Those Safety Boots Now?
A warehouse safety checklist is essential for ensuring a safe and hazard-free environment for workers and visitors. By implementing the measures outlined in this checklist, you can minimize risks and protect workers from potential hazards. A strong commitment to safety and a proactive approach to reducing risks will help ensure a safe and efficient warehouse operation.