There are different approaches associated with valuing your business’ inventory stock. The weighted average cost is one of those approaches that allow you to determine the average inventory cost based on each individual cost and quantity on hand.
Businesses tend to use the weighted average cost method to determine the amount that goes into the cost of goods sold and inventory. In most cases, businesses pay different prices when they purchase inventory items due to the diversity in the types of inventory stock or the same stock that is purchased at different times.
This blog post covers the specifics of the weighted average cost method and the weighted average cost formula. You will also learn about five benefits associated with the weighted average cost.
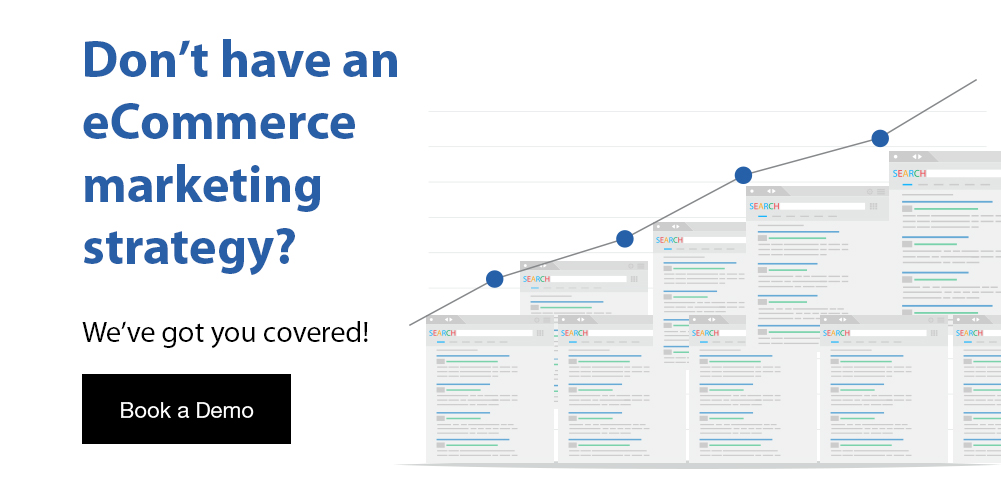
Weighted Average Cost Meaning
The meaning of weighted average cost (WAC) refers to the average cost of your inventory per unit. WAC allows retailers to understand how much each inventory item costs to purchase or produce.
To identify the WAC, businesses will need to use the weighted average cost formula. This is one metric they can use to learn about their inventory on hand.
Key Takeaway: If a business is selling similar products with multiple SKU numbers, the weighted average cost method will allow them to easily determine the inventory value and maintain accurate financial statements.
How To Calculate WAC
The weighted average cost formula is:
Weighted Average Cost = Cost of Goods Sold / Number of Units Purchased
The cost of goods sold is calculated by adding the cost of your inventory over multiple purchases. The number of units purchased refers to the total units your business purchased over the same period.
Example of the WAC Formula
To better understand the weighted average cost method, let’s take a look at an example.
A company’s inventory report states a beginning inventory of 500 units at a cost of $20 per unit at the beginning of its fiscal year on January 1.
During the first quarter, the company made the following purchases:
- January 4 - purchase of 50 units at a cost of $25 = $1,250
- February 20 - purchase of 100 units at a cost of $30 = $3,000
- March 18 - purchase of 75 units at a cost of $35 = $2,625
During this time, the company also made the following sales:
- End of February sales of 75 units
- End of March sales of 100 units
Using the periodic inventory system, you would determine the cost of goods available for sale and the units available for sale at the end of the first quarter.
During the January-March period, the sale of 175 units would allocate $23.27 per unit sold.
WAC per unit = ($10,000 + $1,250 + $3,000 + $2,625) / 725 = $23.27
The remaining would go into the ending inventory.
175 x $23.27 = $4,072.25 in Cost of Goods Sold
$16,875 - $4,072.25 = $12,802.75 in Ending Inventory
WAC vs FIFO vs LIFO
There are multiple strategies used for valuing inventory. This includes the weighted average cost as well as first-in, first-out (FIFO), and last-in, first-out (LIFO).
FIFO and LIFO are similar costing methods that are used with the weighted average cost. There are different instances where each method would be used best.
The WAC method uses the COGS divided by the total number of units in inventory. It’s best to use the weighted average cost method when it’s too complicated to determine each individual unit of inventory and the amount you’ve paid for it.
The FIFO and LIFO costing methods are useful when WAC is not useful. FIFO methods use the cost of goods sold for items that were purchased first divided by the total number of units purchased. Then, the cost of the oldest items is reported in the financial statements.
The LIFO method assumes customers are frequently purchasing the newest items of inventory in stock compared to the oldest items in stock with FIFO. A business can determine the inventory cost using LIFO by dividing the COGS of the newest items by the number of units purchased. Businesses would then record the cost of the newest items in the financial statements.
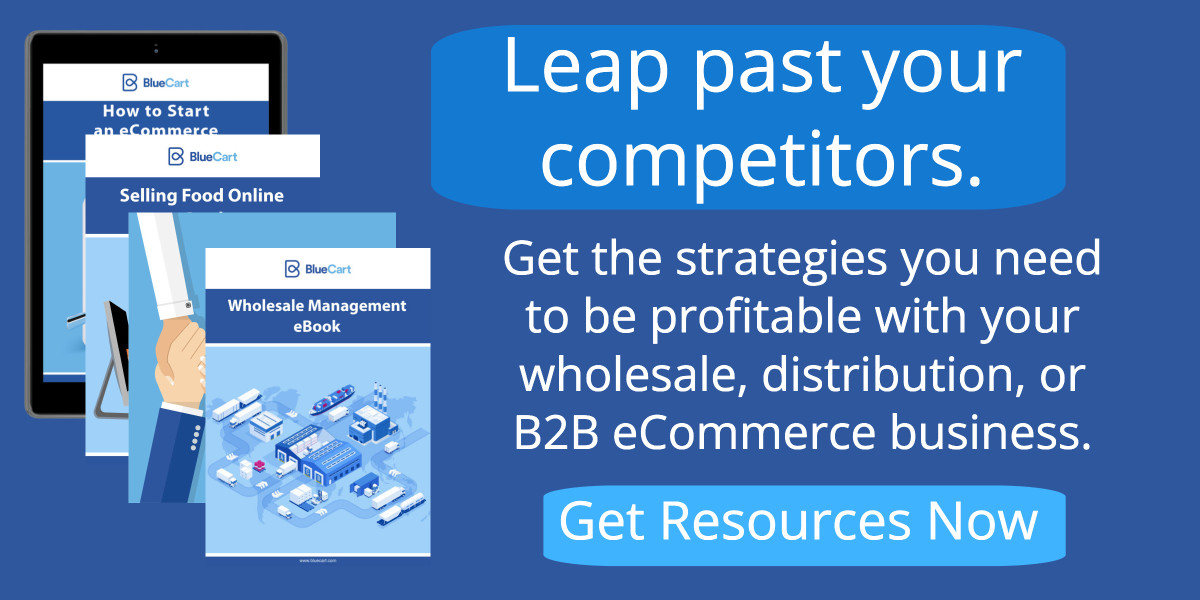
5 Benefits of WAC
There are many benefits to knowing the weighted average cost per unit. In fact, it is one of the easiest inventory tracking methods. With WAC, your business can store inventory without having to designate the batch it belongs to. It’s also not necessary to track the original cost before pricing the items.
Five benefits of weighted average cost include:
1. Less Record-Keeping
The simplicity of WAC makes it possible to save items when it comes to bookkeeping. This is because you don’t have to be exact about when you purchased your inventory and how much each item costs.
The weighted average cost method requires less paperwork and record-keeping. In fact, it requires a single cost calculation and it uses the cost for all other calculations. Other calculations may include days inventory outstanding.
As a result, you only need a single record to document the calculation. Businesses will only record the total inventory costs compared to detailed records for each purchase.
2. Inventory Value Tracking
It’s important for a business to understand the value of its inventory. The weighted average cost method makes it easy to do this.
It can be tough to know how much you paid for each item in your inventory, especially when prices fluctuate. WAC makes accounting easy by revealing the average cost of each item.
3. Saves Money
Fewer detailed records regarding the cost of each individual item and when it was sold can save businesses time. More saved time results in more saved money because you need less administrative help.
4. Improved Inventory Visibility
Businesses can improve real-time inventory visibility with weighted average cost methods. With this, they gain insight into profitability and inventory cost. This is also possible when using centralized inventory methods and an inventory scanner to track items.
Average cost valuations are superior to other valuation methods when a business is dealing with large volumes of inventory. This is also true when the products are indistinguishable from one another or when it’s time-consuming or difficult to track each individual item.
With the WAC method, you can easily see the performance of your key products. As a result, you can examine the financial results that they are associated with.
5. Simple Calculations
Calculating the WAC is simple compared to other calculations. This provides an advantage for businesses that use this method because it only requires an accountant to use three steps. Alternative methods require multiple steps to calculate the cost of goods sold or inventory value.
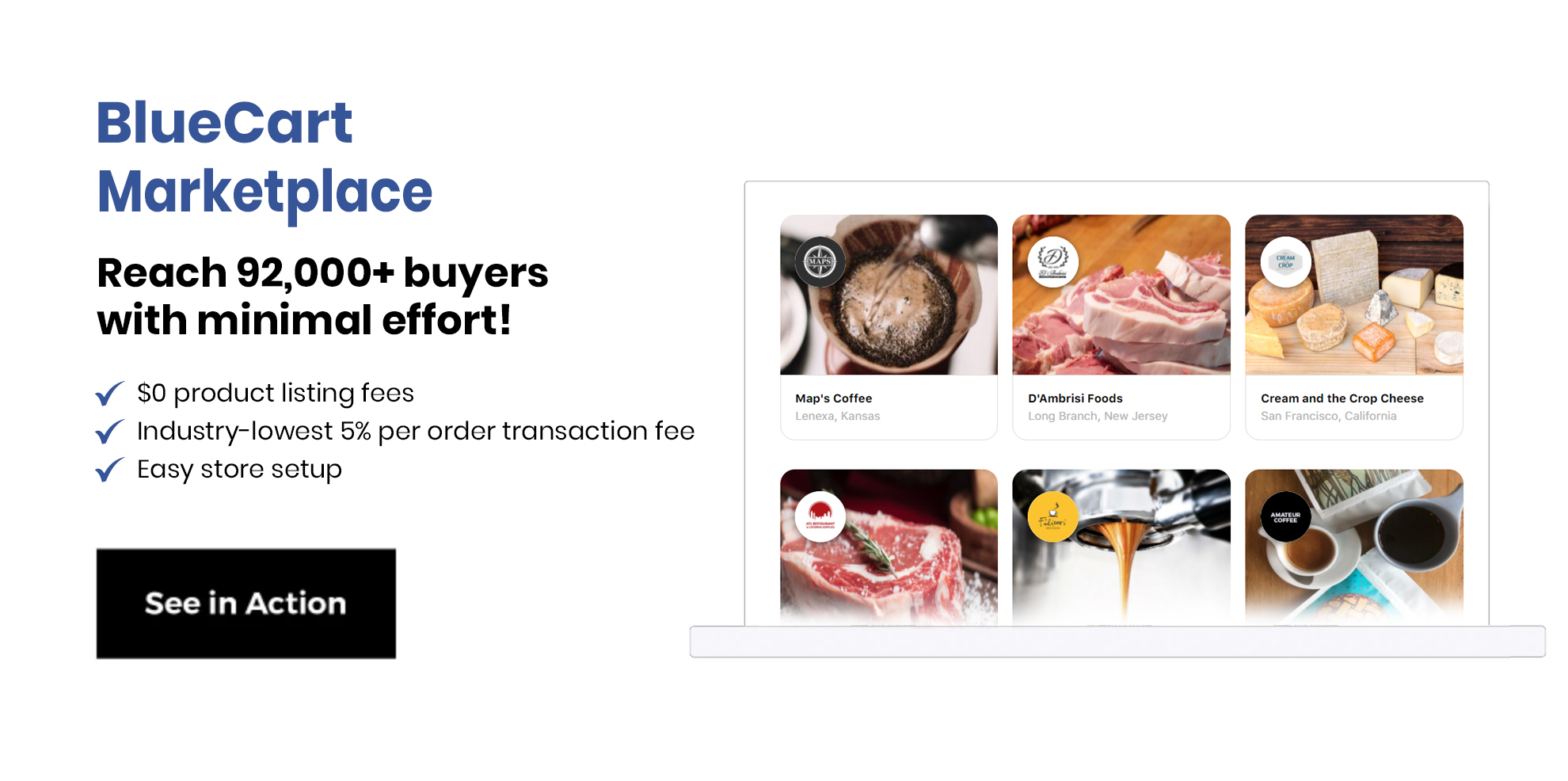
Frequently Asked Questions About WAC
It’s possible to keep track of costs using the weighted average cost per unit. This can impact your business’s prices and help save you time and money on many administrative tasks.
A business owner may use WAC with FIFO and LIFO methods to get a clearer understanding of the business. As a result, you can make more strategic business decisions regarding marketing, pricing, and inventory storage, holiday inventory management. With this information, you can avoid overselling and phantom inventory.
To further understand the weighted average cost, read the following commonly asked questions:
What Is the Weighted Average Cost Flow Method?
The weighted average cost flow method refers to methods that assign costs to inventory and the COGS. When using this method, the cost of the goods available for sale is divided by the number of units produced during a specific period to get the average cost per unit.
How Do You Calculate Weighted Average Cost?
To calculate the weighted average cost, you must divide the total cost of the goods purchased by the number of units you have available for sale. In order to find the cost of goods available for sale, you need to determine the total amount of beginning inventory and recent purchases.
Which Situation It Is Best To Use Weighted Average Method?
It’s best to use the weighted average method when it is too difficult to assign a specific cost to an individual unit of inventory. This often happens when inventory items become intertwined.