Learning how to start an eCommerce business comes with the fun of making money doing what you love. Whether you’re learning how to become a wholesaler, launching a B2B business, or prefer the fast-growing direct to consumer market, there’s a lot to take advantage of. It also includes the less fun parts, like the intricacies of warehouse organization and order management software.
In order to keep customers coming back, your shipping and handling approach needs to emphasize speed and accuracy. This is particularly important if you sell perishable goods, and need to know how to ship frozen food, how to ship cookies, and how to ship food in general. You can get a jump start on optimal shipping practices by making a chart of shipping costs by weight, based on the products you sell.
Next is where batch picking and fulfillment comes in. Instead of setting up your merchandise inventory anywhere you feel like, your inventory tracking methods should make it easy to find what’s needed at a moment’s notice.
Keep reading to learn how your pickers and packers can achieve optimal warehousing efficiency and simplify the work of eCommerce shipping companies.
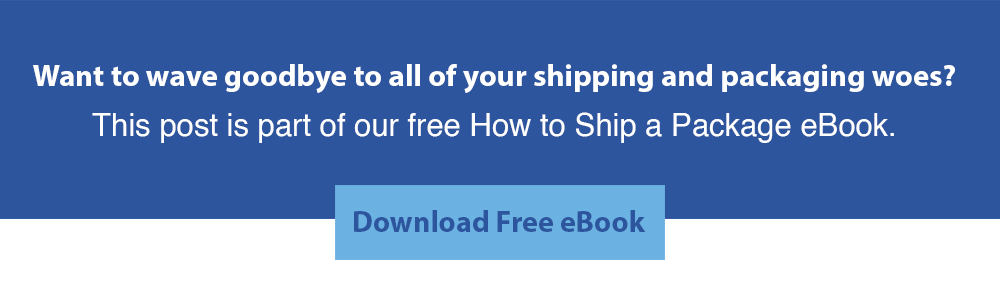
Define Batch
A batch is a group of the same products that are going into identical orders for different customers. Batching is used to speed up order fulfillment (see order fulfillment meaning),improve worker productivity (see what is warehouse job), strengthen eCommerce KPIs, and simplify inventory management.
Making sure your warehouse management process flow includes optimal batching spaces is key. Instead of going back and forth between multiple areas of the warehouse, pickers can go to one area at a time and collect as many units of a single SKU number as needed.
Product batches allow packers to complete more orders in less time. This way packers can add each product unit to separate boxes, which is especially useful if you leverage a subscription box business model.
Batching is particularly relevant if you’re buying wholesale products and using bulk shipping, both of which rely on large order volume. It’s less likely that you’ll have all the time you want to go through individual shelves, so you need a fast and reliable way to retrieve items every time.
Batching is beneficial for any eCommerce product, including high demand products and wholesale items. Whether you’re selling baked goods online, selling coffee online, selling alcohol online, or selling cookies online, you’ll find you get products to buyers much faster.
Creating a wholesale marketing plan to list your products in a wholesale directory and generate wholesale sales is ideal for batching. Since minimum order quantity (MOQ) is the name of the game when it comes to wholesaling, you’ll need a streamlined system for getting orders out on time.
What Does Fulfillment Batching Mean?
Fulfillment batching is the process of grouping multiple packaged orders that will be shipped out simultaneously. This prevents any wasted effort of loading individual packages onto trucks each time.
The fulfillment batching process is useful for multiple reasons:
- It streamlines shipping activities. Packers can set boxed items at the end of the packing station instead of walking back and forth between the shipping dock every time. Make sure you and your staff have learned how to measure a box for shipping beforehand.
- It makes the work of eCommerce shipping services simpler. Instead of wondering if they’ve received all the packages for the day, your transportation or 3PL partner (see what is 3PL) can quickly identify which order batches need to be loaded up.
- It saves time. When orders get packed efficiently, it creates room for other activities. Rather than cleaning, restocking, or maintenance only taking place when something is missing or broken, it’s easier to create time for it during the workday.
Fulfillment batching empowers staff to be focused, diligent, and productive throughout their entire day. They don’t need to wonder where to go next or whether or not their work will get done, because they tackle it in strategic bursts.
Batch Picking vs. Order Picking
Batch picking is retrieving multiple product units for different orders. Order picking is retrieving each item needed for one order at a time. Either method works, but in most cases, batch picking is both faster and more effective.
The key difference between the two methods is which products are picked from warehouse shelves. Batching is selecting one type of product for multiple orders, whereas regular order picking is picking one complete order at a time. The latter may or may not include different products, but often does.
If you have a small warehouse, order picking may sometimes be effective. The closer your shelves are to eCommerce packaging, the less time is spent across picking, packing, and staging for shipping.
However, if your warehouse takes up a large amount of space, it’s a lot harder to justify order picking (unless you sell big products and are learning how to ship large items). It’s far simpler to provide each picker with a batch picking list so they can fulfill multiple orders’ needs more efficiently. Many modern facilities use warehouse inventory management software, which prevents paper lists and provides for easier order updating.
Batch picking is similar to kitting, which is the process of putting related products together in the same package. You can increase eCommerce sales by kitting with custom subscription boxes. Buyers are happy to pay more for products they love if similar products are sold together.
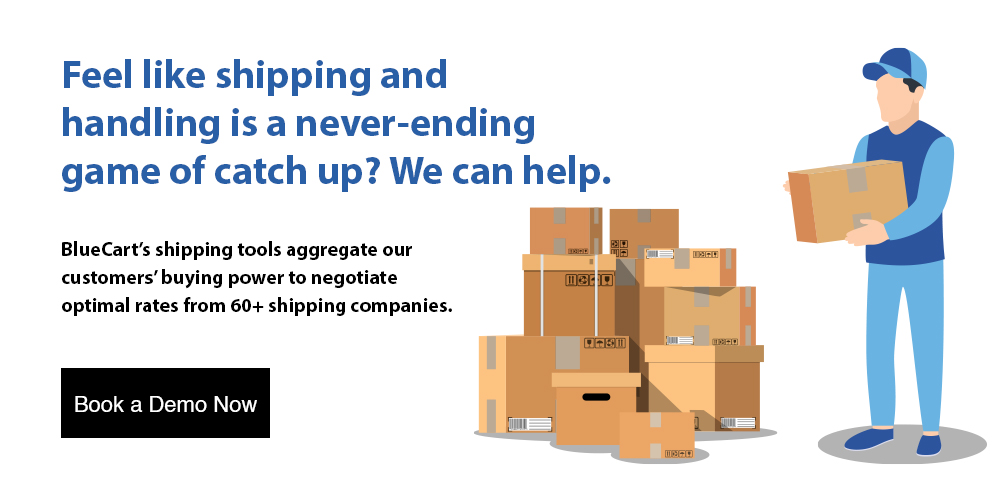
Batch Order
A batch order is a list of the products and units needed to fulfill similar orders to different customers. It’s closely related to batch picking, and usually the two work hand in hand. The process of batch ordering is made simpler when you have the right eCommerce software on hand, like a warehouse management system (WMS).
Batch ordering is the process of grouping similar customer requests and providing this to warehouse staff for daily work. This process is perfected over time as different warehouse employees memorize locations and master their work.
Batch Picking
Batch picking is when a warehouse picker retrieves multiple identical product units for different orders. It’s the process of grouping a product quantity at one time so that particular product can be assigned to separate orders at a packing station.
If your warehouse is particularly large, you may have pickers dedicated for a specific product range or work shift. This can work well as it doesn’t overburden workers for specific objectives.
You may consider incorporating batch returns, as well. To do this, all of your customers' orders should include two bits of information: a packing slip and an RMA number. A packing slip details all of the products included in a single order, and an RMA number is the digit used to process a return. It stands for return merchandise authorization, and tracks the reverse delivery of a returned product.
Order Picking
Order picking is the process of selecting each item in an order on an individual basis. The order picking method is what many warehouses utilize unless they have a better order processing approach in motion.
Order picking often requires walking back and forth between multiple areas of a warehouse. This uses a lot of time and requires employees to memorize various locations with remarkable accuracy. Unless you have some experienced pickers, a warehouse manager job description should include implementing smarter plans for peak labor efficiency.
Since it’s impossible to know what products a customer requests until an order is generated, it’s wise to have an efficient plan in place. Asking each picker to go around the warehouse multiple times for different orders expends a lot of time and increases the likelihood of mistakes.
Frequently Asked Questions About Fulfillment Batching
If you’ve never done fulfillment batching before, it may appear a little confusing. When used properly, it saves your business oodles of time and money. Here are some commonly asked questions about it and our answers:
What is a batch order USPS?
A USPS batch order is when you submit information from numerous orders that you want to ship at the same time. It’s a way of processing several customers’ info that will all go out on the same day.
What does fulfillment status mean?
Fulfillment status is the shipping stage a package is currently in. eCommerce shipping companies may use slightly different terms to indicate where a package is, but you’ll know where packages are based on their tracking numbers.
For example, a package with the status of “not fulfilled” means processing hasn’t started and it’s waiting to be picked up. Terms like “processing” or “fulfilled” means an item is on its way to the carrier, “in transit” indicates it’s on its way, and “delivered” means it reached the customer.
How do I ship multiple packages UPS?
UPS allows you to ship multiple packages at once by registering for a free account. Once signed up and logged into your account, you can set your preferences for one-step shipping and use their shipping cost estimator.
With one-step shipping, all you need to do is confirm customer information on the label, turn on your shipping label printer, and start printing. This saves a lot of time and makes it easy to learn how to print shipping labels from home. It also gives you more time to focus on equally important tasks, like marketing or warehousing.
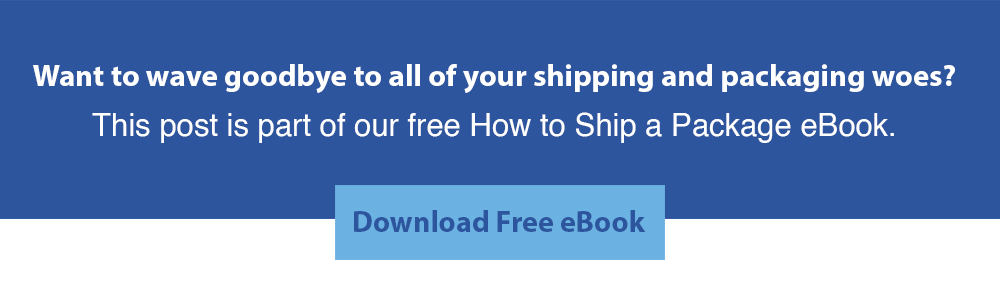
Serving Up a Batch of eCommerce Success
When more than two thirds of modern consumers see fast shipping as a deciding factor in buying, you know it’s something to pay attention to. Having a batching system in place is that hidden key of order management you’ve been looking for. It supports both smooth daily operations and fewer delays in shipping products to customers.