Is your work in process inventory—or WIP inventory—minimized?
Supply chain and managing all types of inventory are established fields of expertise now. And one thing that these professions agree on is that it’s usually best to minimize work in process inventory.
The more WIP inventory you have:
- The less storage space is available for your most profitable items
- The more capital you have tied up in unsaleable items
- The higher the risk of incomplete goods expiring or becoming obsolete
Figuring out WIP inventory is an involved process because it involves associating a cost with a percentage of completion. That’s not easy to do. And that’s why it’s standard practice to minimize WIP inventory before reporting. There’s less risk to assume and less uncertainty to wrestle with on the balance sheet.
The more you learn about WIP inventory, the easier it will be to body slam it into submission. Let’s get ready to rumble.
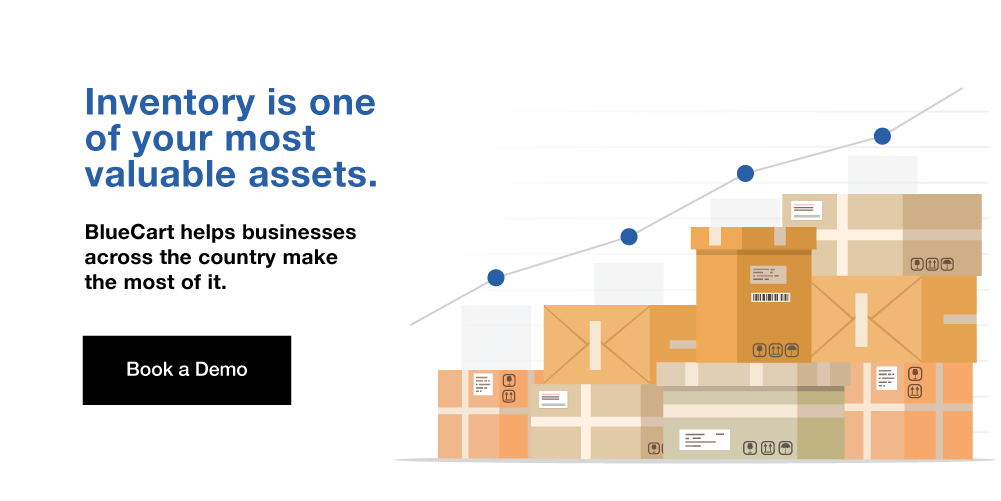
What Is Work In Process Inventory Generally Described As
Work in process inventory is generally described as a company’s unfinished goods waiting to be completed and sold. The standard work in process inventory definition is all the raw material, overhead costs, and labor associated with every stage of the production process.
Any raw material inventory that has been combined with human labor but is not yet finished goods inventory is work in process inventory. That makes it a part of manufacturing inventory (see what is inventory). Think everything after raw material inventory and before finished product inventory. It’s all the production costs incurred for all partially-completed goods. Another title for work in process inventory is work in progress inventory (both abbreviated WIP inventory).
Why Does Work In Process Inventory Exist?
The above work in process inventory definition explains the what, but not the why. Why do companies have partially completed inventory? A few reasons.
The most obvious is that the items are in the process of being produced. They may be on a conveyor belt in the act of fabrication or they may be waiting in a queue for further processing. Either way, they are actively being created.
Another reason for work in process inventory is safety stock, buffer stock, or anticipation inventory. Some companies find it beneficial to hold on to goods at certain stages of production as insurance against shortages of supply or spikes in demand. Vendor managed inventory agreements are often helpful in determining the right purchase orders to protect against supply chain surprises.
Work In Process vs Work In Progress Inventory
Work in process inventory and work in progress inventory are interchangeable phrases, for the most part. Though some within supply chain management do make a small distinction between them. Some folks refer to work in process inventory only in the context of production operations that move along relatively quickly. They reserve work in progress for larger-scale projects like consulting or construction work.
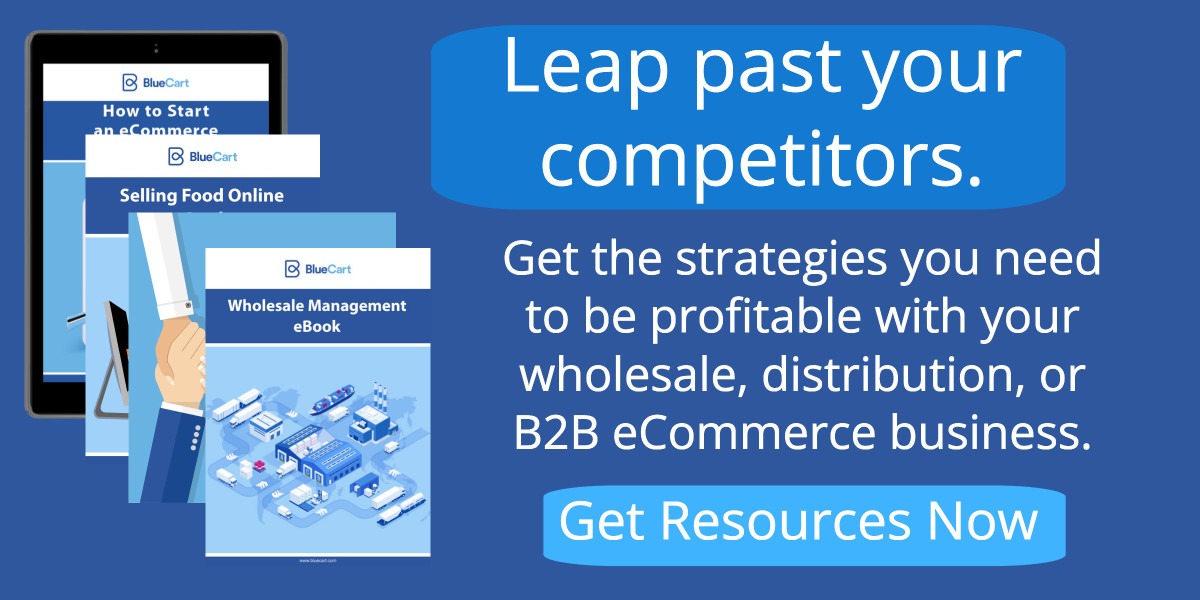
Quiz: Work In Process Inventory Increases When …
Let’s see if you’ve fundamentally understood what work in process inventory is. Here’s a quiz.
Work in process inventory increases when:
- Products are finished and turned into in transit inventory
- Raw materials are purchased
- Raw materials are used
- Finished products, or merchandise inventory, are sold
If you chose C, you’re correct. Nice work!
Examples of Work in Process Inventory Goods
Companies that sell products with high added value have a lot of goods in their work-in-process inventory. Let’s check some examples.
- A feed mill. Manufacturers of livestock feed purchase various types of grains, wholesale legumes, and other products. When they stay in storage, these goods fall under the raw materials category. But once they leave storage and the manufacturing process starts, they become part of the work-in-process inventory.
- A beauty subscription box company. The subscription business model has become very popular in the last couple of years. A company that offers its skincare and beauty products in subscription boxes will have a lot of work-in-progress inventory. That includes items such as bags, boxes, packaging materials, bottles for the products, the solutions, and more.
- A coffee roastery. Even if they sell just coffee, they have a lot of products in their work-in-progress inventory. That includes the actual roasted coffee beans, packaging bags, and branded labels.
How to Calculate Work In Process Inventory
For the majority of manufacturers, WIP inventory is the raw materials plus labor and production overhead. For more complex operations—like big constructions projects—it can include wages, subcontractor costs, and more. Regardless, it takes time to figure out. Again, that’s why most manufacturers minimize WIP before they tally it up at the end of the accounting period.
How to Find Beginning Work In Process Inventory
Beginning work in process inventory is actually the same thing as ending work in process inventory, just for a different accounting period.
Businesses always calculate WIP inventory at the end of accounting periods, whether that be a quarter, year, or some other time period. This total WIP figure is the ending work in process inventory for that accounting period—and the beginning work in process inventory for the next accounting period.
This ending WIP inventory is listed as a current asset on your company’s current balance sheet. So, to figure out how to find work in process inventory you need the beginning work in process inventory. And to calculate that, you need the ending work in process inventory.
How to Calculate Ending Work In Process Inventory
The work in process formula is:
Ending WIP Inventory = Beginning WIP Inventory + Manufacturing Costs - Cost of Finished Goods
Let’s use a best coffee roaster as an example.
Imagine BlueCart Coffee Co. has a beginning work in process inventory for the quarter of $10,000. This refers to all the bags, labels, beans yet-to-be-ground, and other raw materials waiting to be turned into finished bags of coffee ready for sale.
Over the next three months, the company incurs production costs of $75,000 roasting, grinding, and packaging coffee beans. The total value of the finished goods over the quarter is $72,000.
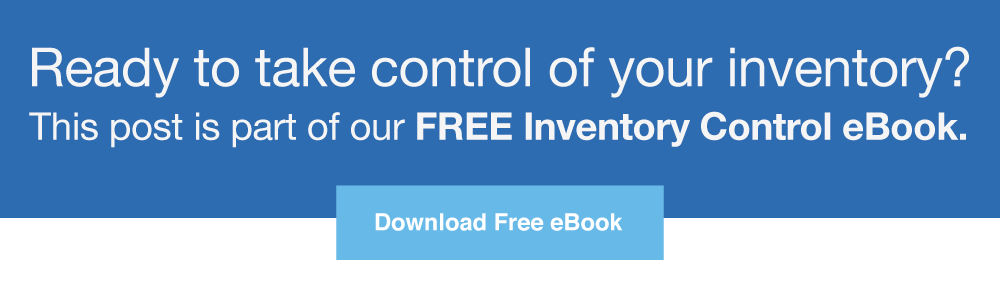
Ending WIP Inventory = Beginning WIP Inventory + Manufacturing Costs - Cost of Finished Goods
Ending WIP Inventory = $10,000 + $75,000 - $72,000
Ending WIP Inventory = $13,000
This means BlueCart Coffee Co. has $13,000 worth of inventory that’s neither raw material nor finished goods. For a perishable item like coffee, growing WIP inventory figures are a red flag unless they’re strategically kept as anticipation inventory.
Keep in mind that this work in process formula is an estimate. There are things it doesn’t consider, like waste, spoilage, downtime, scrap, and MRO inventory. To get a totally accurate WIP inventory is unreasonable. It would require combing through the production process and itemizing every little inevitability. In general, companies calculate estimated WIP inventory levels. It’s better than nothing.
Work In Process Inventory Journal Entry
Keeping tabs on your work in process inventory requires some bookkeeping. If you’re not an accountant, you may wonder how a work in process inventory journal entry looks. Here’s a simple example that shows how records shift from debits to credits throughout the production cycle.
In this example, your initial purchase of $5,000 of raw material which is debited to your raw materials inventory. You’d then credit your accounts payable for the same amount.
Once the raw materials enter the production cycle, that $5,000 debit is moved to the WIP inventory account and the raw materials account is credited with $5,000.
And, finally, once the WIP inventory becomes finished goods, the $5,000 is debited to the finished good account and $5,000 is credited back to the WIP inventory account.
Trust the Process
Understanding WIP inventory is crucial for monitoring and improving production capacity and inventory control. Unless you’re holding on to a substantial amount of WIP inventory is a part of a strategic anticipatory inventory management strategy. Otherwise, it’s not ideal to let it grow.
That’s because a business’s sustained WIP inventory plays a big part in the valuation of their business. And approval of any loans they apply for. WIP isn’t immediately sales-ready and, while it counts as a current asset, isn’t very liquid. Loan companies are hesitant to consider WIP inventory as collateral. If you can't calculate your WIP, you won't deserve that warehouse manager salary.
“Large” and “small” aren’t good gauges of healthy WIP inventory. Consistency relative to sales is a better benchmark. If your WIP inventory remains consistent or contracts without resulting sales loss, it’s a sign that your production operations are smooth. But If it continually grows without an associated growth in sales, it’s a sign of inefficiency. You can then focus on optimizing your shipping to make even more money. Route optimization software is great for that, especially a multi-stop route planner.
You should also look into using a wholesale marketplace to find suppliers who can fill orders more quickly or even list your own products for sale.
Frequently Asked Questions About Work In Process Inventory
Work in process inventory can be difficult to understand outside of proper context. If you’re optimizing your warehousing practices or learning more about inventory, you probably have several questions. Check out these commonly asked work in process questions below:
What is the Work in Process Inventory Formula
The work in process inventory formula is the Beginning WIP Inventory + Manufacturing Costs – COGM. This calculation will give you the end work in process inventory.
What is another title for Work in Process Inventory?
Another title for work in process inventory is WIP Inventory.
How do you find beginning work in process inventory?
Your beginning work in process (WIP) inventory is your previous accounting period’s ending WIP inventory. You can carry it over from the previous month and use it as the current month’s starting WIP inventory.
If you still need to find your beginning WIP inventory, you can do so with a formula. The calculation is your cost of goods sold (COGS), plus your ending inventory balance, minus your cost of purchases. If you don’t have an ending inventory balance to include, simply subtract your cost of purchases.
As an example, let’s say your current COGS is $5,000, your ending inventory balance is $9,642.40, and your cost of purchases is $8.924.10. With the formula above, this would give you a beginning work in process inventory of $5,718.30.
What Is the Formula for the Cost of Manufactured Goods?
Cost of manufactured goods (COGM) = total manufacturing costs + beginning work in process inventory – ending work in process inventory. Thanks to this formula, businesses can calculate the total cost of making a final product. The formula can also be used to determine the total amount of work in process inventory as long as the business knows the COGM, total manufacturing costs and the beginning WIP inventory.
The COGM formula is also useful when calculating the total COGS (cost of goods sold) for a said period of time (usually a year).
What Is the Formula for Manufacturing Costs?
Manufacturing costs = raw materials + manufacturing overhead + labor costs. Businesses can use this formula in order to calculate how much the price of manufacturing products is. Manufactured costs should not be confused with the cost of manufactured goods.
How to Optimize Work in Process Inventory?
There are multiple ways to optimize inventory management. That’s also true for work-in-process inventory. Here are some examples of ways to optimize work in process inventory.
- Reduce waste by implementing JIT (just-in-time) manufacturing which excludes excess work in process inventory;
- Integrate forecast demand solutions which can help your business prepare for peak seasons and slow months;
- Use automation software such as ERP and MES (manufacturing execution systems). These solutions can monitor inventory levels and production schedules in order to have better visibility and understanding of optimal work in process inventory levels;
- Improve supply chain coordination by partnering with the right suppliers or outsourcing certain processes to 3PL providers or other companies;
- Analyze and eliminate production bottlenecks that might lead to suboptimal inventory levels or imbalances across the business.
What Are the Other Types of Inventory?
There are three main types of inventory. One of them is work-in-process inventory. Let’s see the other two.
- Raw materials. As the name suggests, this type of inventory consists of raw materials that are in storage. They have not yet been a part of the manufacturing process. Once they go out of storage and on the production lines, they become part of the work-in-process inventory.
- Finished goods. Once the products are ready to be sold or shipped, they become part of the finished goods inventory. Often these products are not packaged, but in some cases, depending on the business processes, they can be packaged and ready to be shipped.
Although these are the three major types of inventory, there are other categories as well. Here are a few additional types:
- Maintenance, repair, and operations (MRO) goods;
- Packaging materials;
- Anticipation stock;
- Transit inventory;
- Excess inventory;
Is work in process inventory?
Yes, work in process (WIP) inventory is considered inventory. Any part, product, or item that’s used to make merchandise inventory is listed on a company’s balance sheet. WIP inventory is considered an inventory asset, and as it moves through the stages of production, it becomes part of the cost of sales.
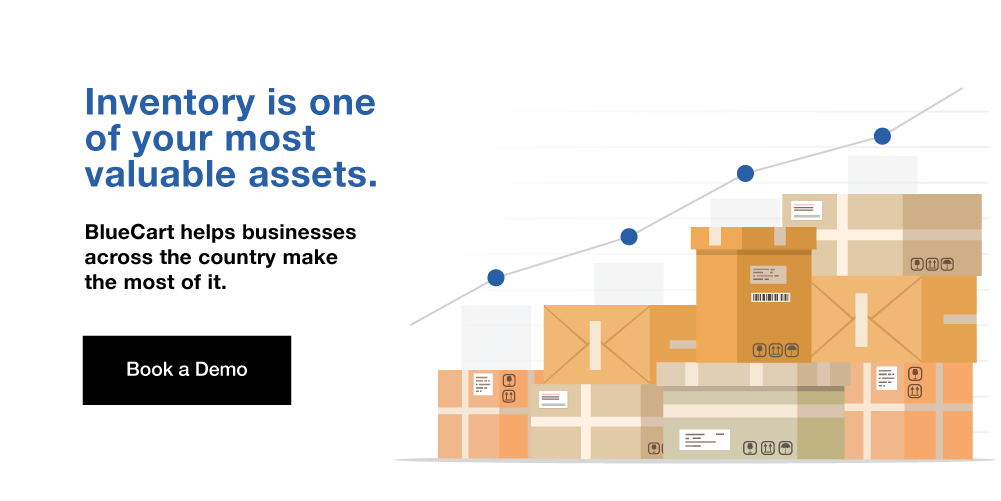
What is included in work in process inventory?
Work in process (WIP) inventory includes all raw goods, production expenses, and labor costs associated with producing merchandise inventory. Adding the totals of these categories will give you your current work in process inventory.
Is the Work in Progress Formula the Same as the WIP Formula?
Yes. The work-in-progress formula is the same as the work-in-process inventory formula. The two terms are used interchangeably.
Why Is the Work in Progress Formula Important?
By calculating the work in progress (WIP) inventory, businesses can better track the quantity of their partially completed products and get insights into the efficiency of the manufacturing process. By calculating work-in-progress inventory properly, companies can have a better understanding of the need to allocate material and labor to different parts of the business. Furthermore, the different work-in-progress formulas can help discover production bottlenecks and improve the overall workflow. In order to do so, businesses can analyze all the different stages of the manufacturing process.
How Long Should Inventory Stay in the WIP Stage?
The time it takes for raw materials to become end products varies significantly based on the type of manufacturing. Generally speaking, complex products stay in the work-in-progress stage longer compared to simple products. Manufacturers of large and complicated products can divide their WIP stage into multiple smaller stages. This will help them better analyze and optimize the production process, increase efficiency, and reduce bottlenecks.